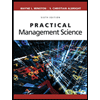
Practical Management Science
6th Edition
ISBN: 9781337406659
Author: WINSTON, Wayne L.
Publisher: Cengage,
expand_more
expand_more
format_list_bulleted
Concept explainers
Topic Video
Question
Earthbound Corporation is a manufacturer and distributor of air conditioning systems. You have been engaged to install an accounting system for Earthbound period among the inventory control features earthbound desires as part of the system are indicators of how much to order and when period.
The following information is furnished for a product called “Hydronix” which is carried in inventory:
- Hydronix are sold by the gross (12 dozen) at a list price of P800 per gross FOB shipper. John receives a 40% trade discount off list price on purchases in gross lots.
- Freight cost is P20 gross from the shipping point to John's plant
- John uses about 5,000 Hydronix during 259-day production year and must purchase a total of 36 gross per year to allow for normal breakage. Minimum and maximum usages are 12 and 28, respectively.
- It takes 20 working days (normal delivery time) to receive an order from the date the purchase request is initiated. A rush order in full gross lots can be received by air freight in 5 working days at an extra cost of P52 per gross. A stockout (complete exhaustion of inventory) of Hydronix would stop production and John would purchase Hydronix locally at list price rather than shut-down.
- The cost of placing an order is P10, the cost of receiving an order is P20.
- Space storage cost is P12 per year gross stored
- Insurance and taxes are approximately 12% of the net delivered cost of average inventory and John expects a return of at least 8% on its average investment (ignore return on order and carrying cost for simplicity).
Required:
- Calculate the total annual cost of Hydronix based on uniform order lot sizes of one, two, three, four, five, and six gross of Hydronix. Indicate the economic order quantity (economic lot size) to order.
- Calculate the minimum stock reorder point for Hydronix. This is the point below which the Hydronix inventory should not fall without reordering so as to guard against stockout. Factors to be considered include average lead-period usage and safety stock requirements.
- Calculate the cost of stockout of Hydronix. Factors to be considered include the excess costs for local purchases and for rush orders.
Expert Solution

This question has been solved!
Explore an expertly crafted, step-by-step solution for a thorough understanding of key concepts.
This is a popular solution
Trending nowThis is a popular solution!
Step by stepSolved in 2 steps with 2 images

Knowledge Booster
Learn more about
Need a deep-dive on the concept behind this application? Look no further. Learn more about this topic, operations-management and related others by exploring similar questions and additional content below.Similar questions
- Jill's Job Shop buys two parts (Tegdiws and Widgets) for use in its production system from two different suppliers. The parts are needed throughout the entire 52-week year. Tegdiws are used at a relatively constant rate and are ordered whenever the remaining quantity drops to the reorder level. Widgets are ordered from a supplier who stops by every three weeks. Data for both products are as follows: A. Find the total inventory costs if using inventory policy. This is a case considering safety stock (make sure to use the right formula)arrow_forward32) ABC Shop ABC shop uses glue at a daily rate that is normally distributed with a mean of 250 ounces and a standard deviation of 26 ounces. When the shop places an order for glue it requires 9 days for the order to arrive. What is the Reorder Point if the shop wants an 84% Service Level? Round to an integer value. Group of answer choices a) 2,347 ounces b) 1,538 ounces c) 1,967 ounces d) 2,307 ounces e) 2,327 ounces f) 1,558 ouncesarrow_forwardThe sales of Whole Care mouthwash at Jen's of Michigan over the past six months have averaged 2,000 cases per month, which is the current order quantity. Jen's of Michigan's cost is $12.00 per case, and ordering cost is $38. The company estimates its cost of capital to be 12 percent. Insurance, taxes, breakage, handling, and pilferage are estimated to be approximately 6 percent of the item cost. Lead time is 3 days, and considering weekends and holidays, Tom's of Maine operates 250 days per year. Based on the above information please answer the following questions What is EOQ? What is the cost reduction? What is the reorder point? What is Time between Orders (TBO)?arrow_forward
- 40) PLEASE HELP WITH THIS! Gentle Ben's Bar and Restaurant uses 5,000 quart bottles of an imported wine each year. The effervescent wine costs $3 per bottle and Is served only in whole bottles because it loses its bubbles quickly. Ben figures that it costs $10 each time an order is placed, and holding costs are 20 percent of the purchase price. It takes three weeks for an order to arrive. Weekly demand is 100 bottles (closed two weeks per year) with a standard devlation of 30 bottles. Ben would like to use an inventory system that minimizes inventory cost and will provide a 95 percent service probability. b. At what inventory level should he place an order? Note: Use Excel's NORM.S.IN( function to find the z value. Round z value to 2 decimal places and final answer to the nearest whole number.arrow_forwardGiven the following information, formulate an inventory management system. The item is demanded 50 weeks a year. PARAMETER Item cost Order cost Annual holding cost Annual demand Average weekly demand Standard deviation of weekly demand. Lead time. Service probability Optimal order quantity Reorder point units units VALUE $12.00 $194.00/order 21% of item cost 24,700 units 494 /week 20 units 2 week 95% a. Determine the order quantity and reorder point. (Use Excel's NORMSINV() function to find your z-value and then round that z- value to 2 decimal places. Do not round any other intermediate calculations. Round your final answers to the nearest whole number.)arrow_forwardSam's Pet Hotel operates 52 weeks per year, 6 days per week, and uses a continuous review inventory system. It purchases kitty litter for $13.00 per bag. The following information is available about these bags: ≻Demand=75 bags/week ≻Order cost=$55.00/order ≻Annual holding cost=25 percent of cost ≻Desired cycle-service level=80 percent ≻Lead time=4 weeks (24 working days) ≻Standard deviation of weekly demand=15 bags ≻Current on-hand inventory is 320 bags, with no open orders or backorders. Part 2 a. Suppose that the weekly demand forecast of 75 bags is incorrect and actual demand averages only 50 bags per week. How much higher will total costs be, owing to the distorted EOQ caused by this forecast error? The costs will be $enter your response here higher owing to the error in EOQ. (Enter your response rounded to two decimal places.) a. What is the EOQ? What would the average time between orders (in weeks)? b. What should R be? c. An inventory withdraw…arrow_forward
- PART A Speedy Bicycle Company (SBC) is a wholesale distributor of a wide variety of bicycles and bicycle parts. The most popular model is the Dragonfly, which sells for $170. All manufacturing is done at a plant in China, and shipment takes a month (30 days) from the time an order is placed. The estimated order cost is $75, including customs clearance. SBC's cost per bicycle is 65% of retail price, and inventory carrying cost is 11% per year of SBC's cost. If the company cannot fulfill a retail order, the retailer will get the shipment from another distributor and SBC loses that business. SBC is planning inventory for 2023 based on forecasted demand and wants to maintain a 93% service level to minimize lost orders. The company has 300 working days per year. 2021 Forecasted Demand for the Dragonfly Bicycle Model: F A J 15 58 J 8 M 31 M 96 J 59 38 A 23 S 16 0 14 N 26 D 41arrow_forwardThe distribution manager for Putnam Corporation is trying to establish the most economic ordering policy for the standard model of its best-selling microwave oven. He has control of the finished goods warehouse for the factory and must satisfy wholesaler demand. The following information is available: Wholesale value $100 Annual demand 50,000 units Std. Deviation of Demand 30 units per day Working year 250 days Production lead time 9 days Ordering cost for production $1,800 Holding cost per unit per year 20% of value Desired service level 96 percent: If Putnam wishes to use the periodic review system, what should be the safety stock, reorder point? If the current on hand inventory is 1,000 units, how many units should be ordered?arrow_forwardGainesville Cigar stocks Cuban cigars that have variable lead times because of the difficulty in importing the product: Lead time is normally distributed with an average of 4 weeks and a standard deviation of 2 weeks. Demand is also a variable and normally distributed with a mean of 225 cigars per week and a standard deviation of 25 cigars. Refer to the standard normal table for z-values. This exercise contains only parts a and b. a) For a 95% service level, what is the ROP? The reorder point is cigars (round your response to the nearest whole number).arrow_forward
- EOQ, reorder point, and safety stock Alexis Company uses 937units of a product per year on a continuous basis. The product has a fixed cost of $44 per order, and its carrying cost is $4 per unit per year. It takes 5 days to receive a shipment after an order is placed, and the firm wishes to hold 10 days' usage in inventory as a safety stock. a. Calculate the EOQ. b. Determine the average level of inventory. (Note: Use a 365-day year to calculate daily usage.) c. Determine the reorder point. d. Indicate which of the following variables change if the firm does not hold the safety stock: (1) order cost, (2) carrying cost, (3) total inventory cost, (4) reorder point, (5) economic order quantity.arrow_forwardMac-in-the-Box, Inc., sells computer equipment by mail andtelephone order. Mac sells 1,200 flat-bed scanners per year.Ordering cost is $300, and annual holding cost is 16 percentof the item’s price. The scanner manufacturer offers thefollowing price structure to Mac-in-the-Box: What order quantity minimizes total annual costs?arrow_forwardUniversity Drug Pharmaceuticals orders its antibiotics every two weeks (14 days) when a salesperson visits from one of the pharmaceutical companies. Tetracycline is one of its most prescribed antibiotics, with average daily demand of 2,000 capsules. The standard deviation of daily demand was derived from examining prescriptions filled over the past three months and was found to be 800 capsules. It takes f ive days for the order to arrive. University Drug would like to satisfy 99 percent of the prescriptions. The salesperson just arrived, and there are currently 25,000 capsules in stock.How many capsules should be ordered?arrow_forward
arrow_back_ios
SEE MORE QUESTIONS
arrow_forward_ios
Recommended textbooks for you
- Practical Management ScienceOperations ManagementISBN:9781337406659Author:WINSTON, Wayne L.Publisher:Cengage,Operations ManagementOperations ManagementISBN:9781259667473Author:William J StevensonPublisher:McGraw-Hill EducationOperations and Supply Chain Management (Mcgraw-hi...Operations ManagementISBN:9781259666100Author:F. Robert Jacobs, Richard B ChasePublisher:McGraw-Hill Education
- Purchasing and Supply Chain ManagementOperations ManagementISBN:9781285869681Author:Robert M. Monczka, Robert B. Handfield, Larry C. Giunipero, James L. PattersonPublisher:Cengage LearningProduction and Operations Analysis, Seventh Editi...Operations ManagementISBN:9781478623069Author:Steven Nahmias, Tava Lennon OlsenPublisher:Waveland Press, Inc.
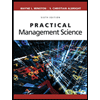
Practical Management Science
Operations Management
ISBN:9781337406659
Author:WINSTON, Wayne L.
Publisher:Cengage,
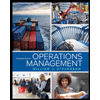
Operations Management
Operations Management
ISBN:9781259667473
Author:William J Stevenson
Publisher:McGraw-Hill Education
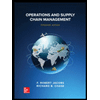
Operations and Supply Chain Management (Mcgraw-hi...
Operations Management
ISBN:9781259666100
Author:F. Robert Jacobs, Richard B Chase
Publisher:McGraw-Hill Education
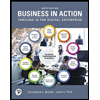
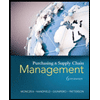
Purchasing and Supply Chain Management
Operations Management
ISBN:9781285869681
Author:Robert M. Monczka, Robert B. Handfield, Larry C. Giunipero, James L. Patterson
Publisher:Cengage Learning
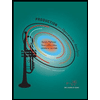
Production and Operations Analysis, Seventh Editi...
Operations Management
ISBN:9781478623069
Author:Steven Nahmias, Tava Lennon Olsen
Publisher:Waveland Press, Inc.