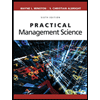
Practical Management Science
6th Edition
ISBN: 9781337406659
Author: WINSTON, Wayne L.
Publisher: Cengage,
expand_more
expand_more
format_list_bulleted
Concept explainers
Topic Video
Question
I need question D solved please
(a) What was their average aggregate inventory value? =46,410,239
(b) What was their average inventory (measured in weeks of supply)? =6.97
(c) What was their inventory turnover?=7.1771
BIT operates on a build-to-stock policy, and therefore stores its finished
goods in a warehouse capable of housing up to 70,000 units. Its annual overhead cost (fixed cost) is $117,000; and it costs $3/unit to house the finished goods. BIT has been approached by a warehouse company offering to house the finished goods for a unit cost of $4.5/unit, with an annual contract cost of $30,000.
(d) Should BIT continue operating its own warehouse, or should it employ
the warehouse company? Why?
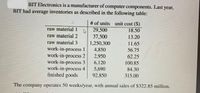
Transcribed Image Text:BIT Electronics is a manufacturer of computer components. Last year,
BIT had average inventories as described in the following table:
# of units unit cost ($)
29,500
raw material 1
18.50
raw material 2
37,500
13.20
raw material 3
work-in-process 1
work-in-process 2
work-in-process 3
work-in-process 4
finished goods
1,250,300
11.65
4,850
56.75
2,950
62.25
6,120
100.85
5,690
92,850
84.30
315.00
The company operates 50 weeks/year, with annual sales of $322.85 million.
Expert Solution

This question has been solved!
Explore an expertly crafted, step-by-step solution for a thorough understanding of key concepts.
Step by stepSolved in 2 steps

Knowledge Booster
Learn more about
Need a deep-dive on the concept behind this application? Look no further. Learn more about this topic, operations-management and related others by exploring similar questions and additional content below.Similar questions
- Current decision to buy: Ross White's machine shop uses 200 brackets each month during the course of a year. This usage is relatively constant throughout the year. Currently, these brackets are purchased from a supplier 100 miles away for $16 each and the lead time is 2 days. The holding cost per bracket per year is $1.60 (10% of the unit cost) and the annual ordering cost per order is $18.50. There are 240 working days per year. Possible future decision to make in-house: Ross White is reconsidering his decision of buying the brackets and is considering making the brackets in-house. He has determined the set up costs would be $24.50 in machinist time and lost production time. Forty eight brackets could be produced in a day once the machine has been set up. Ross estimates that the cost (including labor and materials) of producing one bracket would be $14.85. The holding cost would be 10% of the cost. a. What is the EOQ given Ross' current decision to buy the brackets? What is the total…arrow_forwardArrow Distributing Corp. likes to track inventory by using weeks of supply as well as by inventory turnover. Arrow Distributing Corp. Net Revenue $15,630 Cost of sales $12,190 Inventory $1,090 Total assets $8,770 a) What is its weeks of supply? weeks (round your response to two decimal places). b) What is Arrow's inventory turnover? times per year (round your response to two decimal places). c) Suppose a manufacturer has an inventory turnover of 13.5 times per year. Arrow's supply chain performance relative to the manufacturer's, as measured by inventory turnover, isarrow_forwardDescribe why inventory problems are so widespread and what basic insight inventory models provide?arrow_forward
- Can you assist me with Chapter 12 Question 3. Please show the steps it's easier to follow along instead of an excel spreadsheet. Thank youarrow_forwardSumco's annual demand is expected to increase from 1,000 units to 1,500 units, the ordering cost is reduced to $8 per order and the average carrying cost per unit per year is increased to $0.80. Under these new conditions: A) Calculate the new EOQ. B) Calculate the Annual Ordering Cost, the Annual Holding Cost and the Total Annual Cost. C) Plot a graph showing Ordering Cost, Holding Cost and Total Cost as a function of Q for this problem Predictions: On acerarrow_forwardCurrent decision to buy: Ross White's machine shop uses 300 brackets each month during the course of a year. This usage is relatively constant throughout the year. Currently, these brackets are purchased from a supplier 100 miles away for $25 each and the lead time is 2 days. The holding cost per bracket per year is $3.75 (15% of the unit cost) and the annual ordering cost per order is $18.50. There are 240 working days per year. Possible future decision to make in-house: Ross White is reconsidering his decision of buying the brackets and is considering making the brackets in-house. He has determined the set up costs would be $22.50 in machinist time and lost production time. Forty eight brackets could be produced in a day once the machine has been set up. Ross estimates that the cost (including labor and materials) of producing one bracket would be $22.85. The holding cost would be 12% of the cost. What is the EOQ given Ross' current decision to buy the brackets? What is the…arrow_forward
- Just need help with the underlinedarrow_forwardPlease show work so I can understand it. Given this information: •Expected demand during lead time = 800 units • Standard deviation of lead time demand = 40 units Assuming that lead time demand is distributed normally. The risk of stockout is 5 percent during lead time (a) What amount of safety stock is appropriate? (b) Calculate ROParrow_forwardIL Data related to the inventories of Metro Supply are presented below: 困 Surgical Equipment $ 260 170 240 Surgical Supplies $ 120 Rehab Rehab Selling price Cost Equipment S 340 Supplies $ 165 90 250 235 162 Replacement cost Costs to sell Normal gross profit ratio 80 158 30 25 10 30% 30% 30% 20% *Show your computation! If not, no credit A) In applying the lower of cost or market rule, the inventory of surgical equipment would be valued at: B) In applying the lower of cost or market rule, the inventory of surgical supplies would be valued at: C) In applying the lower of cost or market rule, the inventory of rehab equipment would be valued at: D) In applying the lower of cost or market rule, the inventory of rehab supplies would be valued at:arrow_forward
- Give typed answer onlyarrow_forwardRace One Motors is an Indonesian car manufacturer. Atits largest manufacturing facility, in Jakarta, the company producessubcomponents at a rate of 300 per day, and it uses these subcomponentsat a rate of 12,500 per year (of250 working days). Holding costsare $2 per item per year, and orde1ing (setup) costs are $30 per order.a) What is the economic production quantity?b) How many production runs per year will be made?c) What will be the maximum inventory level?d) What percentage of time will the facility be producing components?e) What is the annual cost of ordering and holding inventory?arrow_forwardDiscuss how inventory expenses must be balanced and kept to q minimum through inventory controlarrow_forward
arrow_back_ios
SEE MORE QUESTIONS
arrow_forward_ios
Recommended textbooks for you
- Practical Management ScienceOperations ManagementISBN:9781337406659Author:WINSTON, Wayne L.Publisher:Cengage,Operations ManagementOperations ManagementISBN:9781259667473Author:William J StevensonPublisher:McGraw-Hill EducationOperations and Supply Chain Management (Mcgraw-hi...Operations ManagementISBN:9781259666100Author:F. Robert Jacobs, Richard B ChasePublisher:McGraw-Hill Education
- Purchasing and Supply Chain ManagementOperations ManagementISBN:9781285869681Author:Robert M. Monczka, Robert B. Handfield, Larry C. Giunipero, James L. PattersonPublisher:Cengage LearningProduction and Operations Analysis, Seventh Editi...Operations ManagementISBN:9781478623069Author:Steven Nahmias, Tava Lennon OlsenPublisher:Waveland Press, Inc.
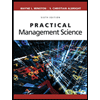
Practical Management Science
Operations Management
ISBN:9781337406659
Author:WINSTON, Wayne L.
Publisher:Cengage,
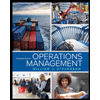
Operations Management
Operations Management
ISBN:9781259667473
Author:William J Stevenson
Publisher:McGraw-Hill Education
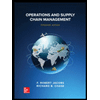
Operations and Supply Chain Management (Mcgraw-hi...
Operations Management
ISBN:9781259666100
Author:F. Robert Jacobs, Richard B Chase
Publisher:McGraw-Hill Education
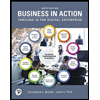
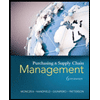
Purchasing and Supply Chain Management
Operations Management
ISBN:9781285869681
Author:Robert M. Monczka, Robert B. Handfield, Larry C. Giunipero, James L. Patterson
Publisher:Cengage Learning
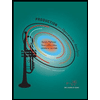
Production and Operations Analysis, Seventh Editi...
Operations Management
ISBN:9781478623069
Author:Steven Nahmias, Tava Lennon Olsen
Publisher:Waveland Press, Inc.