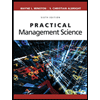
Concept explainers
Dave’s local college football team is playing for the national championship in next month’s bowl game, and he’s thinking about having “We’re number one” T-shirts imprinted in honor of the team. It’s too late to get the shirts before game day, but if he orders today, he can get them within a few days after the game.
The shirts must be ordered in multiples of 1000, and Dave has estimated the amount of profit he will make for possible outcomes of the game.
Given the following payoff table, what will Dave do if he uses the maximin criterion? The maximax criterion? The minimax regret criterion? Order no shirts $0 wins $0 loses $0 ties Order 1000 shirts $800 wins $-200 loses $200 ties Order 2000 shirts $1600 wins $-400 loses $300 ties |

Trending nowThis is a popular solution!
Step by stepSolved in 4 steps with 8 images

- You have an annual demand of 800 units of your product which you sell for $90 a unit. It costs you $20 to place an order and carrying costs for the item are 14%. What is your EOQ?arrow_forwardPlease do not give solution in image format thanku A small mail-order company uses 14,000 boxes a year. Holding cost rate is 18 percent of unit cost per year, and ordering cost is $33 per order. The following quantity discounts are available. Number of Boxes Price per Box 1,000 to 1,999 $1.15 2,000 to 4,999 1.10 5,000 to 9,999 1.05 10,000 or more 1.00 a. Determine the optimal order quantity. Optimal order quantity boxes b. Determine the number of orders per year. (Round the final answer to 1 decimal place.) No. of orders per yeararrow_forwardA manufacturer of hospital supplies has a uniform annual demand for 80,000 boxes of bandages. It costs $20 to store one box of bandages for one year and $320 to set up the plant for production. How many times a year should the company produce boxes of bandages in order to minimize the total storage and setup costs? Question content area bottom Part 1 The company should produce boxes of bandages enter your response here time(s) a year.arrow_forward
- At a recent manufacturing workshop, XYZ, Incorporated explained that demand for disposable masks increase rapidly in March 2020 when quarantine mandates first took effect. At the time, retailers could only place a single order to cover demands through the end of the summer. A certain retailer purchased disposal masks from a supplier at a cost of $20 per unit and sold them for $30 per unit. By the end of summer, demand for masks subsided considerably and all masks that weren't sold during the summer could be sold at a discounted price of $18 per unit. The retailer estimated that demand between March and August would be Normally distributed with mu = 10,000 and sigma = 1525 units With, supply chains becoming more stable since March 2020, the retailer is currently in the process of establishing a contract with a disposable mask supplier. The supplier has agreed to sell masks to the retailer for $18 per unit and will make deliveries any time the supplier places an order for a cost of $100…arrow_forwardDiscuss with examples the two methods of inventory control. Which method do you think is better for a retail store with several items of small value?arrow_forwardPaul’s Toy Distributor (PTD) sells 200 game consoles every week. PTD charges a $300 fixed cost for every delivery. PTD’s annual inventory holding cost is $45 per console. Assume that there are 52 weeks a year. Assume that PTD orders 1000 game consoles at a time. What is the average amount of time the consoles stay as PTD’s inventory before being sold? Find the closest answer.arrow_forward
- A restaurant has an annual demand for 886 bottles of California wine. It costs $2 to store 1 bottle for 1 year, and it costs $10 to place a reorder. Find the optimum number of bottles per order.arrow_forwardThe demand for a particular part called SKU 005 is 1,500 units a year. The cost of one SKU 005 is $64.00. It costs $60.00 to place an order SKU 005, and the user of SKU 005 has a per year inventory carrying cost of 25% of unit cost. Assume that there are 250 working days in the year where SKU 005 is used. What is the combined annual holding and ordering cost of an order size of 200 units for SKU 005? OA. $2050 O B. $1360 O C. $1697 O D. $825 O E. $1200arrow_forwardDelaney Co. uses 12,000 of an item per year. They are open 300 days per year. The item takes 8 days from the time they place an order until they receive it. They like to maintain a safety stock of 200. What is Delaney's reorder point for this item?arrow_forward
- Need help! A-1 is incorrect.arrow_forwardWhat special procedures should be used to control the most expensive and most frequently used products in inventory? Give one example of a product in your response.arrow_forwardA gift shop sells 400 boxes of scented candles a year. The ordering cost is $50 for scented candles, and holding cost is $25 per box per year. What is the economic order size for scented candles?arrow_forward
- Practical Management ScienceOperations ManagementISBN:9781337406659Author:WINSTON, Wayne L.Publisher:Cengage,Operations ManagementOperations ManagementISBN:9781259667473Author:William J StevensonPublisher:McGraw-Hill EducationOperations and Supply Chain Management (Mcgraw-hi...Operations ManagementISBN:9781259666100Author:F. Robert Jacobs, Richard B ChasePublisher:McGraw-Hill Education
- Purchasing and Supply Chain ManagementOperations ManagementISBN:9781285869681Author:Robert M. Monczka, Robert B. Handfield, Larry C. Giunipero, James L. PattersonPublisher:Cengage LearningProduction and Operations Analysis, Seventh Editi...Operations ManagementISBN:9781478623069Author:Steven Nahmias, Tava Lennon OlsenPublisher:Waveland Press, Inc.
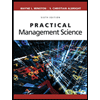
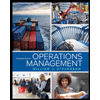
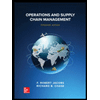
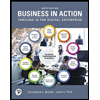
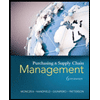
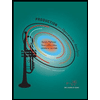