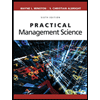
Concept explainers
A wholesale store buys 500 of their most popular coffee mugs each month. The cost of ordering
and receiving shipments is $12 per order. Accounting estimates annual carrying costs are $3.60.
The supplier lead time is 2 operating days. The store operates 240 days per year. Each order is
received from the supplier in a single delivery. There are no quantity discounts.
Use 2 decimal places in your calculations (if needed) and then round your final answer to the
closest whole number.
a. What quantity should the store order with each order?
(show your work in the space below)
b. How many times per year will the store order?
(show your work in the space below)
c. How many days will elapse between two consecutive orders?
(show your work in the space below)
d. What is the reorder point if the company wishes to carry a safety stock of 10 mugs?
(show your work in the space below)
e. What is the store’s total annual cost of placing orders & carrying inventory?
(show your work in the space below)

Trending nowThis is a popular solution!
Step by stepSolved in 3 steps with 5 images

- An electronic store sells 1100 model X computers annually. Annual carrying cost is 12% of the unit cost. Order cost is $80. The lead time for receiving computers is 5 days. The supplier offers discounted prices for the store based on order quantity as given below: Order quantity (Q) Unit Price ($) Q < 50 440 50 <=Q <75 420 75 <= Q < 99 400 Q >= 100 390 Give your answers to two decimal places. Find the minimum cost order quantity at price level $400 Find the optimal order quantity Find the annual ordering cost for optimal order quantity Find the annual holding cost for optimal order quantityarrow_forward3) The Omnigroup stocks and sells Kipor generators. The firm gathered the following information from its Kathmandu office: Demand = D = 19,500 units per year Ordering cost = S = $25.60 per order Holding cost = H = $4.40 per unit per year The firm wants to calculate the: a) EOQ for the Kipor generators. b) Annual holding costs for the Kipor generators. c) Annual ordering costs for the Kipor generators. Hint: EOQ = square root of (2DS/H) Annual Holding Cost = (Q/2) H Annual Ordering Cost = (D/Q) Sarrow_forwardA car manufacturer has holding costs of 37%. One of the items needed in the factory is door handles. For every order, the facotry incurs a fixed cost of $59.00. The manufacturer needs annually 1,900 of the door handles. The door handles supplier offers a price of $11.00 each for quantities of 350 or fewer and a price of $10.23 for quantities over 350 units. Round your answer to the nearest integer value. How many units should the manufacturer order at one time? units What is the total annual cost at this order point?arrow_forward
- DFC Company has recorded the past years sales for the company: Year(t) Sales(x) (in Million Pesos) 2011(1) 2012(2) 2013(3) 2014(4) 2015(5) 2016(6) 2017(7) 2018(8) 2019(9) 2020(10) 219 224 268 272 253 284 254 278 282 298 Use the naïve model. Compute for MAE and MSE Use a three period moving average. Compute for the MAE and MSE Use the simple exponential smoothing to make a forecasting table. Compute the MAE and MSE of the forecasts. Alpha = 0.1 Use the least square method to make the forecasting table. Compute the MAE and MSE *** Use excel or r programmingarrow_forwardSuppose that the R&B Beverage Company has a soft drink product that shows a constant annual demand rate of 3,800 cases. A case of the soft drink costs R&B $3. Ordering costs are $20 per order and holding costs are 25% of the value of the inventory. R&B has 250 working days per year, and the lead time is 5 days. Identify the following aspects of the inventory policy. a. economic order quantity (round your answer to the nearest integer.) _____450_______ b. reorder point ______76______ c. cycle time (in days) (round your answer to two decimal places.) ______29.61______ d. total annual cost (in $) (round your answer to two decimal places.) _____?_______ ***I am asking the question with the ? symbol. I have been able to locate the numbers for the first three but I am having issues computing my answers for the last one.arrow_forwardA billiard ball maker must place orders for resin, a raw material for billiard balls. It uses resin at a rate of 120 kilograms each day, and incurs a cost of $0.4 per kilogram per day to hold inventory. The ordering cost is $150 per order. Lead time for delivery is 4 days. Assume 365 day in a year.What is the optimal length of the order cycle associated with the minimum total cost of ordering and inventory holding? [Round your final number with two decimals] 0.13 days 1.10 days 2.50 days 47.76 days None of the above PLEASE SHOW CALCULATIONS NOT JUST ANSWERarrow_forward
- please answer in details within 30 minutes.arrow_forwarda) What is the economic order quantity? b) Find the annual holding costs.c) Find the annual ordering costs.d) What is the reorder point?arrow_forwardSuppose that the R&B Beverage Company has a soft drink product that shows a constant annual demand rate of 3,400 cases. A case of the soft drink costs R&B $3. Ordering costs are $20 per order and holding costs are 25% of the value of the inventory. R&B has 250 working days per year, and the lead time is 5 days. Identify the following aspects of the inventory policy. (a) economic order quantity (round your answer to the nearest integer.) (b) reorder point (c) cycle time (in days) (round your answer to two decimal places.) days (d) total annual cost (in $) (round your answer to two decimal places.) $arrow_forward
- Do you think the safety stock (safety inventory) could be negative? What is the meaning of a negative safety inventory (hint: safety stock is the difference between the optimal inventory and the average demand)?arrow_forwardGive typed full explanationarrow_forwardAll Seasons Flower Shop uses 870 clay pots a month. The pots are purchased at $ 6 each. Annual holding cost per pot is estimated to be 35% of purchase cost. Ordering cost is $ 40 per order. The shop operates 12 months in a year. What would be the difference in total cost if an order quantity of 1000 is used instead of the EOQ. Note: calculate the difference as “total cost with Q = 1000 – total cost with EOQ”.arrow_forward
- Practical Management ScienceOperations ManagementISBN:9781337406659Author:WINSTON, Wayne L.Publisher:Cengage,Operations ManagementOperations ManagementISBN:9781259667473Author:William J StevensonPublisher:McGraw-Hill EducationOperations and Supply Chain Management (Mcgraw-hi...Operations ManagementISBN:9781259666100Author:F. Robert Jacobs, Richard B ChasePublisher:McGraw-Hill Education
- Purchasing and Supply Chain ManagementOperations ManagementISBN:9781285869681Author:Robert M. Monczka, Robert B. Handfield, Larry C. Giunipero, James L. PattersonPublisher:Cengage LearningProduction and Operations Analysis, Seventh Editi...Operations ManagementISBN:9781478623069Author:Steven Nahmias, Tava Lennon OlsenPublisher:Waveland Press, Inc.
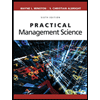
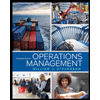
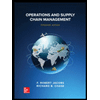
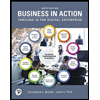
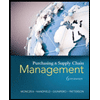
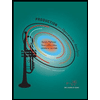