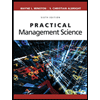
Concept explainers
A real estate agent is considering changing her land line phone plan. There are three plans to choose from, all of which involve a monthly service charge of $20. Plan A has a cost of $.43 a minute for daytime calls and $.18 a minute for evening calls. Plan B has a charge of $.53 a minute for daytime calls and $.15 a minute for evening calls. Plan C has a flat rate of $80 with 250 minutes of calls allowed per month and a charge of $.40 per minute beyond that, day or evening.
a. Determine the total charge under each plan for this case: 140 minutes of day calls and 60 minutes of evening calls in a month. (Do not round intermediate calculations. Round your answer to 2 decimal places.)
b. If the agent will only use the service for daytime calls, over what range of call minutes will each plan be optimal? (Round each answer to the nearest whole number. Include the indifference point itself in each answer.)
c. Suppose that the agent expects both daytime and evening calls. At what point (i.e., percentage of total call minutes used for daytime calls) would she be indifferent between plans A and B? (Do not round intermediate calculations. Enter your answer as a percentage rounded to 2 decimal places. Omit the "%" sign in your response.)

Trending nowThis is a popular solution!
Step by stepSolved in 3 steps

- The cost infomation of an old process unit that has a capacity of 5,400 ft'/hr and a total cost of $8,500,000 is used to find the cost of a new unit that has a capacity of 8,500 t'hr. Assuming the total cost of the new unit is $12,000,000 you are required to state: 1. The method and equation that you will use to find that cost, 2. The value of the corresponding factor, 3. Is the value calculated in (2) within the accepted range?arrow_forwardCompute the capacity (i.e. processing rate) for each of the following scenarios. Convertyour answers to parts per hour.a. A four-station line with single-machine stations, where the average processing timesare 15, 20, 10 and 12 minutes, respectively.b. A three-station line where the number of machines at stations 1, 2 and 3 is 2, 6, and3, respectively; and the average processing times are 10, 24 and 18 minutes,respectively.arrow_forwardA manager must decide between two machines. The manager will take into account each machine's operating costs and initial costs, and its breakdown and repair times. Machine A has a projected average operating time of 140 hours and a projected average repair time of 7 hours. Projected times for machine B are an average operating time of 70 hours and a repair time of 6 hours. What are the projected availabilities of each machine? (Round your answer to 3 decimal places). I don't want the answer. I just want to know HOW to do it.arrow_forward
- The Dahlia Medical Center has 34 labor rooms, 18 combination labor and delivery rooms, and 5 delivery rooms. All of these facilities operate around the clock. Time spent in labor rooms varies from hours to days, with an average of about a day. The average uncomplicated delivery requires about one hour in the delivery room. The average time in a combination labor-delivery room is about 24 hours. During an exceptionally busy three-day period, 101 healthy babies were born at Dahlia Medical Center. 59 babies were born in separate labor and delivery rooms and 42 were born in combined labor and delivery rooms. Which of the facilities (labor rooms, combination labor and delivery rooms, or delivery rooms) had the greatest utilization rate? ▼had the highest utilization rate of %. (Enter your response as a percent rounded to two decimal places.) The combination labor and delivery rooms delivery rooms labor roomsarrow_forwardA retail catalog operation employs a bank of six telephone operators who process orders using computer terminals. When a terminal breaks down, it must be disconnected and taken to a nearby electronic repair shop, where it is repaired. The mean time between terminal breakdowns is six working days, and the mean time required to repair a terminal is two working days (both exponentially distributed). As a result of lost sales, it costs the mail-order operation an estimated $50 per day in lost profits each day a terminal is out for repair. The company pays the electronics repair shop $3000 per year on a service agreement to repair the terminals. The company is considering the possibility of signing a new service agreement with another electronics repair shop that will provide subsitutute terminals while the broken ones are at the repair shop. However, the new service agreement would cost the mail-order operation $15,000 per year. Assuming that there are 250 working days in a year, determine…arrow_forwardPine Valley Furniture Pine Valley Furniture recently implemented a new internship program and has begun recruiting interns from nearby university campuses. As part of this program, interns have the opportunity to work alongside a systems analyst. This shadowing opportunity provides invaluable insights into the systems analysis and design process. Recently you were selected for a six-month internship at Pine Valley Furniture, and Jim Woo has been assigned as your supervisor. At an initial meeting with Jim Woo, he explains that Pine Valley Furniture is currently involved with two important systems development projects, the customer tracking system and WebStore. The purpose of the customer tracking system is to enable the PVF marketing group to track customer purchase activity and sales trends better. The WebStore project will help move the company into the twenty-first century by facilitating online furniture purchases, with an initial focus on corporate furniture buying. During your…arrow_forward
- A fast-food restaurant has a drive-thru window and during peak lunch times can handle a maximum of 60 cars per hour with one person taking orders, assembling them, and acting as cashier. The average sale per order is $9.50. A proposal has been made to add two workers and divide the tasks among the three. One will take orders, the second will assemble them, and the third will act as a cashier. With this system, it is estimated that 85 cars per hour can be serviced.arrow_forwardFee-for-service payments give each service a point value. True or False?arrow_forwardA manager must decide which type of machine to buy, A, B, or C. Machine costs (per individual machine) are as follows: Machine Cost $50,000 A B $40,000 C $70,000 Product forecasts and processing times on the machines are as follows: PROCCESSING TIME PER UNIT (minutes) Annual Product Demand 1 2 3 4 18,000 25,000 15,000 9,000 A 1 5 4 5 A B C B Click here for the Excel Data File 6531 Total processing time in minutes per machine: a. Assume that only purchasing costs are being considered. Compute the total processing time required for each machine type to meet demand, how many of each machine type would be needed, and the resulting total purchasing cost for each machine type. The machines will operate 8 hours a day, 220 days a year. (Enter total processing times as whole numbers. Round up machine quantities to the next higher whole number. Compute total purchasing costs using these rounded machine quantities. Enter the resulting total purchasing cost as a whole number.) C 2 1 2 6arrow_forward
- The capacity of a restaurant would be the Multiple Choice minimum operating cost of the restaurant during a workweek. average number of customers that visit the restaurant on weekends. maximum number of customers who can be effectively served at any one particular time. total number of customers who have visited the restaurant since its establishment. average number of employees who work in the restaurant on a normal day.arrow_forwardA manager must decide which type of machine to buy, A, B, or C. Machine costs (per individual machine) are as follows: Machine Cost A $ 60,000 B $ 50,000 C $ 60,000 Product forecasts and processing times on the machines are as follows: PROCCESSING TIME PER UNIT (minutes) Product AnnualDemand A B C 1 16,000 3 4 4 2 10,000 6 5 1 3 15,000 1 3 6 4 17,000 5 3 4 Click here for the Excel Data File a. Assume that only purchasing costs are being considered. Compute the total processing time required for each machine type to meet demand, how many of each machine type would be needed, and the resulting total purchasing cost for each machine type. The machines will operate 10 hours a day, 240 days a year. (Enter total processing times as whole numbers. Round up machine quantities to the next higher whole number. Compute total purchasing costs using these rounded machine quantities. Enter the resulting total purchasing cost as a whole…arrow_forward
- Practical Management ScienceOperations ManagementISBN:9781337406659Author:WINSTON, Wayne L.Publisher:Cengage,Operations ManagementOperations ManagementISBN:9781259667473Author:William J StevensonPublisher:McGraw-Hill EducationOperations and Supply Chain Management (Mcgraw-hi...Operations ManagementISBN:9781259666100Author:F. Robert Jacobs, Richard B ChasePublisher:McGraw-Hill Education
- Purchasing and Supply Chain ManagementOperations ManagementISBN:9781285869681Author:Robert M. Monczka, Robert B. Handfield, Larry C. Giunipero, James L. PattersonPublisher:Cengage LearningProduction and Operations Analysis, Seventh Editi...Operations ManagementISBN:9781478623069Author:Steven Nahmias, Tava Lennon OlsenPublisher:Waveland Press, Inc.
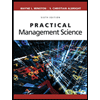
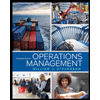
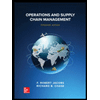
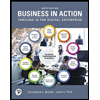
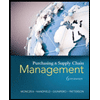
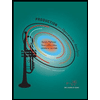