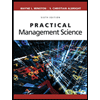
Concept explainers
asap!!
A manager of an inventory system believes that inventory models are important decision making aids. Even though often using an EOQ policy, the manager never considered a backorder model because of the assumption that backorders were “bad” and should be avoided. However, with upper management’s continued pressure for cost reduction, you have been asked to analyze the economics of a backorder policy for some products that can possibly be backordered. For a specific product with D = 1200 units per year, Co = 160, = 4, and = 25, what is the difference in total annual cost between the EOQ model and the planned shortage or backorder model? If the manager adds constraints that no more than 25% of the units can be backordered and that no customer will have to wait more than 18 days for an order, should the backorder inventory policy be adopted? Assume 300 working days per year.

Trending nowThis is a popular solution!
Step by stepSolved in 2 steps with 4 images

- MAY I ASK FOR THE SOLUTIONS AND ANSWERS OF NOS. 12 to 17 (kindly refer to the table) Thank you! ABC Corporation resells one type of candle. It has 250 working days. Each day, it sells an average of 500 boxes but may sometimes sell a maximum of 600 boxes. The supplier takes an average of 5 days to deliver the order. During busier times, the supplier may take 7 days. Based on ABC’s records, ordering cost average P400 per order. Storage cost per box average P5 per year. There is also an opportunity cost of 1% per year for every peso invested in inventories. Each box of candles costs P450. If ABC would continue its current inventory management policy, it would keep 10,000 boxes as safety stock and order tendays-worth of inventory. (A) Reorder Point 1. What should be the reorder point in boxes? 2. How much would the normal lead time usage be? 3. How much should ABC keep as safety stock? (B) Economic Order Quantity 4. What is the annual demand for the boxes of candles? 5. How much is the…arrow_forwardDiscuss what condition must exist for good inventory management?arrow_forwardWhat are the different types of inventory carrying costs? Are these expenses constant or variable, as described here?arrow_forward
- What are the challenges of inventory management in any company? And how a company can overcome it.arrow_forwardWhat is a disadvantage common to the following two strategies: (1) varying inventory levels and (2) backordering during periods of high demand?arrow_forwardConduct the ABC analysis for a convenience store, using the following percentages A inventory - most important items, generating 60% of sales B inventory - items generating the next 30% of sales Cinventory - items generating <10% of sales Stock (units) |Unit price Revenue 1000 $ 1.89 Product АВС Candy bars Cereal 200 $ 4.50 Cookies 400 $ 4.00 Milk 100 $ 2.00 200 $ 3.00 500 $ 1.50 Muffins Soda Hints 1. sort by revenue (largest to smallest) 2. calculate % of total revenue for each item 3. run a cumulative % for the items 4. identify the cut-off for each category You can run the entire exercise sorting and extending the table abovearrow_forward
- PART A Speedy Bicycle Company (SBC) is a wholesale distributor of a wide variety of bicycles and bicycle parts. The most popular model is the Dragonfly, which sells for $170. All manufacturing is done at a plant in China, and shipment takes a month (30 days) from the time an order is placed. The estimated order cost is $75, including customs clearance. SBC's cost per bicycle is 65% of retail price, and inventory carrying cost is 11% per year of SBC's cost. If the company cannot fulfill a retail order, the retailer will get the shipment from another distributor and SBC loses that business. SBC is planning inventory for 2023 based on forecasted demand and wants to maintain a 93% service level to minimize lost orders. The company has 300 working days per year. 2021 Forecasted Demand for the Dragonfly Bicycle Model: F A J 15 58 J 8 M 31 M 96 J 59 38 A 23 S 16 0 14 N 26 D 41arrow_forwardAnnual demand for your product is 50,000 units. Holding cost is 25% of the value of the item. The cost, per unit, is $5.00. It costs $200 to place an order. This is a new supplier that you are thinking about buying from, and the catch is that you have to place a pretty big order in order to be able to buy from these people. You have to buy at least 6,957 units every time. What are you total costs, (including the Cost of Goods), if you choose to buy from this supplier?arrow_forwardHow does inventory affect a firm’s financial performance? Explain the importance of inventory, types of inventories, and key decisions and costs.arrow_forward
- PHL Manufacturing assembles security monitors. It purchases 900 black-and-white cathode ray tubes per month at $80 each. Ordering costs are $30, and annual carrying costs are 25 percent of the purchase price. - a) Determine the optimal quantity (4 points) - b) Find the total annual cost of ordering and carrying the inventory (2 points) - c) If the supplier offer a price of $79 per tube for ordering 1200 tubes in a lot, would you evaluate and advise PHL to take advantage of the offer?arrow_forwardBe specific in your suggestions for reducing inventory and how to implement them.arrow_forwardcan you please help me answer this question.... Rebar Company prepared the following analysis of its year-end inventory on December 31. First, determine the total lower of cost or market value for each product in Rebar Company's inventory. Second, prepare the journal entry needed at year-end to value the inventory at LCM, if applicable. Historical Cost Replacement Cost Product Quantity per unit per unit A 17 $430 $499 B 140 325 299 C 38 75 69arrow_forward
- Practical Management ScienceOperations ManagementISBN:9781337406659Author:WINSTON, Wayne L.Publisher:Cengage,Operations ManagementOperations ManagementISBN:9781259667473Author:William J StevensonPublisher:McGraw-Hill EducationOperations and Supply Chain Management (Mcgraw-hi...Operations ManagementISBN:9781259666100Author:F. Robert Jacobs, Richard B ChasePublisher:McGraw-Hill Education
- Purchasing and Supply Chain ManagementOperations ManagementISBN:9781285869681Author:Robert M. Monczka, Robert B. Handfield, Larry C. Giunipero, James L. PattersonPublisher:Cengage LearningProduction and Operations Analysis, Seventh Editi...Operations ManagementISBN:9781478623069Author:Steven Nahmias, Tava Lennon OlsenPublisher:Waveland Press, Inc.
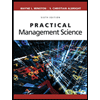
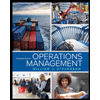
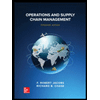
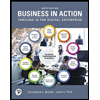
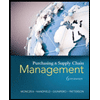
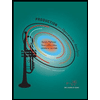