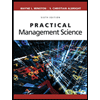
Practical Management Science
6th Edition
ISBN: 9781337406659
Author: WINSTON, Wayne L.
Publisher: Cengage,
expand_more
expand_more
format_list_bulleted
Concept explainers
Question
A farm consists of 600 acres of land, of which 500 acres will be planted with corn, soybeans, and wheat, according to these conditions:
- At least half of the planted acreage should be in corn
- No more than 200 acres should be soybeans
- The ratio of corn to wheat planted should be 2:1
It costs $20 an acre to plant corn, $15 an acre to plant soybeans, and $12 an acre to plant wheat
Formulate this problem as an LP model that will minimize planting cost while achieving the specified conditions.
Expert Solution

This question has been solved!
Explore an expertly crafted, step-by-step solution for a thorough understanding of key concepts.
This is a popular solution
Trending nowThis is a popular solution!
Step by stepSolved in 3 steps with 4 images

Knowledge Booster
Learn more about
Need a deep-dive on the concept behind this application? Look no further. Learn more about this topic, operations-management and related others by exploring similar questions and additional content below.Similar questions
- Assume the demand for a companys drug Wozac during the current year is 50,000, and assume demand will grow at 5% a year. If the company builds a plant that can produce x units of Wozac per year, it will cost 16x. Each unit of Wozac is sold for 3. Each unit of Wozac produced incurs a variable production cost of 0.20. It costs 0.40 per year to operate a unit of capacity. Determine how large a Wozac plant the company should build to maximize its expected profit over the next 10 years.arrow_forwardThe Tinkan Company produces one-pound cans for the Canadian salmon industry. Each year the salmon spawn during a 24-hour period and must be canned immediately. Tinkan has the following agreement with the salmon industry. The company can deliver as many cans as it chooses. Then the salmon are caught. For each can by which Tinkan falls short of the salmon industrys needs, the company pays the industry a 2 penalty. Cans cost Tinkan 1 to produce and are sold by Tinkan for 2 per can. If any cans are left over, they are returned to Tinkan and the company reimburses the industry 2 for each extra can. These extra cans are put in storage for next year. Each year a can is held in storage, a carrying cost equal to 20% of the cans production cost is incurred. It is well known that the number of salmon harvested during a year is strongly related to the number of salmon harvested the previous year. In fact, using past data, Tinkan estimates that the harvest size in year t, Ht (measured in the number of cans required), is related to the harvest size in the previous year, Ht1, by the equation Ht = Ht1et where et is normally distributed with mean 1.02 and standard deviation 0.10. Tinkan plans to use the following production strategy. For some value of x, it produces enough cans at the beginning of year t to bring its inventory up to x+Ht, where Ht is the predicted harvest size in year t. Then it delivers these cans to the salmon industry. For example, if it uses x = 100,000, the predicted harvest size is 500,000 cans, and 80,000 cans are already in inventory, then Tinkan produces and delivers 520,000 cans. Given that the harvest size for the previous year was 550,000 cans, use simulation to help Tinkan develop a production strategy that maximizes its expected profit over the next 20 years. Assume that the company begins year 1 with an initial inventory of 300,000 cans.arrow_forwardAt the beginning of each week, a machine is in one of four conditions: 1 = excellent; 2 = good; 3 = average; 4 = bad. The weekly revenue earned by a machine in state 1, 2, 3, or 4 is 100, 90, 50, or 10, respectively. After observing the condition of the machine at the beginning of the week, the company has the option, for a cost of 200, of instantaneously replacing the machine with an excellent machine. The quality of the machine deteriorates over time, as shown in the file P10 41.xlsx. Four maintenance policies are under consideration: Policy 1: Never replace a machine. Policy 2: Immediately replace a bad machine. Policy 3: Immediately replace a bad or average machine. Policy 4: Immediately replace a bad, average, or good machine. Simulate each of these policies for 50 weeks (using at least 250 iterations each) to determine the policy that maximizes expected weekly profit. Assume that the machine at the beginning of week 1 is excellent.arrow_forward
- Scenario 3 Ben Gibson, the purchasing manager at Coastal Products, was reviewing purchasing expenditures for packaging materials with Jeff Joyner. Ben was particularly disturbed about the amount spent on corrugated boxes purchased from Southeastern Corrugated. Ben said, I dont like the salesman from that company. He comes around here acting like he owns the place. He loves to tell us about his fancy car, house, and vacations. It seems to me he must be making too much money off of us! Jeff responded that he heard Southeastern Corrugated was going to ask for a price increase to cover the rising costs of raw material paper stock. Jeff further stated that Southeastern would probably ask for more than what was justified simply from rising paper stock costs. After the meeting, Ben decided he had heard enough. After all, he prided himself on being a results-oriented manager. There was no way he was going to allow that salesman to keep taking advantage of Coastal Products. Ben called Jeff and told him it was time to rebid the corrugated contract before Southeastern came in with a price increase request. Who did Jeff know that might be interested in the business? Jeff replied he had several companies in mind to include in the bidding process. These companies would surely come in at a lower price, partly because they used lower-grade boxes that would probably work well enough in Coastal Products process. Jeff also explained that these suppliers were not serious contenders for the business. Their purpose was to create competition with the bids. Ben told Jeff to make sure that Southeastern was well aware that these new suppliers were bidding on the contract. He also said to make sure the suppliers knew that price was going to be the determining factor in this quote, because he considered corrugated boxes to be a standard industry item. Is Ben Gibson acting legally? Is he acting ethically? Why or why not?arrow_forwardScenario 3 Ben Gibson, the purchasing manager at Coastal Products, was reviewing purchasing expenditures for packaging materials with Jeff Joyner. Ben was particularly disturbed about the amount spent on corrugated boxes purchased from Southeastern Corrugated. Ben said, I dont like the salesman from that company. He comes around here acting like he owns the place. He loves to tell us about his fancy car, house, and vacations. It seems to me he must be making too much money off of us! Jeff responded that he heard Southeastern Corrugated was going to ask for a price increase to cover the rising costs of raw material paper stock. Jeff further stated that Southeastern would probably ask for more than what was justified simply from rising paper stock costs. After the meeting, Ben decided he had heard enough. After all, he prided himself on being a results-oriented manager. There was no way he was going to allow that salesman to keep taking advantage of Coastal Products. Ben called Jeff and told him it was time to rebid the corrugated contract before Southeastern came in with a price increase request. Who did Jeff know that might be interested in the business? Jeff replied he had several companies in mind to include in the bidding process. These companies would surely come in at a lower price, partly because they used lower-grade boxes that would probably work well enough in Coastal Products process. Jeff also explained that these suppliers were not serious contenders for the business. Their purpose was to create competition with the bids. Ben told Jeff to make sure that Southeastern was well aware that these new suppliers were bidding on the contract. He also said to make sure the suppliers knew that price was going to be the determining factor in this quote, because he considered corrugated boxes to be a standard industry item. As the Marketing Manager for Southeastern Corrugated, what would you do upon receiving the request for quotation from Coastal Products?arrow_forward2.28 A foundry produces castings to order. An order for 20 special castings has been re- ceived. Since the casting process is highly variable, not all castings produced are good. The cost of producing each casting is $550; the additional cost of finishing a good casting is $125. If a casting is not good, it is recycled at a value of $75; excess good castings are not finished but are recycled at a value of $75. The customer has agreed to accept 15, 16, 17, 18, 19, or 20 castings at a price of $1250 each. If fewer than 15 good castings are produced, none will be purchased by the customer. Prob- ability distributions for the number of good castings produced in a batch of varying sizes are given below. How many castings should be scheduled in order to maximize expected profit? #Good Castings 5 6 7 8 9 10 11 12 13 14 15 16 17 18 19 20 21 22 23 24 25 26 27 28 29 30 79 2 PRODUCT, PROCESS, AND SCHEDULE DESIGN Number of Castings Scheduled 15 16 17 0.05 0.00 0.00 0.00 0.00 0.00 0.05 0.05 0.00…arrow_forward
- Given the following for a retail property: This property is occupied by a single tenant: Net Rentable Space 10,000 sq. ft. Lease Rate $18.00 per sq. ft. per year Real Estate Taxes $ 1.75 per sq. ft. per year Operating Expenses $ 0.55 per sq. ft. per year Insurance $ 0.06 per sq. Ii. per year Actual Gross Sales $2,200,000 Base Sales as per Lease $2,000,000 Percentage Lease Clause 4.0% What is the amount of rent due on a per sq. ft. basis (per year) ifthe tenant has a "net net"_ (NN)Jease and a "percentage lease clause" in the lease? Please provide proper keystrokes for the BAii Plus and Gualifier Plus IIIfx calculators. Thank you!arrow_forwardThe local supermarket buys lettuce each day to ensure very fresh produce. Each morning, any lettuce that is left from the previous day is sold to a dealer that resells it to farmers who use it to feed their animals. This week, the supermarket can buy fresh lettuce for $4 a box. The lettuce is sold for $10 a box and the dealer that sells old lettuce is willing to pay $1.50 a box. Past history says that tomorrow’s demand for lettuce averages 250 boxes, with a standard deviation of 34 boxes. How many boxes of lettuce should the supermarket purchase tomorrow?arrow_forwardWhat would be the purpose for a cashier’s well (pit or bucket) in a hotel that has no property management system? Why would a hotel that has a property management system in place also have a cashier’s well (pit or bucketarrow_forward
- Please no plagiarism pleasearrow_forwardThere is an upstream Picking department that feeds two downstream Packing departments: Pack Singles and Pack Multis. Those Packing departments feed to a Shipping department that loads the outgoing trucks. 40% of your Pick volume goes to Pack Singles and has a packing rate of 104 units per labor hour (uph). 60% of the Pick volume goes to Pack Multis and has a pack rate of 215 units per labor hour. Your pickers pick both Single and Multi items throughout the day at an overall average rate of 114 units per labor hour. All units that are packed in both processes go through the Ship process at a rate of 570 units per hour. You have 102 people today for all 4 departments and you absolutely must pack 47,880 units in Pack Multis Items to meet a customer promise metric. How do you allocate labor to balance the flow in your department if you work a 10 hour shift? Do not assume breaks or lunches in your answer. Redirect 1: You now need to process all of the Pack Singles Volume in the first 5…arrow_forward49 The local supermarket buys lettuce each day to ensure really fresh produce. Each morning, any lettuce that is left from the previous day is sold to a dealer that resells it to farmers who use it to feed their animals. This week, the supermarket can buy fresh lettuce for $7.00 a box. The lettuce is sold for $18.00 a box and the dealer that sells old lettuce is willing to pay $2.00 a box. Past history says that tomorrow's demand for lettuce averages 255 boxes with a standard deviation of 40 boxes.arrow_forward
arrow_back_ios
SEE MORE QUESTIONS
arrow_forward_ios
Recommended textbooks for you
- Practical Management ScienceOperations ManagementISBN:9781337406659Author:WINSTON, Wayne L.Publisher:Cengage,Purchasing and Supply Chain ManagementOperations ManagementISBN:9781285869681Author:Robert M. Monczka, Robert B. Handfield, Larry C. Giunipero, James L. PattersonPublisher:Cengage Learning
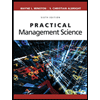
Practical Management Science
Operations Management
ISBN:9781337406659
Author:WINSTON, Wayne L.
Publisher:Cengage,
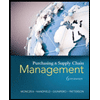
Purchasing and Supply Chain Management
Operations Management
ISBN:9781285869681
Author:Robert M. Monczka, Robert B. Handfield, Larry C. Giunipero, James L. Patterson
Publisher:Cengage Learning