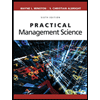
Practical Management Science
6th Edition
ISBN: 9781337406659
Author: WINSTON, Wayne L.
Publisher: Cengage,
expand_more
expand_more
format_list_bulleted
Question
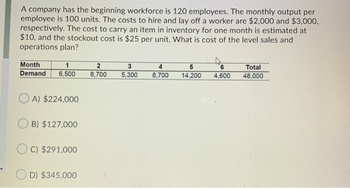
Transcribed Image Text:A company has the beginning workforce is 120 employees. The monthly output per
employee is 100 units. The costs to hire and lay off a worker are $2,000 and $3,000,
respectively. The cost to carry an item in inventory for one month is estimated at
$10, and the stockout cost is $25 per unit. What is cost of the level sales and
operations plan?
Month
1
Demand 6,500
A) $224,000
B) $127,000
C) $291,000
D) $345,000
2
3
8,700 5,300
4
5
8,700 14,200
6
4,600
Total
48,000
Expert Solution

This question has been solved!
Explore an expertly crafted, step-by-step solution for a thorough understanding of key concepts.
This is a popular solution
Trending nowThis is a popular solution!
Step by stepSolved in 3 steps with 2 images

Knowledge Booster
Similar questions
- The extra inventory we keep just in case the replenishment is delayed is referred to as Group of answer choices a)customer service inventory b)unanticipated excess inventory c)safety stock d) unexplained inventoryarrow_forwardThe table above provides the aggregate plan of production by a firm. It is known that the firm uses a level plan with lost sales, i.e., without backorders. Given this information, what is the number in the cell that says xx?arrow_forwardQueen Manufacturing uses 2,200 switch assemblies per week and then reorders another 2,200. Assume the relevant carrying cost per switch assembly is $5.90 and the fixed order cost is $620. a. Calculate the carrying costs. Note: Do not round intermediate calculations and round your answer to the nearest whole number, e.g., 32. b. Calculate the restocking costs. Note: Do not round intermediate calculations and round your answer to the nearest whole number, e.g., 32. c. Calculate the economic order quantity. Note: Do not round intermediate calculations and round your answer to 2 decimal places, e.g., 32.16. d. Calculate the EOQ number of orders per year. Note: Do not round intermediate calculations and round your answer to 2 decimal places, e.g., 32.16. a. Carrying costs b. Restocking costs c. Economic order quantity d. Number of ordersarrow_forward
- The Average days of inventory is?arrow_forwardDevelop a production plan and calculate the annual cost for a firm whose demand forecast is fall, 11,000; winter, 8,000; spring, 6,000; summer, 13,000. Inventory at the beginning of fall is 500 units. At the beginning of fall you currently have 30 workers, but you plan to hire temporary workers at the beginning of summer and lay them off at the end of summer. In addition, you have negotiated with the union an option to use the regular workforce on overtime during winter or spring if overtime is necessary to prevent stockouts at the end of those quarters. Overtime is not available during the fall. Relevant costs are hiring, $100 for each temp; layoff $200 for each worker laid off; inventory holding, $5 per unit-quarter; backorder, $10 per unit; straight time, $5 per hour; overtime, $8 per hour. Assume that the productivity is 0.5 unit per worker hour, with eight hours per day and 60 days per season. a. What is the total cost for this plan?arrow_forwardQuestion 12 Simulate the following inventory replenishment problem for 20 weeks. You will have to use the Excel program to simulate. Demand is uniformly distributed between 20 and 30 units. Additional Data are given below. Inventory Cost/Week = $ 1.00 Shortage Cost/Week = $ 2.00 Lead Time = 2 weeks %3D Beginning Stock on Hand (SOH) = 0 %3D Supply in Week 1 = 21 units %3! Supply in Week 2= 22 units What is the total shortage cost at the end of 20 weeks if the order size in every week is 20 units? tion The demand for the next 20 weeks is given below ation Week 1 2 Demand 21 22 4 10 30 21 27 28 23 29 21 25 Week 11 12 13 14 15 17 16 18 19 20 COarrow_forward
- The definition of work-in-process (WIP) inventory is: Select one: a. An end item ready to be sold, but still an asset on the company's books. b. Products or components that are no longer raw materials but have not yet become finished products. c. Materials for maintenance, repair and operation. d. Materials that are normally purchased but have not yet entered the manufacturing process. and. Additional stock to allow for uneven demand; a buffer.arrow_forwarda) The average monthly demand requirement = ____units (round to nearest whole number.) B) The total stockout cost = $____(nearest whole number) C) The total inventory carrying cost = $____(nearest whole number) D) The total cost, excluding normal time labor costs, is = $_____(nearest whole number)arrow_forwardThe quantity consumed or patronage—store visits—during a specific period is called A. trial. B. service inventory. C. usage rate. D. consumption rate. E. turnover.arrow_forward
- Classify the items in a warehouse inventory using the ABC method, where Group A contributes 80%, Group B contributes 15%, and Group C contributes 5% to the total inventory value Product Code Annual Demand Pick List Frequenscy Weighted Volume Weighthed Percentage Comulative Weight Percentage ABC Category A001 20000 2200 A002 19000 1700 A003 7800 700 A004 9840 1400 A005 16000 1300 A006 12000 2000 A007 9950 400 A008 10500 1700 A009 8200 515 A010 4700 258 A011 5100 367 A012 8800 800 A013 8900 711 A014 15000 1900 A015 7900 350 A016 9620 2000 A017 8800 550 A018 25000 2000 A019 9950 380 A020 10500 1100arrow_forwardI understand that as per the calculations, the gross requirement for week 3 is 50 (25*2) (Item A's order releases), week 5 is 190 (20*2) + (150*1) (Item A's order releases + Item B's order releases), and week 6 is 300 (150*2) (Item A's order releases). But I want to know why do we do it that way because If I have a similar question do I always multiply item A's order release for week 3 by 2, week 5 (Item A's order releases x 2 + Item B's order releases x 1), and and week 6 (Item A's order releases x 2 ) I want to understand why we do that so I can anwser a similar question I don't understand why we do that have way just that you did it that wayarrow_forwardA Company is interested in developing a quarterly aggregate production plan but they are not sure if a level strategy with backorders or a chase strategy would be better. They have the following information available regarding their production operation: Hiring workers Layoff workers Inventory holding Cost Stockout cost for backorders Production (Labor) cost Subcontracting cost Previous quarter's production Beginning inventoy Quarter forecasts are 2000, 6000, 4000, 5000, respectively. This problem has questions. Suppose that you want to use a level plan with backorders (one that produces at the average demand over the four quarters). Answer the next two questions using this plan. Do not round your intermediate calculations. Round your final answer to the nearest whole number. What would be your production rate each month? A. 4250 B. 3500 C. 4250, 3000, 4000, 5000 D. 2000, 6000, 4000, 5000 What is the ending inventory in Quarter 2 A. 500 B. 2250 C. 2500 D. 0 Suppose that you want to use…arrow_forward
arrow_back_ios
SEE MORE QUESTIONS
arrow_forward_ios
Recommended textbooks for you
- Practical Management ScienceOperations ManagementISBN:9781337406659Author:WINSTON, Wayne L.Publisher:Cengage,Operations ManagementOperations ManagementISBN:9781259667473Author:William J StevensonPublisher:McGraw-Hill EducationOperations and Supply Chain Management (Mcgraw-hi...Operations ManagementISBN:9781259666100Author:F. Robert Jacobs, Richard B ChasePublisher:McGraw-Hill Education
- Purchasing and Supply Chain ManagementOperations ManagementISBN:9781285869681Author:Robert M. Monczka, Robert B. Handfield, Larry C. Giunipero, James L. PattersonPublisher:Cengage LearningProduction and Operations Analysis, Seventh Editi...Operations ManagementISBN:9781478623069Author:Steven Nahmias, Tava Lennon OlsenPublisher:Waveland Press, Inc.
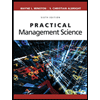
Practical Management Science
Operations Management
ISBN:9781337406659
Author:WINSTON, Wayne L.
Publisher:Cengage,
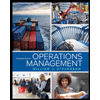
Operations Management
Operations Management
ISBN:9781259667473
Author:William J Stevenson
Publisher:McGraw-Hill Education
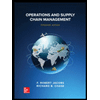
Operations and Supply Chain Management (Mcgraw-hi...
Operations Management
ISBN:9781259666100
Author:F. Robert Jacobs, Richard B Chase
Publisher:McGraw-Hill Education
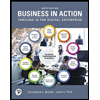
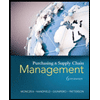
Purchasing and Supply Chain Management
Operations Management
ISBN:9781285869681
Author:Robert M. Monczka, Robert B. Handfield, Larry C. Giunipero, James L. Patterson
Publisher:Cengage Learning
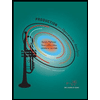
Production and Operations Analysis, Seventh Editi...
Operations Management
ISBN:9781478623069
Author:Steven Nahmias, Tava Lennon Olsen
Publisher:Waveland Press, Inc.