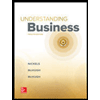
Understanding Business
12th Edition
ISBN: 9781259929434
Author: William Nickels
Publisher: McGraw-Hill Education
expand_more
expand_more
format_list_bulleted
Concept explainers
Question
A company has a factory that is designed so that it is most efi cient (average unit cost is minimized) when producing 15,000 units of output each month. However, it has an absolute maximum output capability of 17,250 units per month, and can produce as little as 7,000 units per month without corporate headquarters shifting production to another plant. If the factory produces 10,925 units in October, what is the capacity utilization rate in October for this factory? |
Expert Solution

This question has been solved!
Explore an expertly crafted, step-by-step solution for a thorough understanding of key concepts.
This is a popular solution
Trending nowThis is a popular solution!
Step by stepSolved in 2 steps

Knowledge Booster
Learn more about
Need a deep-dive on the concept behind this application? Look no further. Learn more about this topic, management and related others by exploring similar questions and additional content below.Similar questions
- Compute the capacity (i.e. processing rate) for each of the following scenarios. Convertyour answers to parts per hour.a. A four-station line with single-machine stations, where the average processing timesare 15, 20, 10 and 12 minutes, respectively.b. A three-station line where the number of machines at stations 1, 2 and 3 is 2, 6, and3, respectively; and the average processing times are 10, 24 and 18 minutes,respectively.arrow_forwardThe exclusive Swink Golf Driving Range has had astandard price of $15 per hour. The facility has 36 golfing stations,with average usage of 50%, 10 hours a day, 7 days a week. MorganSwink, the owner, would like to enhance revenue. He proposes newpricing at $10 per hour on weekdays and $20 per hour on weekends.He estimates that weekday usage will increase to 60% and weekendusage will remain at 500/o, even with the price increase. Variable costis a consistent $3 per hour. Which strategy is better?arrow_forwardAn airline company must plan its fleet capacity and its long-term schedule of aircraft usage. For one flight segment, the average number of customers per day is 70, which represents a 65 percent utilization rate of the equipment assigned to the flight segment. If demand is expected to increase to 91 customers for this flight segment in three years, what capacity requirement should be planned? Assume that management deems that a capacity cushion of 35 percent is appropriate. The needed capacity requirement is customers per day. (Enter your response rounded up to the next whole number.)arrow_forward
- You are the operations manager for Louisiana Oysters, Inc. The company has designed new "Oyster shucking" knife that is expected to reduce risk of injury to the user. Your firm plans to begin production of these knives soon. Either of two machines, A or B could be used for in-house production. Machine A would have a fixed cost of $6000 and a variable cost of $5 per knife produced, and machine B would have a fixed cost of $9600 but a variable cost of $3 per knife. Each knife is expected to sell for $15. Determine the Range of annual “Volume of Business“[Q], for which each of the two alternative machines would be optimal i.e. best. Hint: Compute various break-even points for your evaluationarrow_forwardUse the following information for the next 3 problems: ABC Company plans to construct a 60,000 sq. ft private warehouse and rent public warehouse as needed. Warehouse inventory turns at the rate of 2 times per month. One pound of merchandise occupies 0.2 cubic feet of warehouse space and can be stacked 10 feet high. Given aisles, and normal operating efficiency, only 50 percent of the total warehouse space is actually used for storage. Assume the facility is being built to size so no additional space is allowed for future product growth. A private warehouse can be constructed for $36 per sq. ft. and can be amortized over 20 years. Annual fixed costs amount to $20 per sq. ft. of total space. The cost of operation is $0.03 per pound of throughput. Space may also be rented for a storage charge on inventory of $0.06 per pound per month and a handling charge of $0.05 per pound of throughput. Monthly demands for a typical year are as follows: Month Demand (lb) Jan 2,000,000…arrow_forwardThe annual sales of Crimson Pharmacy are expected to be given by S = 2.5 + 0.4t million dollars t years from now, whereas the annual sales of Cambridge Pharmacy are expected to be given by S = 1.2 + 0.8t million dollars t years from now. When will Cambridge's annual sales first surpass Crimson's annual sales?arrow_forward
- Hickory Manufacturing Company forecasts the following demand for a product (in thousands of units) over the next five years. Year 1 2 3 4 5 Forecast demand 62 84 86 90 90 Currently the manufacturer has seven machines that operate on a two-shift (eight hours each) basis. Thirty days per year are available for scheduled maintenance of equipment with no process output. Assume there are 250 workdays in a year. Each manufactured good takes 20 minutes to produce. What is the effective capacity of the factory? Round your answer down to the nearest whole number. units/year Given the five-year forecast, how much extra capacity is needed each year? Use a minus sign to enter an answer, if there is excess capacity. Round your answers to the nearest whole number. Year 1 2 3 4 5 Extra capacity needed (units) Does the firm need to buy more machines? If so, how many? When? If your answer is zero, enter "0". Round your answers up to the nearest whole number.…arrow_forwardA manager must decide which type of machine to buy, A, B, or C. Machine costs (per individual machine) are as follows: Machine Cost $50,000 A B $40,000 C $70,000 Product forecasts and processing times on the machines are as follows: PROCCESSING TIME PER UNIT (minutes) Annual Product Demand 1 2 3 4 18,000 25,000 15,000 9,000 A 1 5 4 5 A B C B Click here for the Excel Data File 6531 Total processing time in minutes per machine: a. Assume that only purchasing costs are being considered. Compute the total processing time required for each machine type to meet demand, how many of each machine type would be needed, and the resulting total purchasing cost for each machine type. The machines will operate 8 hours a day, 220 days a year. (Enter total processing times as whole numbers. Round up machine quantities to the next higher whole number. Compute total purchasing costs using these rounded machine quantities. Enter the resulting total purchasing cost as a whole number.) C 2 1 2 6arrow_forwardABC Inn has 2 departments: rooms and F&B. the rooms department has a CMR of 0.6 and the F&B department has a CMR of 0.4 the rooms department take in 70% of total revenue and the F&B department takes in 30% of total revenue. If the combined total monthly fixed costs for the entire hotel are equal to $100,00. What is the break-even level of sales?arrow_forward
- Deforrest Marine Motors manufactures engines for the speedboat racing circuit. As part of their annual planning cycle, they forecasted demand for the next four quarters. The number of available days of production and the anticipated demand are given below. Employees Production Rate Production Cost Backorder Cost Overtime Cost Overtime Limit Demand Q1 2,400 6,019,000 They also estimated many of the costs required to conduct operations planning. Some of these key figures are listed below. 30 70 units/employee/quarter Q2 2,200 $1,000/unit $200/unit/quarter $1,500/unit <= 25% of Reg. Production Q3 1,700 Q4 1,800 Hire Cost Fire Cost Subcontracting Cost Subcontracting Limit Inventory Cost Initial Inventory $1,200/employee $800/employee $1,800/unit 400 units maximum $100/unit/quarter 280 units Deforrest Marine Motors wishes to maintain the current number of employees for the entire year to follow a level strategy balanced with inventory and backorders as needed. What is the total cost of this…arrow_forwardUse the following for the next 2 questions: A company forecasts that it will ship 120,000 boxes of product in June. The product has a monthly turnover of 3. The company plans to use its facility to ship 80,000 boxes and the balance of the 40,000 boxes will ship from a rented facility. Space may be rented for a charge of $7 per box per month with an in-and-out handling charge of $0.45 per box shipped. 1. What is the rented (fixed) storage cost for June? - $280,000 - $180,000 - $42,500 - $250,000 - $93,333 - $153,333 - $173,333 2. What is the rented variable cost for June? - $33,333 - $43,333 - $6,000 - $38,000 - $18,000 - $28,000 - $23,333arrow_forwardThe measure of production that considers historical and estimated future production levels and cyclical fluctuations is referred to as: Group of answer choices expected capacity normal capacity theoretical capacity practical capacityarrow_forward
arrow_back_ios
SEE MORE QUESTIONS
arrow_forward_ios
Recommended textbooks for you
- Understanding BusinessManagementISBN:9781259929434Author:William NickelsPublisher:McGraw-Hill EducationManagement (14th Edition)ManagementISBN:9780134527604Author:Stephen P. Robbins, Mary A. CoulterPublisher:PEARSONSpreadsheet Modeling & Decision Analysis: A Pract...ManagementISBN:9781305947412Author:Cliff RagsdalePublisher:Cengage Learning
- Management Information Systems: Managing The Digi...ManagementISBN:9780135191798Author:Kenneth C. Laudon, Jane P. LaudonPublisher:PEARSONBusiness Essentials (12th Edition) (What's New in...ManagementISBN:9780134728391Author:Ronald J. Ebert, Ricky W. GriffinPublisher:PEARSONFundamentals of Management (10th Edition)ManagementISBN:9780134237473Author:Stephen P. Robbins, Mary A. Coulter, David A. De CenzoPublisher:PEARSON
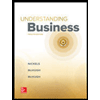
Understanding Business
Management
ISBN:9781259929434
Author:William Nickels
Publisher:McGraw-Hill Education
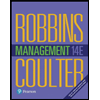
Management (14th Edition)
Management
ISBN:9780134527604
Author:Stephen P. Robbins, Mary A. Coulter
Publisher:PEARSON
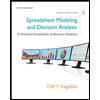
Spreadsheet Modeling & Decision Analysis: A Pract...
Management
ISBN:9781305947412
Author:Cliff Ragsdale
Publisher:Cengage Learning
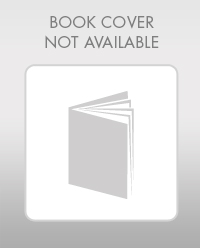
Management Information Systems: Managing The Digi...
Management
ISBN:9780135191798
Author:Kenneth C. Laudon, Jane P. Laudon
Publisher:PEARSON
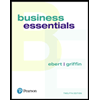
Business Essentials (12th Edition) (What's New in...
Management
ISBN:9780134728391
Author:Ronald J. Ebert, Ricky W. Griffin
Publisher:PEARSON
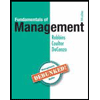
Fundamentals of Management (10th Edition)
Management
ISBN:9780134237473
Author:Stephen P. Robbins, Mary A. Coulter, David A. De Cenzo
Publisher:PEARSON