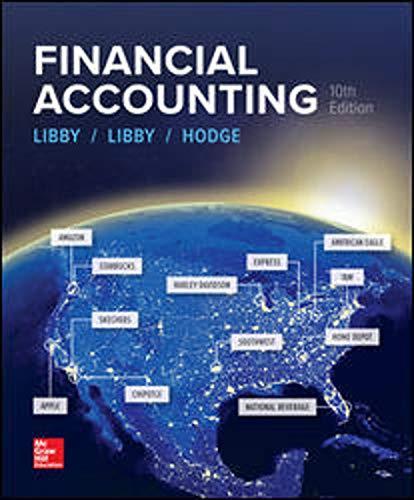
Activity-Based Environmental Cost Assignments
Pinter Company had the following environmental activities and product information:
1. Environmental activity costs
Activity | Costs |
Design products (to reduce pollution) | $ 153,900 |
Test for contamination | 273,600 |
Treat toxic waste | 855,000 |
Operate pollution control equipment | 684,000 |
2. Driver data
Solvent X | Solvent Y | |
Design hours | 3,400 | 2,300 |
Testing hours | 6,100 | 9,100 |
Pounds of waste | 700 | 18,300 |
Machine hours | 3,400 | 72,600 |
3. Other production data
Solvent X | Solvent Y | |
Nonenvironmental production costs | $3,344,000 | $3,876,000 |
Units produced | 380,000 | 380,000 |
Design products | 27 | per design hour |
Testing | 18 | per test hour |
Treating waste | 45 | per pound of waste |
Operating equipment | 9 | per machine hour |
Required:
2. Determine the unit environmental and unit costs of each product using ABC. If required, round your answers to the nearest cent.
Activities | Solvent X | Solvent Y |
Unit environmental cost | $fill in the blank 5 | $fill in the blank 6 |
Unit cost | $fill in the blank 7 | $fill in the blank 8 |
3. What if the design costs increased to $243,900 and the cost of toxic waste decreased to $427,500? Assume that Solvent Y uses 4,600 out of 9,200 design hours. Also assume that waste is cut by 50 percent and that Solvent Y is responsible for 8,122.5 of 8,550 pounds of toxic waste. What is the new environmental cost for Solvent Y? If required, round your intermediate calculations and answer to the nearest cent.
$fill in the blank 9 per unit

Trending nowThis is a popular solution!
Step by stepSolved in 3 steps with 5 images

- Activity-Based Environmental Cost Assignments Pinter Company had the following environmental activities and product information: 1. Environmental activity costs Activity Costs Design products (to reduce pollution) $ 129,600 Test for contamination 230,400 Treat toxic waste 720,000 Operate pollution control equipment 576,000 2. Driver data Solvent X Solvent Y Design hours 2,900 1,900 Testing hours 5,100 7,700 Pounds of waste 600 15,400 Machine hours 2,900 61,100 3. Other production data Solvent X Solvent Y Nonenvironmental production costs $2,176,000 $4,128,000 Units produced 320,000 320,000 What if the design costs increased to $219,600 and the cost of toxic waste decreased to $360,000? Assume that Solvent Y uses 3,800 out of 7,600 design hours. Also assume that waste is cut by 50 percent and that Solvent Y is responsible for…arrow_forward- X Data table - X More info Estimated activity Description of cost pool Estimated Cost Cost driver for this year Machine maintenance costs $ 440,000 Number of machine hours 11,000 340 kg of direct materials @ $50 per kg 70 direct labour hours used @ $30 per labour Engineering change orders $ 300,000 Number of change orders 6,000 hour Hazardous waste disposal $ 910,000 Kg of hazardous materials generated 3,500 140 machine hours used 2$ 1,650,000 Total overhead cost 9 change orders 65 kg of hazardous waste generated Scannell Industries manufactures a variety of custom products. The company has traditionally used a plantwide manufacturing overhead rate based an machine hours to allocate manufacturing overhead to its products. The company estimates that it will incur $1,650,000 in tolal manufacluring overhead costs in the upcoming year and will use 11,000 machine hours. Up to this point, hazardous waste disposal fees have been absorbed into the plantwide manufacturing overhead rate and…arrow_forwardStation 9 ¾ Corporation manufacturers railroad tracks. They are currently using a traditional system, with machine hours as the cost driver. They are considering converting to an ABC system, and want a comparison of the two. Station 9 ¾ has identified the following activity information: Activity Cost Driver Est. Cost Driver Volume Est. Cost Pool Machining Machine Hours 12,000 $119,000 Assembly Direct Labor Hours 15,800 $107,000 Setup Number of Setups 9 $24,300 Total $250,300 The actual cost driver volume that occurred during the production process is below: Machine Hours 8,600 Direct Labor Hours 9,700 Number of Setups 7 What is the Difference between traditional and ABC system?arrow_forward
- Subject - account Please help me. Thankyou.arrow_forwardEstimated Estimated Cost Drivers Activity Cost Overhead Street Mountain Pools Costs Tires Tires Machine set ups $ 90,000 150 350 Assembling $500,000 25,000 15,000 Inspection $400,000 180 320 Question Using the activity-based costing approach, determine the applied overhead rates for Darter Company.arrow_forwardCollin Company manufactures small appliances and uses an activity-based costing system. Information from its system for the year for all products follows: Activity cost pool Total cost Total activity. Assembly Inspection Packaging $460,000 $298,500 $19,700 A. $139,977.76 B. $115,566.24 C. $23,187.50 D. $26.50 20,000 8,500 1,800 machine - hours inspection - hours order The company makes 875 of its stand mixers a year, which requires a total of 27 machine hours, 15 inspection hours, and 9 orders. The stand mixer requires $16.00 in direct materials per unit and $10.50 in direct labor per unit. The stand mixer sells for $160 per unit. What is the profit margin in total for the stand mixer? (Do not round intermediary calculations and round your final answer to the nearest cent.)arrow_forward
- Eccles Corporation uses an activity-based costing system with three activity cost pools. The company has provided the following data concerning its costs and its activity based costing system: Costs: Wages and salaries $ 349,000 Depreciation 290,000 Utilities 199,000 Total $ 838,000 Distribution of resource consumption: Activity Cost Pools Total Assembly Setting Up Other Wages and salaries 65% 20% 15% 100% Depreciation 35% 20% 45% 100% Utilities 15% 75% 10% 100% How much cost, in total, would be allocated in the first-stage allocation to the Assembly activity cost pool? Multiple Choice $125,700 $544,700 $345,533 $358,200arrow_forwardPlease introduction and correct and incorrect option explain!arrow_forwardActivity-Based Product Costing Sweet Sugar Company manufactures three products (white sugar, brown sugar, and powdered sugar) in a continuous production process. Senior management has asked the controller to conduct an activity-based costing study. The controller identified the amount of factory overhead required by the critical activities of the organization as follows: Activity Budgeted Activity Cost Production $462,000 Setup 289,100 Inspection 142,400 Shipping 129,000 Customer service 51,200 Total $1,073,700 The activity bases identified for each activity are as follows: Activity Activity Base Production Machine hours Setup Number of setups Inspection Number of inspections Shipping Number of customer orders Customer service Number of customer service requests The activity-base usage quantities and units produced for the three products were determined from corporate records and are as follows: Machine Hours Number…arrow_forward
- Schedule of Activity Costs Quality Control Activities Product testing Assessing vendor quality Recalls Rework Scrap disposal Product design Training machine operators Warranty work Process audits Activity Cost $55,000 26,000 18,000 29,000 8,000 30,000 46,000 12,000 22,000 From the provided schedule of activity costs, determine the internal failure costs.arrow_forwardKk.335.arrow_forwardNo Ai solutionarrow_forward
- AccountingAccountingISBN:9781337272094Author:WARREN, Carl S., Reeve, James M., Duchac, Jonathan E.Publisher:Cengage Learning,Accounting Information SystemsAccountingISBN:9781337619202Author:Hall, James A.Publisher:Cengage Learning,
- Horngren's Cost Accounting: A Managerial Emphasis...AccountingISBN:9780134475585Author:Srikant M. Datar, Madhav V. RajanPublisher:PEARSONIntermediate AccountingAccountingISBN:9781259722660Author:J. David Spiceland, Mark W. Nelson, Wayne M ThomasPublisher:McGraw-Hill EducationFinancial and Managerial AccountingAccountingISBN:9781259726705Author:John J Wild, Ken W. Shaw, Barbara Chiappetta Fundamental Accounting PrinciplesPublisher:McGraw-Hill Education
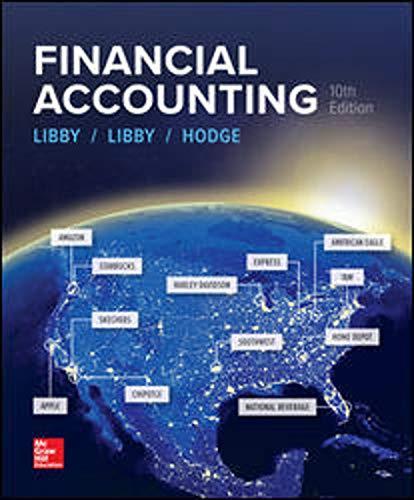
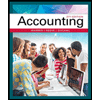
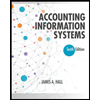
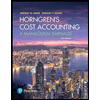
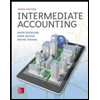
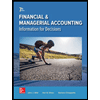