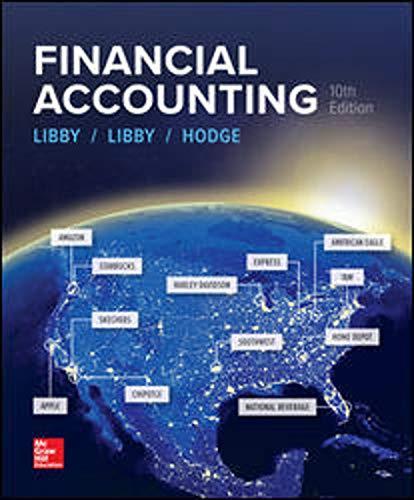
Concept explainers
Resource Usage Model, Special Order
Ehrling, Inc., manufactures metal racks for hanging clothing in retail stores. Ehrling was approached by the CEO of Carly’s Corner, a regional nonprofit food bank, with an offer to buy 350 heavy-duty metal racks for storing canned goods and dry food products. While racks normally sell for $245 each, Carly’s Corner offered $75 per rack. The CEO explained that the number of families they served had grown significantly over the past two years, and that the charity needed additional storage for the donated food items. Since Ehrling is operating at 80 percent of capacity, and Ehrling employees have “adopted” Carly’s Corner as their annual charity, the company wants to make the special order work. Ehrling’s controller looked into the cost of the storage racks using the following information from the activity-based accounting system:
Activity Rate** | |||||
Activity Driver | Unused Capacity |
Quantity Demanded* |
Fixed | Variable | |
Direct materials | Number of racks | 0 | 350 | - | $82 |
Direct labor | Direct labor hours | 0 | 525 | - | 15 |
Setups | Setup hours | 60 | 1 | $150 | 5 |
Inspection | Inspection hours | 800 | 20 | 10 | 5 |
Machining | Machine hours | 6,000 | 175 | 40 | 3 |
*This represents only the amount of resources demanded by the special order being considered. | |||||
**This is expected activity cost divided by activity capacity. |
Expansion of activity capacity for setups, inspection, and machining must be done in steps. For setups, each step provides an additional 20 hours of setup activity and costs $3,000. For inspection, activity capacity is expanded by 2,000 hours per year, and the cost is $20,000 per year (the salary for an additional inspector). Machine capacity can be leased for a year at a rate of $40 per machine hour. Machine capacity must be acquired, however, in steps of 1,500 machine hours.
Required:
1. Compute the change in income for Ehrling, Inc., if the order is accepted.
$
2. Does the order require any change in capacity for setups, packing, or machining?
No
3. Suppose that the packing activity can be eliminated for this order since the customer is in town and does not need to have the racks boxed and shipped. Because of this, direct materials can be reduced by $13 per unit, and direct labor can be reduced by 0.5 hour per unit. How is the analysis affected?
It is now a $ loss if the special order is accepted.

Trending nowThis is a popular solution!
Step by stepSolved in 8 steps with 7 images

- Please answer the 2 questions belowarrow_forwardBarfield Corporation prepares business plans and marketing analyses for start-up companies in the Cleveland area. Barfield has been very successful in recent years in providing effective service to a growing number of clients. The company provides its service from a single office building in Cleveland and is organized into two main client-service groups: one for market research and the other for financial analysis. The two groups have budgeted annual costs of $440,000 and $810,000, respectively. In addition, Barfield has a support staff that is organized into two main functions: one for clerical, facilities, and logistical support (called the CFL group) and another for computer-related support. The CFL group has budgeted annual costs of $216,000, while the annual costs of the computer group are $654,000. Tom Brady, CFO of Barfield, plans to prepare a departmental cost allocation for his four groups, and he assembles the following information: Percentage of estimated dollars of work and…arrow_forwardMilano Pizza is a small neighborhood pizzeria that has a small area for in-store dining as well as offering take-out and free home delivery services. The pizzeria’s owner has determined that the shop has two major cost drivers—the number of pizzas sold and the number of deliveries made. The pizzeria’s cost formulas appear below: Fixed Cost per Month Cost per Pizza Cost per Delivery Pizza ingredients $ 4.90 Kitchen staff $ 6,010 Utilities $ 660 $ 0.80 Delivery person $ 2.60 Delivery vehicle $ 680 $ 2.00 Equipment depreciation $ 440 Rent $ 1,970 Miscellaneous $ 780 $ 0.10 In November, the pizzeria budgeted for 1,710 pizzas at an average selling price of $20 per pizza and for 190 deliveries. Data concerning the pizzeria’s actual results in November were as follows: Actual Results Pizzas 1,810 Deliveries 170 Revenue $ 36,800 Pizza ingredients $ 8,110 Kitchen staff $ 5,950 Utilities $ 910 Delivery person $…arrow_forward
- C. W. McCall sells a goldplated souvenir mug; McCall expects to sell 1,400 units for $35 each to earn a $15 contribution margin per unit. Janice McCall, president, expects the year’s total market to be 35,000 units. For the year just completed, the local college won the national hockey championship, and as a result, the total actual market was 150,000 units. C. W. McCall sold 3,000 units and calculates sales variances using contribution margin. What is the firm’s sales volume variance?arrow_forwardQuality Clothing, Inc., produces skorts and jumper uniforms for school children. In the process of cutting out the cloth pleces for each product, a certain amount of scrap cloth is produced. Quality has been selling this cloth scrap to Jorge's Scrap Warehouse for $3.30 p pound. Last year, the company sold 42,000 lb. of scrap, which would be enough to make 10,500 teddy bears that the management of Quality is now interested in producing. Their processes would need some reprogramming, particularly in the cutting and stitching processes, but it would require no additional worker training. However, new packaging would be needed. The total variable cost to produce the teddy bears $3.80. Fixed costs would increase by $93,000 per year for the lease of the packaging equipment and Quality estimates it could produce and sell 10,500 teddy bears per year. Finished teddy bears could be sold for $18.00 each. Calculate the effect on operating Income. Round your answers to the nearest dollar. Sell at…arrow_forwardAssume that you desire to operate a food truck business. You have five food trucks. Some trucks will need more repairs than others. Based on online research and discussions with other food truck owners, you determine that in a given year the following possibilities are likely. The probability of few repairs is 20% and the estimated cost is $2,500 The probability of moderate repairs is 60% with an estimated cost of $5,000 The probability of extensive repairs is 20% with an estimated cost of $25,000. What is the average expected cash flow out for repairs, based on these probabilities? Type your answer without commas or decimal places or dollar signs.arrow_forward
- Quality Clothing, Inc., produces skorts and jumper uniforms for school children. In the process of cutting out the cloth pieces for each product, a certain amount of scrap cloth is produced. Quality has been selling this cloth scrap to Jorge's Scrap Warehouse for $3.15 per pound. Last year, the company sold 39,000 lb. of scrap, which would be enough to make 9,750 teddy bears that the management of Quality is now interested in producing. Their processes would need some reprogramming, particularly in the cutting and stitching processes, but it would require no additional worker training. However, new packaging would be needed. The total variable cost to produce the teddy bears $3.80. Fixed costs would increase by $94,000 per year for the lease of the packaging equipment and Quality estimates it could produce and sell 9,750 teddy bears per year. Finished teddy bears could be sold for $18.00 each. Calculate the effect on operating income. Round your answers to the nearest dollar. Sell at…arrow_forwardMilano Pizza is a small neighborhood pizzeria that has a small area for in-store dining as well as offering take-out and free home delivery services. The pizzeria's owner has determined that the shop has two major cost drivers-the number of pizzas sold and the number of deliveries made. The pizzeria's cost formulas appear below: Fixed Cost per Month Pizza ingredients Kitchen staff Utilities Delivery person Delivery vehicle Equipment depreciation Rent Miscellaneous Pizzas Deliveries Revenue Pizza ingredients Kitchen staff Utilities Delivery person Delivery vehicle Equipment depreciation Rent $ 5,910 $ 610 Miscellaneous $ 630 $ 400 $ 1,870 $ 730 In November, the pizzeria budgeted for 1,560 pizzas at an average selling price of $15 per pizza and for 220 deliveries. Data concerning the pizzeria's actual results in November appear below: Actual Results. 1,660 200 $ 25,450 $ 7,210 $ 5,850 $ 885 $ 620 $ 986 $ 400 Cost per Pizza $ 4.40 $ 1,870 $ 790 $ 0.30 Cost per Delivery $ 0.15 $ 3.10 $…arrow_forwardKim Epson operates a full-service car wash, which operatesfrom 8 a.m. to 8 p.m., 7 days a week. The car wash has two sta-tions: an automatic washing and drying station and a manualinterior cleaning station. The automatic washing and dryingstation can handle 30 cars per hour. The interior cleaningstation can handle 200 cars per day. Based on a recent year-end review of operations, Kim estimates that future demandfor the interior cleaning station for the 7 days of the week, expressed in average number of cars per day, would be asfollows:Day Mon. Tues. Wed. Thurs. Fri. Sat. Sun.Cars 160 180 150 140 280 300 250By installing additional equipment (at a cost of $50,000), Kimcan increase the capacity of the interior cleaning station to300 cars per day. Each car wash generates a pretax contribu-tion of $4.00. Should Kim install the additional equipment ifshe expects a pretax payback period of three years or less?arrow_forward
- AccountingAccountingISBN:9781337272094Author:WARREN, Carl S., Reeve, James M., Duchac, Jonathan E.Publisher:Cengage Learning,Accounting Information SystemsAccountingISBN:9781337619202Author:Hall, James A.Publisher:Cengage Learning,
- Horngren's Cost Accounting: A Managerial Emphasis...AccountingISBN:9780134475585Author:Srikant M. Datar, Madhav V. RajanPublisher:PEARSONIntermediate AccountingAccountingISBN:9781259722660Author:J. David Spiceland, Mark W. Nelson, Wayne M ThomasPublisher:McGraw-Hill EducationFinancial and Managerial AccountingAccountingISBN:9781259726705Author:John J Wild, Ken W. Shaw, Barbara Chiappetta Fundamental Accounting PrinciplesPublisher:McGraw-Hill Education
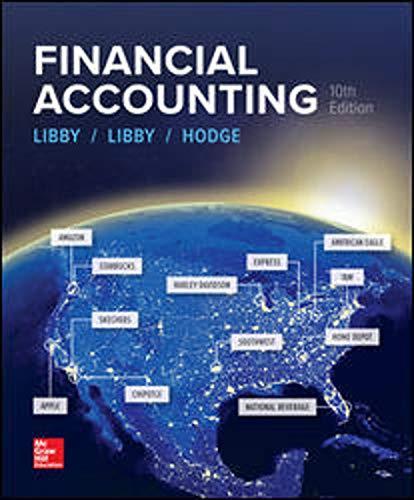
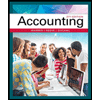
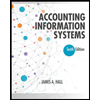
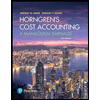
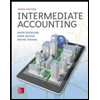
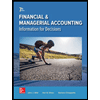