PipeFlow_AE341_ESmith
pdf
School
San Diego State University *
*We aren’t endorsed by this school
Course
341
Subject
Mechanical Engineering
Date
Apr 3, 2024
Type
Pages
13
Uploaded by ChiefDeerMaster1083
April 5, 2023 Pipe Flow AE: 341 Fluid Mechanics Laboratory. Section 1004 Author Emilee Smith Instructor Jose Moreto
Pipe Flow Emilee Smith i Contents Abstract ...........................................................................................................................................
1
Introduction .....................................................................................................................................
1
Theory .............................................................................................................................................
2
Procedure and Equipment ...............................................................................................................
3
Results and Discussion ...................................................................................................................
6
Conclusion ......................................................................................................................................
8
Acknowledgements .........................................................................................................................
8
References. ......................................................................................................................................
9
Appendices ....................................................................................................................................
10
Questions
...................................................................................................................................
10
Table of Figures Figure 1: H1D Volumetric Hydraulic Bench.. Adapted from ref. (2) \ ..........................................
3
Figure 3: Apparatus with Water and Mercury Manometers [3] .....................................................
4
Figure 2: What Controls the Flow [3] .............................................................................................
4
Figure 4: Mercury Manometer [3] ..................................................................................................
4
Figure 5: Water Manometer [3] ......................................................................................................
4
Figure 6: Thermometer [3]
..............................................................................................................
5
Figure 7: Air Valve Release [3] ......................................................................................................
5
Figure 8: Graduated Beaker [3] ......................................................................................................
5
Figure 9: f vs Re on Moody Diagram .............................................................................................
7
Figure 10: Log(hL) vs log(V) for Laminar and Turbulent Flow ....................................................
7
Pipe Flow Emilee Smith 1 Abstract Using a long pipe apparatus with two different kinds of manometers, water and mercury, this lab provided experimental data for the head loss variation with velocity over Reynolds number regarding both laminar and turbulent flows. With this data, calculated results could be compared to the variation of friction factor and Reynolds number. The experimental data was then plotted on the Moody Chart to analyze the types of flow the occurred and estimate an approximate wall roughness, which was concluded to be 0.0012 mm. Nomenclature
: f Friction Factor Re Reynolds Number 𝐿
Length 𝑉
Velocity 𝑔
Gravity 𝑒
Wall Roughness 𝑇
Temperature 𝑣
Kinematic Viscosity 𝐷
Diameter ℎ
Head Loss 𝛾
Specific Weight Introduction This lab report covers the Pipe Flow Lab. The purpose of this lab is to study the flow inside a long and thin pipe in order to observe the variation of head loss with velocity over a range of Reynolds numbers including both laminar and turbulent flows, and to compare the variation of friction factor with Reynolds number with published results [3]. This experiment was performed by Emilee
Your preview ends here
Eager to read complete document? Join bartleby learn and gain access to the full version
- Access to all documents
- Unlimited textbook solutions
- 24/7 expert homework help
Pipe Flow Emilee Smith 2 Smith, Lana Ayyash, and Brenna Gallagher on March 16, 2023, at San Diego State University as a requirement for this course, AE 341, Fluid Mechanics Laboratory. Theory With this experiment we can analyze laminar and turbulent flow which are essential fluid mechanic properties. Laminar flow is steady, comprised only of one component, velocity. Turbulent is unsteady, random flow, with components in all directions. In between laminar and turbulent is transitional. These types of flow relate most importantly to Reynolds number, Re, which is “the ratio of the inertia to viscous effects in the flow” [4]. Depending on the value of the Reynolds number, flow can be described as one of the three types mentioned, although the exact numbers vary. We can find the Reynolds number using fluid velocity, density of our fluid, viscosity, and size of the pipe. According to Fundamentals of Fluid Mechanics,
“the flow in a round pipe is laminar if the Reynolds number is less than approximately 2100, turbulent if the Reynolds number if greater than approximately 4000, and transitional (or switching between laminar and turbulent) if the Reynolds number is between these two limits” [4]. With this lab, we can plot our experimental data on the Moody Chart and observe the type of flows that occurred throughout then experiments. 𝑅𝑒 =
𝑉𝐷
𝑣
Equation 1 𝑄
ଵ
=
𝑉
ଵ
Δ𝑡
ଵ Equation 2 𝑄
ଶ
=
𝑉
ଶ
Δ𝑡
ଶ Equation 3 𝑄
̇
௧௨
=
(𝑄
1
+ 𝑄
2
)
2
Equation 4 𝑇
௩
=
𝑇
+ 𝑇
2
Equation 5
Pipe Flow Emilee Smith 3 ℎ
= 𝑓
𝐿
𝐷
𝑉
ଶ
2𝑔
Equation 6 Procedure and Equipment For this experiment, we used the provided Volumetric Hydraulic Bench shown in Figure 1. In addition to the Hydraulic Bench, we used the apparatus seen in Figure 2 which includes both mercury and water manometers. This system has a 524mm long pipe with a diameter of 3mm. Figure 1: H1D Volumetric Hydraulic Bench.. Adapted from ref. (2)
\ Volumetric Hydraulic Bench Manufacturer. TecEquipment Model. H1D Sump Tank capacity. 160 Liters. Collecting Tank capacity 35 Liters. Pump capacity 0 to 60 liters/minute at 1.5 m head Adapted from ref. (2).
Pipe Flow Emilee Smith 4 Figure 3: Apparatus with Water and Mercury Manometers [3] Figure 5: Water Manometer [3]
Figure 4: Mercury Manometer [3]
Figure 2: What Controls the Flow [3]
Your preview ends here
Eager to read complete document? Join bartleby learn and gain access to the full version
- Access to all documents
- Unlimited textbook solutions
- 24/7 expert homework help
Pipe Flow Emilee Smith 5 Step by Step Procedure: 1.
Measure the temperature of the water for the experiment using the thermometer seen in figure 6. 2.
Next, turn on the pump and fully open the bench valve and pipe valve a clear all air bubbles from the manometers. a.
Then close pipe valve and Turn OFF pump. b.
Push air valve release (seen in Figure 7) so decrease the level inside manometer to below zero. 3.
Turn the pump back on. 4.
Slowly open the pipe valve until head loss (water) is approximately 50mm. Using the smaller graduated beaker (seen in Figure 8), measure the volume flow rate at volumes of 200mL and 250mL. a.
Calculate volume flow rate: 𝑄 = (
௨
௧ప
)
തതതതതതതതതതത
5.
Then, multiply previous head loss by a factor of 1.25 and measure the volume as done in step 4. a.
Continue doing this for seven runs total (giving us a head loss of 190.73mm). b.
For the eighth run, multiply by 1.5 (286.1mm). 6.
After this we are out of capacity range of the water manometer and need to move to the mercury manometer. Figure 6: Thermometer [3] Figure 7: Air Valve Release [3]
Figure 8: Graduated Beaker [3]
Pipe Flow Emilee Smith 6 a.
Conduct four runs using mercury with an increment factor of 1.5. 7.
Fill out the table provided. 8.
Finally, turn off pump. Results and discussion After conducting the experiment, we used the data collected to calculate the volume flow rate, Q. Using the volume flow rate, we could then calculate the velocity of the water through the pipe for every run. Once we had all our variables, head loss, length of the pipe, diameter, velocity, and gravity, the friction factor for each run was calculated and recorded. Reynolds number was also calculated using velocity, diameter, and kinematic viscosity. The experimental results were plotted on the Moody Diagram as shown in Figure 9. As you can see, our flow begins laminar and proceeds to become turbulent. Using this graph, we can analyze and approximate a wall roughness for the pipe. Our data concluded a roughness of 0.0012 mm. Secondly, Figure 10 shows a graph of log(ℎ
) 𝑣𝑠 log(𝑉)
in both cases, laminar and turbulent flows. The first seven runs proved to be laminar, all with Reynolds number below 2100, and the final 6 runs were turbulent, with Reynolds numbers above (or near) 4000. The expected slopes for laminar and turbulent flows on the log(ℎ
) 𝑣𝑠 log(𝑉)
graph were one and two, respectively. The experimental results, also depicted on Figure 10, gave us slopes of 1.1845 and 1.9831. For laminar flow, our percent error was 18.5% and for turbulent, 0.8%. The results for turbulent are understandably similar because turbulent flow is so random and irregular, with a much wider range to obtain. Laminar is linear and consistent and it is more difficult to keep a flow laminar.
Pipe Flow Emilee Smith 7 Figure 9: f vs Re on Moody Diagram Figure 10: Log(hL) vs log(V) for Laminar and Turbulent Flow
Your preview ends here
Eager to read complete document? Join bartleby learn and gain access to the full version
- Access to all documents
- Unlimited textbook solutions
- 24/7 expert homework help
Pipe Flow Emilee Smith 8 Conclusion This experiment provided a comprehensive understanding of the different flows, turbulent and laminar. We were able to easily estimate a wall roughness for the pipe to be 0.0012 by plotting our experimental data on the Moody Diagram. The results of the log vs log graph, although with percent errors of 18% and 0.8% for laminar and turbulent flow respectively, the numbers were still close to expected slopes of 1 and 2. Our results confirmed the relationship between Reynolds number and both laminar and turbulent flow, laminar remaining under 2100 and turbulent over 4000. Acknowledgements All experimental data were collected with the assistance of Emilee Smith, Lana Ayyash, and Breanna Gallagher. We thank San Diego State University for providing the necessary facilities, and Jose Moreto for the insightful instructions.
Pipe Flow Emilee Smith 9 References. 1. Liu X. Guidance for Writing Reports, AE 341 Lab. 2017. p. 2. 2. H1D Volumetric Hydraulic Bench Data Sheet [Internet]. p. 1–3. Available from: www.tecquipment.com 3. Pipe Flow Lab Instructions from Jose Moreto 4. Munson, B. R. (2009). Fundamentals of Fluid Mechanics
. John Wiley.
Pipe Flow Emilee Smith 10 Appendices Sample Calculations: 𝑄
ଵ
=
𝑉
ଵ
Δ𝑡
ଵ =
100𝑚𝐿 ∗
10
ି
𝑚
ଷ
1𝑚𝐿
59𝑠
= 1.695 ∗ 10
ି
𝑚
ଷ
/𝑠
𝑄
ଶ
=
𝑉
ଶ
Δ𝑡
ଶ =
150𝑚𝐿 ∗
10
ି
𝑚
ଷ
1𝑚𝐿
90.85𝑠
= 1.651 ∗ 10
ି
𝑚
ଷ
/𝑠 𝑄
̇
௧௨
=
(𝑄
1
+ 𝑄
2
)
2
=
(1.695 ∗ 10
−6
𝑚
3
/𝑠 + 1.651 ∗ 10
−6
𝑚
3
/𝑠)
2
= 1.673 ∗ 10
−6
𝑚
3
/𝑠
𝑉 =
𝑄
𝐴
=
1.673 ∗ 10
ି
𝑚
ଷ
/𝑠 7.069 ∗ 10
ି
𝑚
ଶ
= 0.23668 𝑚/𝑠
𝑓 = ℎ
𝐷
𝐿
2𝑔
𝑉
ଶ
= 50 ∗ 10
ଷ
𝑚
0.003𝑚
0.524𝑚
2 ∗
9.795𝑚
𝑠
ଶ
ቀ
0.23668𝑚
𝑠
ଶ
ቁ
ଶ
= 0.10011
𝑅𝑒 =
𝑉𝐷
𝑣
=
0.23668
𝑚
𝑠
∗ 0.003𝑚
1 ∗ 10
ିଷ
𝑚
ଶ
/𝑠
= 710.041
𝑇
௩
=
20 + 21
2
= 20.5°𝐶
Questions Question 1: Can you explain why in the Moody Diagram, in the laminar portion, 𝑓 𝑣𝑠 𝑅𝑒
follows a straight line? Solution: The laminar portion of the Moody Chart follows a straight like because the 𝑓 𝑣𝑠 𝑅𝑒
for laminar flow is linear: 𝑓 =
ସ
ோ
.
Your preview ends here
Eager to read complete document? Join bartleby learn and gain access to the full version
- Access to all documents
- Unlimited textbook solutions
- 24/7 expert homework help
Pipe Flow Emilee Smith 11 Question 2: Do you expect to have the same slopes when you plot log(ℎ
) 𝑣𝑠 log(𝑉)
in both cases, laminar and turbulent flows?
Solution: I do not expect the have the same slopes when I plot log(ℎ
) 𝑣𝑠 log(𝑉)
in both cases because the expected values that are provided show a slope of 1 for Laminar flow and a slope of 2 for Turbulent. Therefore, I expect the slopes of my experimental data and calculations to be like the expected values with deviation.
Related Questions
Fluid mechanic
arrow_forward
Question No. 17
arrow_forward
Py
Flow
FIGURE 6.2 Portion of a fluid distribution system showing
variations in velocity, pressure, and elevation.
Reference level
2.
arrow_forward
CS) Flow through a heat exchanger tube is to be studied by means of a 1/10 scale model. If the tmateaangeraarmall, carries widecreme de ratio of pressure losses between the model and the prototype if water is used in the model.
arrow_forward
% ParametersD = 0.1; % Diameter of the tube (m)L = 1.0; % Length of the tube bundle (m)N = 8; % Number of tubes in the bundleU = 1.0; % Inlet velocity (m/s)rho = 1.2; % Density of the fluid (kg/m^3)mu = 0.01; % Dynamic viscosity of the fluid (Pa.s)
% Define the grid size and time stepdx = D/10; % Spatial step size (m)dy = L/10; % Spatial step size (m)dt = 0.01; % Time step size (s)
% Calculate the number of grid points in each directionnx = ceil(D/dx) + 1;ny = ceil(L/dy) + 1;
% Create the velocity matrixU_matrix = U * ones(nx, ny);
% Perform the iterationsfor iter = 1:100 % Calculate the velocity gradients dUdx = (U_matrix(:, 2:end) - U_matrix(:, 1:end-1)) / dx; dUdy = (U_matrix(2:end, :) - U_matrix(1:end-1, :)) / dy; % Calculate the pressure gradients dpdx = -mu * dUdx; dpdy = -mu * dUdy; % Calculate the change in velocity dU = dt * (dpdx / rho); % Update the velocity matrix U_matrix(:, 2:end-1) = U_matrix(:, 2:end-1) + dU; % Apply…
arrow_forward
please help me with this question. Thank you!
arrow_forward
Please include mathematical expressions with theoretical explanations.
arrow_forward
Engineering fluid mechanics:
pathlines, streamlines, and streaklines.
A.) If somehow you could attach a light to a fluid particle and take a time exposure, would the image you photographed be a pathline or streakline? Explain from definition of each.
arrow_forward
Given problem:
a.) At temperatures of 100° F and 120 psi absolute, calculation of above properties for methane (CH4): what is the barometric pressure if the gauge reading is 104.5 Psig?
b.) A pipe transports an incompressible fluid. The volume flow rate is 10m3/s at point 1 along the pipe. The area halves at spot 2 along the pipe. At site 2, what is the volume flow rate?
arrow_forward
Answer question 4
arrow_forward
1.1." In Example 1.1:
(a) Estimate the pressure drop required.
(b) Estimate the pumping power required.
See any fluid mechanics textbook for methods of making these estimates.
Evample 1.1. The area of the Los Angeles basin is 4083 square miles. The heavily
nalluted air layer is assumed to be 2000 ft thick on average. One solution to Los
Angeles' problems would be to pump this contaminated air away. Suppose that we
wish to pump out the Los Angeles basin every day and that the air must be pumped
S0 miles to the desert near Palm Springs. (We assume the residents of Palm Springs
won't complain.) Assume also that the average velocity in the pipe is 40 fu/s. Estimate
the required pipe diameter.
The flow rate required is
АН
4083 mi? 2000 ft (5280 f/mi)?
Q =
Δι
ft'
%3D
24 h
= 2.63 - 10º It
3600 s/h
= 7.46 - 10
and the required pipe diameter is
4- 2.63 - 10° ft/s
D =
= 9158 ft = 2791 m
T: 40 fi/s
This is about three times the height of the tallest man-made structure, and far
beyond our current…
arrow_forward
Please solve the following
arrow_forward
%or l. ln. .
o [Template] exami..
->
Ministry of Higher Education
& Scientific Research
Tikrit University
College of Engineering
Mechanical Engineering Dept.
Class : 2nd year
Subject: Principles of Fluid Mechanics
Time: 1:15 hrs
Date: 11/3 / 2021
Final Exam
2020-2021
Q1:-The gate AB as shown in fig.1 has long 1 m and wide 0.9 m .Find the force
Fon The gate AB and also find the centre of pressure X
8 m
3 m
Oil
S-0.81
7 m
Fig.1
Q2:-
A wood cone floats in water in the position shown in fig.2.The specific gravity
of the wood is 0.6.Would it be stable?
D7m
Fig.2
Water
By
Asst.Prof.Dr.Muhammad A.Eleiwi
II
>
arrow_forward
Three types of fluids stack in an open tank as shown in the plot.
Select the expression of the gage pressure at location 2, P2(gage)=______
A.
B.
C.
D.
patm
arrow_forward
ES
Font
English (United Kingdom)
▬▬ Q Search
>
Text Predictions: On
ALT
Paragraph
S
Accessibility: Good to go
Styles
The following parameters characterise a liquid-fuelled rocket engine: stagnation
pressure P0=100bar; stagnation temperature TO=3300K; nozzle exit diameter DE=1.0m;
throat diameter=0.1 m; gas constant R=692 Jkg-1 K -1; ratio of specific heats
cp/cV=y=1.25. Estimate the following: static pressure at the exit plane, exit Mach
number.
Heading
Focus
Editing
ENG
UK
arrow_forward
SEE MORE QUESTIONS
Recommended textbooks for you
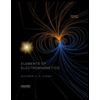
Elements Of Electromagnetics
Mechanical Engineering
ISBN:9780190698614
Author:Sadiku, Matthew N. O.
Publisher:Oxford University Press
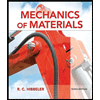
Mechanics of Materials (10th Edition)
Mechanical Engineering
ISBN:9780134319650
Author:Russell C. Hibbeler
Publisher:PEARSON
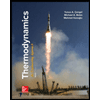
Thermodynamics: An Engineering Approach
Mechanical Engineering
ISBN:9781259822674
Author:Yunus A. Cengel Dr., Michael A. Boles
Publisher:McGraw-Hill Education
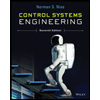
Control Systems Engineering
Mechanical Engineering
ISBN:9781118170519
Author:Norman S. Nise
Publisher:WILEY
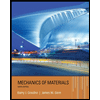
Mechanics of Materials (MindTap Course List)
Mechanical Engineering
ISBN:9781337093347
Author:Barry J. Goodno, James M. Gere
Publisher:Cengage Learning
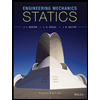
Engineering Mechanics: Statics
Mechanical Engineering
ISBN:9781118807330
Author:James L. Meriam, L. G. Kraige, J. N. Bolton
Publisher:WILEY
Related Questions
- CS) Flow through a heat exchanger tube is to be studied by means of a 1/10 scale model. If the tmateaangeraarmall, carries widecreme de ratio of pressure losses between the model and the prototype if water is used in the model.arrow_forward% ParametersD = 0.1; % Diameter of the tube (m)L = 1.0; % Length of the tube bundle (m)N = 8; % Number of tubes in the bundleU = 1.0; % Inlet velocity (m/s)rho = 1.2; % Density of the fluid (kg/m^3)mu = 0.01; % Dynamic viscosity of the fluid (Pa.s) % Define the grid size and time stepdx = D/10; % Spatial step size (m)dy = L/10; % Spatial step size (m)dt = 0.01; % Time step size (s) % Calculate the number of grid points in each directionnx = ceil(D/dx) + 1;ny = ceil(L/dy) + 1; % Create the velocity matrixU_matrix = U * ones(nx, ny); % Perform the iterationsfor iter = 1:100 % Calculate the velocity gradients dUdx = (U_matrix(:, 2:end) - U_matrix(:, 1:end-1)) / dx; dUdy = (U_matrix(2:end, :) - U_matrix(1:end-1, :)) / dy; % Calculate the pressure gradients dpdx = -mu * dUdx; dpdy = -mu * dUdy; % Calculate the change in velocity dU = dt * (dpdx / rho); % Update the velocity matrix U_matrix(:, 2:end-1) = U_matrix(:, 2:end-1) + dU; % Apply…arrow_forwardplease help me with this question. Thank you!arrow_forward
- Please include mathematical expressions with theoretical explanations.arrow_forwardEngineering fluid mechanics: pathlines, streamlines, and streaklines. A.) If somehow you could attach a light to a fluid particle and take a time exposure, would the image you photographed be a pathline or streakline? Explain from definition of each.arrow_forwardGiven problem: a.) At temperatures of 100° F and 120 psi absolute, calculation of above properties for methane (CH4): what is the barometric pressure if the gauge reading is 104.5 Psig? b.) A pipe transports an incompressible fluid. The volume flow rate is 10m3/s at point 1 along the pipe. The area halves at spot 2 along the pipe. At site 2, what is the volume flow rate?arrow_forward
- Answer question 4arrow_forward1.1." In Example 1.1: (a) Estimate the pressure drop required. (b) Estimate the pumping power required. See any fluid mechanics textbook for methods of making these estimates. Evample 1.1. The area of the Los Angeles basin is 4083 square miles. The heavily nalluted air layer is assumed to be 2000 ft thick on average. One solution to Los Angeles' problems would be to pump this contaminated air away. Suppose that we wish to pump out the Los Angeles basin every day and that the air must be pumped S0 miles to the desert near Palm Springs. (We assume the residents of Palm Springs won't complain.) Assume also that the average velocity in the pipe is 40 fu/s. Estimate the required pipe diameter. The flow rate required is АН 4083 mi? 2000 ft (5280 f/mi)? Q = Δι ft' %3D 24 h = 2.63 - 10º It 3600 s/h = 7.46 - 10 and the required pipe diameter is 4- 2.63 - 10° ft/s D = = 9158 ft = 2791 m T: 40 fi/s This is about three times the height of the tallest man-made structure, and far beyond our current…arrow_forwardPlease solve the followingarrow_forward
arrow_back_ios
SEE MORE QUESTIONS
arrow_forward_ios
Recommended textbooks for you
- Elements Of ElectromagneticsMechanical EngineeringISBN:9780190698614Author:Sadiku, Matthew N. O.Publisher:Oxford University PressMechanics of Materials (10th Edition)Mechanical EngineeringISBN:9780134319650Author:Russell C. HibbelerPublisher:PEARSONThermodynamics: An Engineering ApproachMechanical EngineeringISBN:9781259822674Author:Yunus A. Cengel Dr., Michael A. BolesPublisher:McGraw-Hill Education
- Control Systems EngineeringMechanical EngineeringISBN:9781118170519Author:Norman S. NisePublisher:WILEYMechanics of Materials (MindTap Course List)Mechanical EngineeringISBN:9781337093347Author:Barry J. Goodno, James M. GerePublisher:Cengage LearningEngineering Mechanics: StaticsMechanical EngineeringISBN:9781118807330Author:James L. Meriam, L. G. Kraige, J. N. BoltonPublisher:WILEY
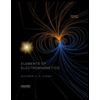
Elements Of Electromagnetics
Mechanical Engineering
ISBN:9780190698614
Author:Sadiku, Matthew N. O.
Publisher:Oxford University Press
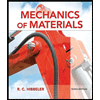
Mechanics of Materials (10th Edition)
Mechanical Engineering
ISBN:9780134319650
Author:Russell C. Hibbeler
Publisher:PEARSON
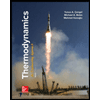
Thermodynamics: An Engineering Approach
Mechanical Engineering
ISBN:9781259822674
Author:Yunus A. Cengel Dr., Michael A. Boles
Publisher:McGraw-Hill Education
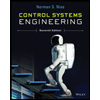
Control Systems Engineering
Mechanical Engineering
ISBN:9781118170519
Author:Norman S. Nise
Publisher:WILEY
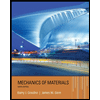
Mechanics of Materials (MindTap Course List)
Mechanical Engineering
ISBN:9781337093347
Author:Barry J. Goodno, James M. Gere
Publisher:Cengage Learning
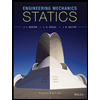
Engineering Mechanics: Statics
Mechanical Engineering
ISBN:9781118807330
Author:James L. Meriam, L. G. Kraige, J. N. Bolton
Publisher:WILEY