Health & SafetyTag Out Assignment
docx
School
Confederation College *
*We aren’t endorsed by this school
Course
EB301
Subject
Mechanical Engineering
Date
Dec 6, 2023
Type
docx
Pages
6
Uploaded by BailiffJackalMaster747
1
Case Study Assignment for Lockout- Tagout Procedures
Abhilash Ajithkumar
Abin Rajan
Albert Pottenplakkil Joseph
Devika Geetha Kumari Somadas
Thalapathi Ravi
EB 301: Health & Safety Management & Inspection
Professor: Karen McKissick
November 13 ,2023
2
Case Study #1
A millwright was assigned to a servicing and maintenance task on an overhead crane. This
millwright was trained in the requirements of the Lockout/Tag out standard as an authorized
employee. The employee initiated the prescribed energy control procedure by turning "off" the
crane's electrical disconnect switch and placing his lock onto this energy isolating device.
However, the disconnect switch lever was corroded, therefore, it broke inside the disconnect
switch assembly. The worker was not aware of this. As a result, when the millwright placed the
lock on the lever in the "off" position, the actual switch located inside the electrical box remained
in the "on" position. When he contacted the energized electrical bus bar located near the bridge
railings, fatal injury occurred.
Q1: What was the root cause for the accident? Could this be prevented and how?
A corroded disconnect switch lever kept the crane in the "on" position, leading the worker to
believe that the crane had been de-energized. This was the result of an inadequate isolation of the
energy source during the lockout/tagout operation, which caused the accident. When the worker
encountered the energized electrical bus bar, this failing to recognize the switch's true state
resulted in a fatal injury. More thorough lockout/tagout procedures are needed to prevent such
situations. It is essential to perform thorough and routine inspections of the equipment, especially
the disconnect switch. The corrosion problem might have been found through routine
maintenance tests and inspections before the lockout procedure was started. Increasing staff
understanding is also crucial; training materials should stress how important it is to verify that
energy sources are truly isolated and identify any weaknesses in lockout/tagout apparatus. In the
end, the incident emphasizes the necessity of taking preventative steps to guarantee that
lockout/tagout protocols are successful. To establish a safer workplace, employers should
prioritize regular maintenance, staff education, and inspections. These precautions not only avert
deadly collisions but also foster a culture of safety by providing all staff members with the
information and resources they need to recognize and mitigate any risks.
Q2: Was there anybody or any party at fault in this accident? Please explain why or why not.
In accidents, determining blame frequently requires a complex study of several variables. In this
instance, it seems that equipment failure more especially, the corroded disconnect switch lever
was more significant than the millwright's interventions. The employer, equipment makers, and
maintenance personnel may all share accountabilities. If the lockout/tagout equipment was not
regularly inspected and maintained, the employer may be held partially liable for the accident.
The equipment's manufacturers should also be closely examined, especially regarding the
disconnect switch's design and robustness. There are obvious possibilities for improvement if the
equipment was not built to endure weather conditions or did not have elements for a clear status
indicator. It is necessary to carry out a comprehensive investigation, including involving
regulatory agencies, to identify the specific responsibilities and liability of each concerned party.
Organizations must commit to continuous evaluations and improvements of their tools,
3
instruction, and lockout/tagout procedures. The adoption of a proactive strategy not only reduces
the probability of said events but also cultivates a safety culture that empowers all staff members
to recognize and mitigate dangers, hence advancing a safer work environment.
Case Study #2
Employees were performing repairs on an 8-ft-diameter pipeline that carried hot oil. They had
properly locked and tagged pumping stations, pipeline valves and the control room prior to
beginning repairs. When the work was completed and inspected, all lockout / tagout safeguards
were removed and all elements were returned to their operating state. At this point, control-room
personnel were alerted that the work was completed, and they were requested to start up the
system 5 hours earlier than it was originally scheduled. Two supervisors were not aware of the
early start-up. They decided to inspect the repairs themselves. They walked inside the pipe with
lights to perform the inspection. As the control-room operators started the system as instructed,
hot oil began to flow through the pipe killing the two supervisors.
Q3: What was the root cause for the accident? Could this be prevented and how?
The main root cause for the incident particularly was not double checking and lack of
communication in a subtle way. The control personals could basically have made sure that
everyone essentially was informed about the starting of the plant prior to the scheduled time,
their re-verification could generally have saved two innocent lives. Also, the two supervisors
could for all intents and purposes have informed about their inspection to the control team or
anyone else there prior to their entry into the pipe, as in case their comms didn’t work other
workers could generally have told that two of the supervisors informed us about conducting an
inspection prior to the starting. The lockout tagout procedure clearly states to re-verify or double-
check as it can help particularly save lives, which for all intents and purposes is quite significant.
Clear channels of communication and coordination need to be established to stop these kinds of
things. Any schedule modifications should be communicated to all parties through a reliable
system, particularly if they include starting up a potentially dangerous system.
Q4: Was there anybody or any party at fault in this accident? Please explain why or why not.
I believe that we specifically are not supposed to for the most part blame anyone without proving
that they really were wrong, as in this case it is not one party that kind of is to blame. Starting the
plant very early that too particularly nearly 5 hours prior to the scheduled time, the control room
personals had more than enough time in their hand to make sure that every single one of the
people in there particularly were informed about their decision. Also, being supervisors, they
didn’t for the most part bother to essentially inform others of their inspection of the pipeline,
even so they had many years of experience their lack of negligence cost them their lives. Clearly
Your preview ends here
Eager to read complete document? Join bartleby learn and gain access to the full version
- Access to all documents
- Unlimited textbook solutions
- 24/7 expert homework help
4
it wouldn’t for the most part be their first time being there while cleaning the pipelines and they
didn’t essentially follow the rules, which really is quite significant. Ultimately, rather than
blaming just one person or party, fault can really be essentially attributed to several factors, such
as very poor communication and a failure to really follow protocol, which is significant. A
generally more thorough understanding of the precise actions and choices that led to the accident
should be provided by the investigation, for all intents and purposes contrary to popular belief.
Case Study #3
A 52-year-old welder died when he was crushed to death by a hydraulic door on a metal
shredder. The employee was attempting to remove a jammed piece of metal from the hydraulic
door on the shredder when the item causing the jam fell away and the door suddenly closed on
him.
Q5: What was the root cause for the accident? Could this be prevented and how? Who was at
fault?
The welder tried to remove the jammed piece of metal from the hydraulic door without following
proper procedures, which resulted in the falling of the jam, and the worker was crushed to death
by the hydraulic door. The root cause for the accident includes the lack of Lockout /Tagout
procedures, problems with the design or maintenance of the equipment, lack of training, and the
worker’s insufficient knowledge of the equipment.
This accident can be prevented by the following measures,
Implementation of lockout/tagout procedures is vital for preventing accidents during
maintenance or the repair of the machinery. In this case, the worker failed to de-energize
and lock-out the shredder first. In addition, he did not close the door and release the
system's residual hydraulic energy. The purpose of lockout/tagout is to avoid hazardous
energy from killing or injuring employee.
Employees should receive proper training on the equipment they are operating, including
safety protocols and emergency procedures. According to OHSA, Section 25 (1)(c) and
Section 25 (2) (a),
In order to ensure the worker's health or safety, the employer's
supplies, machinery, and safety equipment must be kept in good working condition.
Additionally, workers must get knowledge, guidance, and supervision. Also, in Section
42 (1), OHSA, in addition to providing information and instruction to a worker as
required by clause 25 (2) (a), an employer shall ensure that a worker exposed or likely to
be exposed to a hazardous material or to a hazardous physical agent receives, and that the
worker participates in, such instruction and training as may be prescribed.
In this case, both the management and the worker are at fault.
5
The management should be responsible for taking corrective actions at a hazardous
workplace and should be responsible for supervising and providing adequate training to
the workers. Failing to ensure safety at a workplace is a violation of Section 27 (1) (a)
and (b), OHSA.
The worker should be responsible for his/her own health and safety at the workplace. The
worker should be aware of his working conditions and should follow the safety measures.
Under Section 28, OHSA, the duties of a worker at a workplace are expounded.
6
REFERENCE
Occupational Health and Safety Act (2023),
Government of Ontario
Your preview ends here
Eager to read complete document? Join bartleby learn and gain access to the full version
- Access to all documents
- Unlimited textbook solutions
- 24/7 expert homework help
Related Documents
Related Questions
Energy Star Washing Machine
Model #: GTW500ASN
Style: Top Loader
Cubic Feet: 4.5 cubic feet
Yearly Energy Usage (from Energy Guide): 210
kWh/y
Non-Energy Star Washing Machine
Model #: GTW465ASN
Style: Top Loader
Cubic Feet: 4.5 cubic feet
Yearly Energy Usage (from Energy Guide): 175
kWh/yr
Picture of Appliance:
Website Link to Retail Store
Purchase Price: (1) $498.00
Yearly Energy Use (in kWh): 175 kWh/yr
Energy Cost per Year
(Energy usage in kWh from above x .1111
cents/kWh): (3)
Cost Recuperation Estimation
1
Picture of Appliance:
Website Link to Retail Store
Purchase Price: (2) $478.00
Yearly Energy Use (in kWh): 210 kWh/yr
Energy Cost per Year
(Energy usage in kWh from above x.1111
cents/kWh): (4)
Initial Cost Difference: Energy Star Appliance Price (1) - Non-Energy Star Appliance Price (2)
Calculation (Show Your Work):
This is the original upfront price difference. In other words, how much more money the Energy-Star
Appliance costs.
2.
Cost Per Year Difference: Non-Energy Star…
arrow_forward
Assignment Booklet 4B
ce 24: Module 4
6 Identify the safety features shown in this automobile from the following list. Place
your answers in the blank spaces given.
• bumper
• hood
• crumple zones
• roll cage
• side-impact beams
Return to page 75 of the Student Module Booklet and begin Lesson 2.
For questions 7 to 10, read each question carefully. Decide which of the choices BEST
completes the statement or answers the question. Place your answer in the blank
space given.
7. According to Transport Canada, how many Canadians owe their lives to
seat belts between 1990 and 2000?
A. 690
В. 1690
С. 1960
D. 11 690
8. By what percent is the webbing of a seat belt designed to stretch to help
absorb energy in a collision?
A. 0%
B. 5-10%
C. 10-15%
D. 15-20%
9. What is the level of seat belt use in Alberta?
A. 90%
В. 70%
С. 50%
D. 30%
Teacher
arrow_forward
Assignment 1: TIME VALUE OF MONEY
Objective: To further understand the concept of the time value of money.
INSTRUCTIONS:
In each problem,
a. Translate data given in problems into their respective graphical representations - i.e. draw
the correct cash flow diagram.
b. Write down all pertinent given information or data on your paper.
c. Calculate answers correctly.
2. A 12-cylinder heavy-duty diesel engine will have a guaranteed residual value of $1,000
in 5 years. Today (year 0) the equivalent worth of this engine is how much if the interest
rate is 9% per year?
arrow_forward
Need help with this question.
A bit urgently if possible
arrow_forward
19.a. A machine has a coupling that fails once every year and a half. What type of PM task can be created tomake sure that this coupling won’t fail on uptime?A. An electrical PM every six monthsB. An operator PM every yearC. A lubricator PM every eight monthsD. A mechanical PM every year19.b. If mission-critical equipment fails after a PM program is initiated, the best action is toA. install permanent employees to monitor the equipment until the proper maintenance schedule can be created.B. become a critic of the program until changes are made.C. modify the inspection and maintenance schedules to lower the failures.D. double the inspection schedule.19.c. Who is often overlooked as an important source of information and should be asked about PMmaintenance tasks in the program?A. Purchasing departmentB. Computer specialistsC. Machine operatorsD. outside contractors
arrow_forward
plz solve it within 30-40 mins I'll give you multiple upvote
arrow_forward
Assignment 1: Killer Robot
Summary of the case: Bart Matthews, a robot operator at Cybernetics, Inc., has been killed by an out-
of-control robot named Robbie. The creator of the robot, Silicon Technologies, is also in a tight
financial position and had hoped that the robot would put the company back on its feet. It has been
determined that several situations contributed to the death of Matthews:
1. Improper methodology was used in developing the software.
2. Testing of the software was faked.
3. The company pressured Robbie's creators to by-pass testing.
4. Part of the software used in the robot was stolen from another vendor's application.
5. The programmer did not understand or know the code which he used.
6. Security measures used were illegal, and therefore all information gathered in regard to the case
might not be permissible in court.
7. The project leader did not understand or use proper design methodologies.
8. The end-user interface was designed improperly.
Questions for…
arrow_forward
Please explanation required
arrow_forward
https://www.sciencedirect.com/science/article/abs/pii/S0965997822001569
In the literature review, they should present the system installed and the main results obtained. In other words, the enhancement due to the installed system. They have to define the system used in this study. (the report talking about ventilation) pls in briefly
Don’t using chatgpt please urgent
i will give u good feedback
arrow_forward
A robot is used for loading and unloading of parts to automated flexible machines. Loading
time is 1 minute; unloading time is 1.5 minutes; machining time 15 minutes; Robot travel time
between the machines including the inspection time is 3 minutes. Cost of robot C,=30 TL/Hour;
cost of machines C2=40 TL/Hour. How many machines (integer number) should be assigned
to the robot so that the total robot and machine costs per cycle are minimized?
8 -
176
a)
4
b)
3
c)
2
d)
e)
6.
arrow_forward
SUBJECT: Industrial Safety Engineering
Do not use chatgpt , draw in handwritten note and explain deeply
Draw decision tree for following machines I. Any one machine tool Pump II. Air compressor III. Internal combustion engine IV. Boiler V. Electrical motors.
arrow_forward
SEE MORE QUESTIONS
Recommended textbooks for you
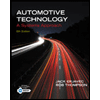
Automotive Technology: A Systems Approach (MindTa...
Mechanical Engineering
ISBN:9781133612315
Author:Jack Erjavec, Rob Thompson
Publisher:Cengage Learning
Related Questions
- Energy Star Washing Machine Model #: GTW500ASN Style: Top Loader Cubic Feet: 4.5 cubic feet Yearly Energy Usage (from Energy Guide): 210 kWh/y Non-Energy Star Washing Machine Model #: GTW465ASN Style: Top Loader Cubic Feet: 4.5 cubic feet Yearly Energy Usage (from Energy Guide): 175 kWh/yr Picture of Appliance: Website Link to Retail Store Purchase Price: (1) $498.00 Yearly Energy Use (in kWh): 175 kWh/yr Energy Cost per Year (Energy usage in kWh from above x .1111 cents/kWh): (3) Cost Recuperation Estimation 1 Picture of Appliance: Website Link to Retail Store Purchase Price: (2) $478.00 Yearly Energy Use (in kWh): 210 kWh/yr Energy Cost per Year (Energy usage in kWh from above x.1111 cents/kWh): (4) Initial Cost Difference: Energy Star Appliance Price (1) - Non-Energy Star Appliance Price (2) Calculation (Show Your Work): This is the original upfront price difference. In other words, how much more money the Energy-Star Appliance costs. 2. Cost Per Year Difference: Non-Energy Star…arrow_forwardAssignment Booklet 4B ce 24: Module 4 6 Identify the safety features shown in this automobile from the following list. Place your answers in the blank spaces given. • bumper • hood • crumple zones • roll cage • side-impact beams Return to page 75 of the Student Module Booklet and begin Lesson 2. For questions 7 to 10, read each question carefully. Decide which of the choices BEST completes the statement or answers the question. Place your answer in the blank space given. 7. According to Transport Canada, how many Canadians owe their lives to seat belts between 1990 and 2000? A. 690 В. 1690 С. 1960 D. 11 690 8. By what percent is the webbing of a seat belt designed to stretch to help absorb energy in a collision? A. 0% B. 5-10% C. 10-15% D. 15-20% 9. What is the level of seat belt use in Alberta? A. 90% В. 70% С. 50% D. 30% Teacherarrow_forwardAssignment 1: TIME VALUE OF MONEY Objective: To further understand the concept of the time value of money. INSTRUCTIONS: In each problem, a. Translate data given in problems into their respective graphical representations - i.e. draw the correct cash flow diagram. b. Write down all pertinent given information or data on your paper. c. Calculate answers correctly. 2. A 12-cylinder heavy-duty diesel engine will have a guaranteed residual value of $1,000 in 5 years. Today (year 0) the equivalent worth of this engine is how much if the interest rate is 9% per year?arrow_forward
- Need help with this question. A bit urgently if possiblearrow_forward19.a. A machine has a coupling that fails once every year and a half. What type of PM task can be created tomake sure that this coupling won’t fail on uptime?A. An electrical PM every six monthsB. An operator PM every yearC. A lubricator PM every eight monthsD. A mechanical PM every year19.b. If mission-critical equipment fails after a PM program is initiated, the best action is toA. install permanent employees to monitor the equipment until the proper maintenance schedule can be created.B. become a critic of the program until changes are made.C. modify the inspection and maintenance schedules to lower the failures.D. double the inspection schedule.19.c. Who is often overlooked as an important source of information and should be asked about PMmaintenance tasks in the program?A. Purchasing departmentB. Computer specialistsC. Machine operatorsD. outside contractorsarrow_forwardplz solve it within 30-40 mins I'll give you multiple upvotearrow_forward
- Assignment 1: Killer Robot Summary of the case: Bart Matthews, a robot operator at Cybernetics, Inc., has been killed by an out- of-control robot named Robbie. The creator of the robot, Silicon Technologies, is also in a tight financial position and had hoped that the robot would put the company back on its feet. It has been determined that several situations contributed to the death of Matthews: 1. Improper methodology was used in developing the software. 2. Testing of the software was faked. 3. The company pressured Robbie's creators to by-pass testing. 4. Part of the software used in the robot was stolen from another vendor's application. 5. The programmer did not understand or know the code which he used. 6. Security measures used were illegal, and therefore all information gathered in regard to the case might not be permissible in court. 7. The project leader did not understand or use proper design methodologies. 8. The end-user interface was designed improperly. Questions for…arrow_forwardPlease explanation requiredarrow_forwardhttps://www.sciencedirect.com/science/article/abs/pii/S0965997822001569 In the literature review, they should present the system installed and the main results obtained. In other words, the enhancement due to the installed system. They have to define the system used in this study. (the report talking about ventilation) pls in briefly Don’t using chatgpt please urgent i will give u good feedbackarrow_forward
- A robot is used for loading and unloading of parts to automated flexible machines. Loading time is 1 minute; unloading time is 1.5 minutes; machining time 15 minutes; Robot travel time between the machines including the inspection time is 3 minutes. Cost of robot C,=30 TL/Hour; cost of machines C2=40 TL/Hour. How many machines (integer number) should be assigned to the robot so that the total robot and machine costs per cycle are minimized? 8 - 176 a) 4 b) 3 c) 2 d) e) 6.arrow_forwardSUBJECT: Industrial Safety Engineering Do not use chatgpt , draw in handwritten note and explain deeply Draw decision tree for following machines I. Any one machine tool Pump II. Air compressor III. Internal combustion engine IV. Boiler V. Electrical motors.arrow_forward
arrow_back_ios
arrow_forward_ios
Recommended textbooks for you
- Automotive Technology: A Systems Approach (MindTa...Mechanical EngineeringISBN:9781133612315Author:Jack Erjavec, Rob ThompsonPublisher:Cengage Learning
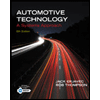
Automotive Technology: A Systems Approach (MindTa...
Mechanical Engineering
ISBN:9781133612315
Author:Jack Erjavec, Rob Thompson
Publisher:Cengage Learning