Case Study of Hy Fybo Design
docx
School
London School of Business and Finance *
*We aren’t endorsed by this school
Course
MANAGERIAL
Subject
Management
Date
Nov 24, 2024
Type
docx
Pages
19
Uploaded by george2550
1
Case Study of Hy Fybo Design
Student Name
Course Name
Professor Name
December 20, 2022
2
Case Study of Hy Fybo Design
Part 1 – Questions
Q 1.
Corporate operations are organized to meet objectives, boost efficiency, and increase
profit. Operations management (OM) seems to be a subdivision of management that
supervises the whole power generation timeframe of a facility or product from the source side
to the completed stage. This involves planning, arranging, and monitoring procedures,
manufacturing and output procedures, and service distribution of manufacturing the preferred
result of a high-quality commodity or service that gratifies client requirements. A business
organization's operations area is manufacturing goods and services. Products are tangible
objects, but services are actions that deal with a mixture of time, place, system, or
psychological significance. Operations are internal tasks that must be completed to supply
goods or services to clients. Therefore, operations management can be viewed from an
organizational standpoint as the administration of the conversion processes that turn inputs
like labor and raw materials into outcomes in the type of finished products and activities. It
guarantees that goods fulfill client requirements and quality necessities (Olsen & Tomlin,
2019).
Importance of Operation Management
Nowadays, every firm recognizes operations management (OM) as little more than a
crucial functional department. Operations governance is no longer viewed as a department
that reports to the financial and advertising departments but as an equal. Businesses that don't
acknowledge its crucial role in their success will often lose money and diminish their market
share. Operations management's former reactive function, which focused primarily on cutting
costs, has been substituted with a more proactive one aiming to maximize the value
3
contributed to the company's products and services. Businesses now operate in a very
cutthroat market. Achieving and maintaining excellent quality while keeping costs in check
are some of the critical problems its executives are currently dealing with in this unstable
market. In addition, the business must efficiently collaborate with other departments to
achieve its objectives, function efficiently among vendors, and be user-friendly for
consumers. Technological advances and control mechanisms must also be integrated into
current processes (Lee & Tang, 2018). These problems are all linked together.
To succeed, OM must do all those tasks to the degree relevant in home and international
markets. Furthermore, it would need to spend money on extra capability that might not
always be used to its fullest. Following production, goods were packaged and kept at the
nearby distribution facility. People disposed of most of their previous, smaller injection
sculpting equipment when the company switched to producing higher-margin HFD goods.
People could employ massive, multi-cavity castings because we had larger machinery overall.
As a result, HFD made many items—or components—during each machine cycle, which
enhanced production. Additionally, it enabled humanity to employ sophisticated molds that
produced a high-quality end product while being bulky and more challenging to switch out
(Lee & Tang, 2018).
Q 2.
All business operations have one thing in common: they transform inputs such as
unprocessed materials, knowledge, cash, tools, and time into outputs. Operations are most
easily regarded as the core of an organisation, where the majority of direct work is carried
out. Operations at such a service-based company are frequently task-oriented and thus will
adhere to a predetermined process until the facilities is complete. On the other hand,
operations are far more critical in a manufacturing company since they follow the products
Your preview ends here
Eager to read complete document? Join bartleby learn and gain access to the full version
- Access to all documents
- Unlimited textbook solutions
- 24/7 expert homework help
4
from their inception to a conclusion before going on to a later point, which is frequently
distributed.
HFD's 4Vs profile
1.
Volume:
The amount of a product that needs to be manufactured to gratify market
demand. This denotes to the definite number of items or units produced. A large-
volume company frequently has specialized personnel, protocols, and tools in addition
to highly repeatable operations and goods. Given the prevalence of costly buildings
and machinery explicitly designed for high-volume production and can provide the
low unit pricing usually necessary to thrive in high-volume operations. As a result, the
company is anticipated to be capital-intensive. Since they cannot be verified for this
type of low-volume manufacturing, low-volume firm operations that manufacture a
few items or offer a modest number of services yearly are doubtful to contain such
expensive or specialized hardware, facilities, methods, or talents. Instead, they should
participate in factors other than prices, such as customization or rapid lead times
(Cappa et al., 2020).
2.
Variety
is the spectrum of goods and services that might be formed and made
available to clients. This V efforts on diversity. Industries that provide various
products or services can growth their income and profit prospective and reduce their
dependency upon only one or two consequences, which could push them out of
existence if the marketplace for those products or services declines or vanishes.
3.
Variation
is the degree to which demand shifts over time due to external factors.
Forecasting variance, meanwhile, is difficult for many reasons. For example, things
became entirely out of rhythm in all aspects of humanity when a significant
catastrophe like the Covid-19 outbreak struck the world. Most business processes are
made up of several versions that must be managed collectively instead of individually.
5
Most of these techniques rely on inputs from various causes and points. Little
courtesy has been paid to the initial idea and drafting of operational variation.
Managers need a wealth of knowledge and expertise to fill the gaps. Procedures that
don't follow a rigorous pattern in operational and production processes lead to quality
concerns (Ivanov et al., 2020).
4.
Visibility:
This word refers to the entire value chain of a company's activities. Clients
are required to utilize the corporation's products and services. In terms of visibility,
the service industry is more visible than the industry sector. Client satisfaction is
influenced by impressions of product excellence and attention to detail, and customers
of high-profile enterprises will have lower response tolerances. High visibility
businesses are forced to concentrate more on the client's demands, which raises unit
prices. Companies that operate in "high exposure" environments need to be much
better at handling clients and pay more attention to their looks and client interaction
abilities. Conversely, operations with less "visibility" can focus more on their secrecy
measures and are evaluated on the end prices, output quality, and punctuality of their
result (Ivanov et al., 2020).
Q 3.
Company operations are the regular tasks that businesses complete to increase their worth
and profits. It may be possible to enhance operations so that they generate enough revenue to
cover expenses and benefit the business's owners. Employees assist in accomplishing
business goals by doing certain duties like marketing, accounting, production, etc.
Recommendations
If CEO Tom Jameson asked me for advice for improving the company operations, I
recommend some significant ways to him, which are explained as follows:
6
1.
Record Every Procedure
Company operations are essentially the activities, and sequences of actions workers take to
produce the product for their company. For example, the steps required for a waitperson to
accept somebody's order might serve as an example of a procedure if the business is a
cafeteria. Workers should be aware of the procedures that relate to them because, in principle,
these operations are taught during staff training. Assure that each and every procedure is well
documented and always accessible to all workers to increase the effectiveness of these
procedures and to enable future learning simpler (Chang et al., 2019).
2.
Invest in Cutting-Edge Technology
When many companies use contemporary technology, relying on traditional business tools
will not help company operations. If anything, it adds significant obstacles to many corporate
operations. Individuals should thus make it a priority to invest in cutting-edge technologies.
Professionals may use various software and hardware innovations, from researching
accounting practice management solutions to getting sophisticated security gear. The
company benefits from increased productivity and safety thanks to this. Consequently, their
team's performance might increase without impacting its work schedule (Herman et al.,
2020).
3.
Support the Workforce
No matter what kind of company individuals run, it is critical that professionals focus on
the development of company staff. This makes company personnel more capable of
producing high-quality work while enabling them to be more effective in their daily
activities. This enhancement may be attained through specialized training, in-depth team
talks, and focused work activities. Real-time evaluation and inspiration may benefit from
investing in a performance monitoring system. These techniques may guarantee the
Your preview ends here
Eager to read complete document? Join bartleby learn and gain access to the full version
- Access to all documents
- Unlimited textbook solutions
- 24/7 expert homework help
7
company's growth, whether individuals use them immediately after learning to acquire new
personnel or after supervising the team for years.
4.
Contact Out Through Social Media
Professionals must evaluate their company's social media marketing to enhance
performance, given that practically all businesses today utilize social media as a powerful
tool to connect to new consumers. Engaging in platform-specific advertising, creating fresh
content, including updating company branding may all provide outstanding benefits. They
may also utilize social media control to manage several profiles more easily.
These actions
may have a remarkable impact on the company's reach and assist them in maximizing the
results of its advertising tactics. The company operations might be visibly improved with
raised audience interest and reaction to marketing activities. By following these measures,
professionals may significantly increase their company's production, reach, and effectiveness.
This enables company operations to make remarkable advancements across the board, setting
the company on a road of steady development (Herman et al., 2020).
Part 2 - Analysis and Reflection
Q 1.
Lean Six Sigma seems to be a managerial approach with team importance that proposes to
increase efficiency by reducing the wastage of resources and errors. It merges the lean
manufacturing/ business mindset with Six Sigma practices and skills. It seeks to stop wasting
material assets, time, skill, and labor while ensuring the quality of administrative and
manufacturing procedures. Some people think it's significant since, with it, businesses can
measurably and consistently improve their operations and financial performance. Businesses
may increase employee and customer involvement by effectively implementing key
processes. This may boost devotion both within and outside of a firm. Operations that have
8
been simplified and made quicker can provide an organization with more flexibility and
simplify it to take advantage of new opportunities. Additionally, they could lead to higher
revenue and sales, lower costs, and better business outcomes. Workers may gain new abilities
(including managing projects and other crucial talents), improve their chances of career
progression, and build solidarity by participating in a group project or company-wide
efficiency push. Companies save time, money, and labor by preventing errors instead of
having to identify and rectify them after the fact. Businesses save time, money, and work by
avoiding mistakes instead of having to determine and remedy them after the fact. The
company activities benefit all parties, including the corporation, clients, vendors, and workers
(Noskieviová & Moravec, 2022).
Amazon
Several of the world's most profitable companies have effectively incorporated elements of
Six Sigma into their operational strategies. Few industries, meanwhile, are as suitable for its
principles as retail, and sometimes even a handful of these companies carry out the operation
as thoroughly and well as Amazon. A situation made achievable partly by its significant usage
of Six Sigma across all activities, and the e-commerce titan quickly leads all those other
online retailers. Amazon provides such a brilliant example of Six Sigma that the corporation
would undoubtedly be a good source of motivation for the private group. The Lean approach
enhances the Six Sigma perspective, and Amazon has incorporated its main operational
priority into its everyday operations. The company, for instance, commits more staff to its
fulfillment and customer support centers than to its technology program to retain a high
degree of service.
Each work operation is also methodically planned for maximum effectiveness, and the
delivery date is utilized to choose the best mode of transportation for a particular product.
9
This method allows firms to make the most use of their assets and save costs, which helps
prevent the organization from developing too rapidly (Wang et al., 2022). It's a strategic
decision that only companies can incorporate the Six Sigma methodology into their company.
However, this strategy's tangible impact on retailers like Amazon makes a strong reason.
After all, keeping up with what their rivals are accomplishing is among the greatest ways to
assist any business in development. Amazon's continued domination of e-commerce calls for
deeper examination. There must be some crucial lessons individuals can implement in their
activities if Six Sigma could assist that organization in becoming its market leader. It seems
that company operations must constantly improve, given that its objective is to provide
improved and enhanced results (Wang et al., 2022).
The company's operations at Amazon are governed by the Kaizen concept, which
emphasizes maximizing efficiency to meet or exceed consumer expectations, particularly in
the fulfillment center. Its storage facilities process more than 35 purchases each second,
representing a level of service almost unheard of in the retail industry. Every delivery
company even has a manager whose job it is to oversee ongoing workflow improvements.
While your business may not have the same quantity as Amazon, users should pay close
attention to factors like order scheduling that directly affect the bottom line. To determine the
flaws or the proportion variation for the level of error specified, Six Sigma is a quantitative
and mathematical computation of the data. Any business should approach information as a
resource rather than a department's possession, particularly in an age where data is used
constantly (Lameijer et al., 2021). Analyzing data opened up new business opportunities for
Amazon. Jeff made careful to instill a data-driven environment from the frontline personnel
to the management when his company was still in its infancy. Amazon has always engaged
engineers to work on various data mining projects. This has likely allowed the company to
effectively maintain its more significant market position in the e-commerce sector for over 25
Your preview ends here
Eager to read complete document? Join bartleby learn and gain access to the full version
- Access to all documents
- Unlimited textbook solutions
- 24/7 expert homework help
10
years. Due to his foresight, data became the focal point of Bezos' organizational culture. He
set up the company's structure so all levels could access the data. It allowed the front lines to
make minor, regular decisions to raise consumer happiness. Amazon used its data technology
platform to study customer behavior, including the purchases people make, the things they
buy, and the demand cycles for products on the shelves. They could innovate and release new
products based on customer search information. Finding vendors that supplied top-notch
products at the most reasonable pricing and convenient delivery places was made more
accessible by data churning. With data available in this digital age, testing and analysis of
information got quicker and simpler. This encouraged continuous growth and learning to
increase profitability (Sordan et al., 2021).
Q 2.
Operations management has advanced through many periods, beginning with an emphasis
on cost reduction and ending with an emphasis on the quality era. The 1890s to 1920s, also
known as the "scientific organizational era," concentrated on lowering production expenses
as much as possible. OM during this time was mainly concerned with increasing productive
labor output. Businesses were primarily involved in finding ways to generate more with less,
using limited assets, and charging employees less. On the other hand, businesses were
beginning to understand the value of quality as they sought to preserve their market share
rather than focusing solely on profits and lowering prices. Companies pay more attention to
client satisfaction by eliminating flaws and improving the efficiency and longevity of their
goods. Since they recognized the connection between efficient cost and high quality could
increase businesses' competitiveness and help them hold their market share for an extended
without being affected by rivals (Scortex, 2020).
Reducing the Cost Era and Quality Era
11
Operations management has advanced through several periods, emphasizing cost
reduction and progressing with a focus on quality. Each of these periods had come
before it, and each succeeding one added to the knowledge gained by the ones that
came before it.
The concentration on streamlining operations during the cost-cutting period,
particularly in mass-production contexts, was marked by an increasing focus on
economy and effectiveness. The advent of the assembly plant, the most effective
method of manufacturing ever created at the time, during this age is not a coincidence.
The emphasis on cost-cutting was accompanied by a desire to keep growth stable and
consistent.
The emphasis on the quality era, which came after and was inspired by the emphasis
on cost-cutting, saw a change toward a strategy to operations management that was
more focused on the needs of the customer. This change featured a stronger focus on
staff empowerment to provide clients with greater service. In order for all facets of the
business activities to collaborate to provide superior results for clients, it also placed a
greater focus on collaboration across various divisions within a corporate organization
(Scortex, 2020).
Operations executives in the production industry have seen two different periods
when the emphasis has been on cutting costs and enhancing quality. Although each of
these periods had its method of approaching operations, each era also assisted in
developing the subsequent one.
During the age of cost-cutting, businesses concentrated on cutting expenses as much
as possible. Henry Ford's invention of the factory line, which made mass
manufacturing and far lower prices conceivable than had before been feasible, had a
significant influence on this time period. Specifically, businesses sought to create
12
more while utilizing fewer assets and paying employees less. This was the main focus
of their attention (Khan et al., 2021).
There is a big shift in perspective as we go towards the era of quality-focused
production. Businesses are now focused on creating items that would be both more
attractive to consumers and cheaper rather than only focusing on making goods
cheaper. This meant eliminating flaws and creating items that consumers would find
appealing and durable. With their concentration on producing high-quality items via
excellent innovation and workmanship, Japanese producers set the bar here.
The application of mass manufacturing concepts to achieve economies of scale was
introduced during the cost-cutting period of OM. Contrarily, in the era of quality as
defined by operations management, consumers took center stage in implementing
total quality management principles. For instance, computerized systems like MRP
controlled the period of reducing costs. Still, the era of quality control was seen as a
competing weapon to boost sales by providing high-quality products. The idea behind
the cost-cutting period, it might be said, was centered on using flexible production
systems and producing using computer programs. In contrast, the quality period was
primarily when the idea of quality as a distinct stage of the manufacturing process was
addressed (Khan et al., 2021).
Innovative effort and advocacy for the necessity to develop original product
advancement ideas in order to have the flexibility to satisfy rapidly shifting consumer
preferences and wants To adjust to the shortening product life cycle, business methods
must be recovered more quickly while production offices must be managed much
more efficiently. The main forces behind the new modifications in the present key
strategies are consumers who clearly emphasise their needs. They are the most notable
associations' partners. Additionally, society and the neighbourhood as a whole make
Your preview ends here
Eager to read complete document? Join bartleby learn and gain access to the full version
- Access to all documents
- Unlimited textbook solutions
- 24/7 expert homework help
13
up one of the best partner groups for organisations. This shifting partner centre
compels OM to rigorously assess the wider impact of operational decisions on the
environment and free society. Organizations must gradually demonstrate their eco-
friendliness if they want to maintain effective advertising in society.
Q 3.
a.
Capacity Planning
The quantity of production producers can produce in terms of products and services to
satisfy consumer requirements closely correlates with the industry's capability. The procedure
through which producers evaluate how many assets they will need to fulfill the requirement
for their goods or services is known as capacity planning. Capacity planning methods can
assist producers in establishing how much natural resources, machinery, labor, and facility
capital will be necessary to fulfill prospective product requirements. These strategies can
guide capital spending for raw resources, hardware, labor, and facility financing.
Absence of
capacity planning results in clients' requirements not being satisfied as soon as they might be,
which increases the risk of losing them to competitors. A strong capacity planning technique
aids the effective distribution of production materials. It implies that the operator's funds are
mismanaged and may be effectively used elsewhere, generating a profit. On the contrary side,
"low capacity" is the inability of a manufacturer to generate for a set amount of time in line
with a user's criteria (Choi et al., 2021).
Guaranteeing that there is room for potential expansion enhances the organization's
operations even more.
It also enables the company to prevent excess capacity and the
expenses that come with it, like idle assets and unproductive capability. All capacity planning
and OM techniques aim to determine the optimal amount of electricity required to fulfill
future needs. Forecasting upcoming demand is the first step in the capacity planning
14
procedure. After the projection, capacity may be scheduled following the anticipated demand.
The objective is to fulfill client demand with sufficient capacity while minimizing expenses.
Different firms will require more capacity relying on their processes, goods, and services.
OM's crucial capacity planning component must be customized to each company's
requirements. When done correctly, capacity planning may save organizations money by
ensuring they have the capabilities needed to satisfy future needs and avoiding the expenses
associated with over- or under-capacity (Teerasoponpong & Sopadang, 2021).
b.
Planning and Control
The managerial responsibilities of planning and control, sometimes referred to as
manufacturing planning and regulation, focus on determining two things: first, what the
market wants, and second, how a firm may best prepare for and fulfill those needs. Daily
operations need planning, including scheduling, dispatch verification, quality evaluation,
inventory supervision, and supply and material maintenance. Control ensures that the actions
are carried out as efficiently and cost-effectively as possible. Controls are put in place to
prepare businesses for modifications when they inevitably occur, whereas planning puts out
the objectives, purposes, and strategies for enterprises to meet customer expectations. In other
words, control ensures that companies may swiftly adapt and modify their operating
principles. Overall, scheduling and monitoring ensure that stock is maintained current, the
staff is scheduled correctly, output maintains up with the market, and the manufacturing line
runs like well-oiled gear (Oluyisola et al., 2021).
c.
Forecasting
Forecasting is the process of making predictions based on recent and previous data. Trend
evaluation is the approach that is used most frequently for this. To predict an interest-based
factor at a specific future period would be one example. Prediction is a comparable but more
15
general concept. Both terms might describe less formal judging techniques or statistical
approaches using time-periodic, cross-sectional, or continuous data. The words "prediction"
as well as "forecasting" are employed for more broad estimations, like the frequency of
flooding more than an extended period, whereas "forecast" with "forecasting" are
occasionally retained in the context of hydrology for predictions of values at particular future
intervals.
Using data from the past and current, forecasting aids in the prediction of future
commercial occurrences. By using accurate forecasting, companies can ensure adequate
supply and preparedness to meet the operation's requirements. Naturally, many risks are
associated with running a business, which is why predicting is done. The reliability of the
predicted data may be impacted if people presume anything without evidence (Fildes et al.,
2019).
In addition, as precise projections are necessary for benefits in product innovation, price,
and quickness to market, forecasting is crucial for maintaining excellent relations with
suppliers.
Underrating demand implies many consumers won't obtain the things they desire
because there isn't enough supply while overestimating demand results in more enormous
inventory and needless expenditures. The number of devoted clients in the company may
decline due to this issue. Lack of capacity can cause shortages that cost businesses,
consumers, and industry share. Demand projections are taken into account while hiring,
training, and terminating employees. To satisfy the need for human assets in perspective, it is
crucial to assess the quantity and quality of current and projected human resources that are
accessible both inside and outside the business. Analyzing and predicting the numerous
expenditures and administrative tasks associated with hiring more employees or cutting back
on staff will significantly impact the organization's operation (Fildes & Goodwin, 2020).
Your preview ends here
Eager to read complete document? Join bartleby learn and gain access to the full version
- Access to all documents
- Unlimited textbook solutions
- 24/7 expert homework help
16
17
References
Chang, Y.-T., Chen, H., Cheng, R. K., & Chi, W. (2019). The impact of internal audit
attributes on the effectiveness of internal control over operations and compliance.
Journal of Contemporary Accounting & Economics
,
15
(1), 1–19.
https://doi.org/10.1016/j.jcae.2018.11.002
Choi, T., Kumar, S., Yue, X., & Chan, H. (2021). Disruptive technologies and operations
management in the industry 4.0 era and beyond.
Production and Operations
Management
,
31
(1), 9–31. https://doi.org/10.1111/poms.13622
Fildes, R., & Goodwin, P. (2020). Stability in the inefficient use of forecasting systems: A
case study in a supply chain company.
International Journal of Forecasting
,
37
(2),
1031–1046. https://doi.org/10.1016/j.ijforecast.2020.11.004
Fildes, R., Ma, S., & Kolassa, S. (2019). Retail forecasting: Research and practice.
International Journal of Forecasting
,
38
(4), 1283–1318.
https://doi.org/10.1016/j.ijforecast.2019.06.004
Herman, L. E., Sulhaini, S., & Farida, N. (2020). Electronic customer relationship
management and company performance: exploring the product innovativeness
development.
Journal of Relationship Marketing
,
20
(1), 1–19.
https://doi.org/10.1080/15332667.2019.1688600
Khan, S. A. R., Razzaq, A., Yu, Z., & Miller, S. (2021). Industry 4.0 and circular economy
practices: A new era business strategies for environmental sustainability.
Business
Strategy and the Environment
,
30
(8), 4001–4014. https://doi.org/10.1002/bse.2853
Lameijer, B. A., Pereira, W., & Antony, J. (2021). The implementation of Lean Six Sigma for
operational excellence in digital emerging technology companies.
Journal of
Manufacturing Technology Management
,
32
(9), 260–284.
https://doi.org/10.1108/jmtm-09-2020-0373
18
Lee, H. L., & Tang, C. S. (2018). Socially and environmentally responsible value chain
innovations: new operations management research opportunities.
Management
Science
,
64
(3), 983–996. https://doi.org/10.1287/mnsc.2016.2682
Noskievičová, D., & Moravec, L. (2022). Using principles and selected tools of lean six
Sigma to improve sustainability: A case study.
Quality Engineering
,
34
(2), 1–13.
https://doi.org/10.1080/08982112.2021.2024230
Olsen, T. L., & Tomlin, B. (2019). Industry 4.0: opportunities and challenges for operations
management.
Manufacturing & Service Operations Management
,
22
(1).
https://doi.org/10.1287/msom.2019.0796
Oluyisola, O. E., Bhalla, S., Sgarbossa, F., & Strandhagen, J. O. (2021). Designing and
developing smart production planning and control systems in the industry 4.0 era: a
methodology and case study.
Journal of Intelligent Manufacturing
,
33
, 311–332.
https://doi.org/10.1007/s10845-021-01808-w
Scortex (Ed.). (2020, July 28).
Focus on quality: Improve profitability by maximizing
operational efficiency
. Scortex. https://scortex.io/focus-on-quality/
Sordan, J. E., Oprime, P. C., Pimenta, M. L., Silva, S. L. da, & González, M. O. A. (2021).
Contact points between Lean Six Sigma and Industry 4.0: a systematic review and
conceptual framework.
International Journal of Quality & Reliability Management
,
ahead-of-print
(ahead-of-print), 2155–2183. https://doi.org/10.1108/ijqrm-12-2020-
0396
Teerasoponpong, S., & Sopadang, A. (2021). A simulation-optimization approach for
adaptive manufacturing capacity planning in small and medium-sized enterprises.
Expert Systems with Applications
,
168
, 114451.
https://doi.org/10.1016/j.eswa.2020.114451
Your preview ends here
Eager to read complete document? Join bartleby learn and gain access to the full version
- Access to all documents
- Unlimited textbook solutions
- 24/7 expert homework help
19
Wang, F.-K., Rahardjo, B., & Rovira, P. R. (2022). Lean Six Sigma with value stream
mapping in industry 4.0 for human-centered workstation design.
Sustainability
,
14
(17), 11020. https://doi.org/10.3390/su141711020
Ivanov, D., Tang, C. S., Dolgui, A., Battini, D., & Das, A. (2020). Researchers' perspectives
on Industry 4.0: multi-disciplinary analysis and opportunities for operations
management.
International Journal of Production Research
,
59
(7), 1–24.
https://doi.org/10.1080/00207543.2020.1798035
Cappa, F., Oriani, R., Peruffo, E., & McCarthy, I. (2020). Big Data for creating and capturing
value in the digitalized environment: unpacking the effects of volume, variety, and
veracity on firm performance.
Journal of Product Innovation Management
,
38
(1), 49–
67. https://doi.org/10.1111/jpim.12545
Related Documents
Recommended textbooks for you
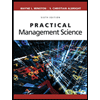
Practical Management Science
Operations Management
ISBN:9781337406659
Author:WINSTON, Wayne L.
Publisher:Cengage,
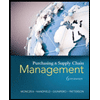
Purchasing and Supply Chain Management
Operations Management
ISBN:9781285869681
Author:Robert M. Monczka, Robert B. Handfield, Larry C. Giunipero, James L. Patterson
Publisher:Cengage Learning
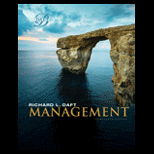
Management, Loose-Leaf Version
Management
ISBN:9781305969308
Author:Richard L. Daft
Publisher:South-Western College Pub
Recommended textbooks for you
- Practical Management ScienceOperations ManagementISBN:9781337406659Author:WINSTON, Wayne L.Publisher:Cengage,Purchasing and Supply Chain ManagementOperations ManagementISBN:9781285869681Author:Robert M. Monczka, Robert B. Handfield, Larry C. Giunipero, James L. PattersonPublisher:Cengage LearningManagement, Loose-Leaf VersionManagementISBN:9781305969308Author:Richard L. DaftPublisher:South-Western College Pub
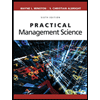
Practical Management Science
Operations Management
ISBN:9781337406659
Author:WINSTON, Wayne L.
Publisher:Cengage,
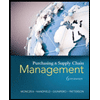
Purchasing and Supply Chain Management
Operations Management
ISBN:9781285869681
Author:Robert M. Monczka, Robert B. Handfield, Larry C. Giunipero, James L. Patterson
Publisher:Cengage Learning
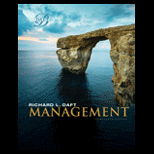
Management, Loose-Leaf Version
Management
ISBN:9781305969308
Author:Richard L. Daft
Publisher:South-Western College Pub