The factors affecting electroplating
.docx
keyboard_arrow_up
School
Harvard University *
*We aren’t endorsed by this school
Course
407
Subject
Chemistry
Date
Nov 24, 2024
Type
docx
Pages
19
Uploaded by AdmiralAtomJackal40
Your preview ends here
Eager to read complete document? Join bartleby learn and gain access to the full version
- Access to all documents
- Unlimited textbook solutions
- 24/7 expert homework help
Recommended textbooks for you
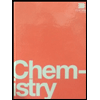
Chemistry by OpenStax (2015-05-04)
Chemistry
ISBN:9781938168390
Author:Klaus Theopold, Richard H Langley, Paul Flowers, William R. Robinson, Mark Blaser
Publisher:OpenStax
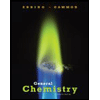
General Chemistry - Standalone book (MindTap Cour...
Chemistry
ISBN:9781305580343
Author:Steven D. Gammon, Ebbing, Darrell Ebbing, Steven D., Darrell; Gammon, Darrell Ebbing; Steven D. Gammon, Darrell D.; Gammon, Ebbing; Steven D. Gammon; Darrell
Publisher:Cengage Learning
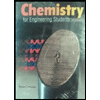
Chemistry for Engineering Students
Chemistry
ISBN:9781337398909
Author:Lawrence S. Brown, Tom Holme
Publisher:Cengage Learning
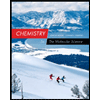
Chemistry: The Molecular Science
Chemistry
ISBN:9781285199047
Author:John W. Moore, Conrad L. Stanitski
Publisher:Cengage Learning
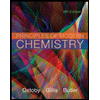
Principles of Modern Chemistry
Chemistry
ISBN:9781305079113
Author:David W. Oxtoby, H. Pat Gillis, Laurie J. Butler
Publisher:Cengage Learning
Recommended textbooks for you
- Chemistry by OpenStax (2015-05-04)ChemistryISBN:9781938168390Author:Klaus Theopold, Richard H Langley, Paul Flowers, William R. Robinson, Mark BlaserPublisher:OpenStaxGeneral Chemistry - Standalone book (MindTap Cour...ChemistryISBN:9781305580343Author:Steven D. Gammon, Ebbing, Darrell Ebbing, Steven D., Darrell; Gammon, Darrell Ebbing; Steven D. Gammon, Darrell D.; Gammon, Ebbing; Steven D. Gammon; DarrellPublisher:Cengage Learning
- Chemistry for Engineering StudentsChemistryISBN:9781337398909Author:Lawrence S. Brown, Tom HolmePublisher:Cengage LearningChemistry: The Molecular ScienceChemistryISBN:9781285199047Author:John W. Moore, Conrad L. StanitskiPublisher:Cengage LearningPrinciples of Modern ChemistryChemistryISBN:9781305079113Author:David W. Oxtoby, H. Pat Gillis, Laurie J. ButlerPublisher:Cengage Learning
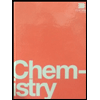
Chemistry by OpenStax (2015-05-04)
Chemistry
ISBN:9781938168390
Author:Klaus Theopold, Richard H Langley, Paul Flowers, William R. Robinson, Mark Blaser
Publisher:OpenStax
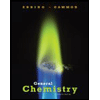
General Chemistry - Standalone book (MindTap Cour...
Chemistry
ISBN:9781305580343
Author:Steven D. Gammon, Ebbing, Darrell Ebbing, Steven D., Darrell; Gammon, Darrell Ebbing; Steven D. Gammon, Darrell D.; Gammon, Ebbing; Steven D. Gammon; Darrell
Publisher:Cengage Learning
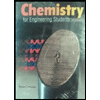
Chemistry for Engineering Students
Chemistry
ISBN:9781337398909
Author:Lawrence S. Brown, Tom Holme
Publisher:Cengage Learning
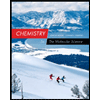
Chemistry: The Molecular Science
Chemistry
ISBN:9781285199047
Author:John W. Moore, Conrad L. Stanitski
Publisher:Cengage Learning
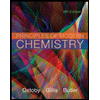
Principles of Modern Chemistry
Chemistry
ISBN:9781305079113
Author:David W. Oxtoby, H. Pat Gillis, Laurie J. Butler
Publisher:Cengage Learning