A solid 57-mm-diameter cold-rolled brass [G = 42.3 GPa) shaft that is 1.35 m long extends through and is completely bonded to a hollow aluminum [G= 22.4 GPa] tube. Aluminum tube (1) has an outside diameter of 79 mm, an inside diameter of 57 mm, and a length of 0.84 m. Both the brass shaft and the aluminum tube are securely attached to the wall support at A. Assume L₁-L₂=0.84 m, L3= 0.51 m, TB = 19 kN-m, and Tc= 8 kN-m. When the two torques shown are applied to the composite shaft, determine: (a) the maximum shear stress magnitude 7₁ in aluminum tube (1). (b) the maximum shear stress magnitude 7₂ in brass shaft segment (2). (c) the maximum shear stress magnitude 73 in brass shaft segment (3). (d) the rotation angle of joint B. (e) the rotation angle Pc of joint C. (1) B TB Tc X
A solid 57-mm-diameter cold-rolled brass [G = 42.3 GPa) shaft that is 1.35 m long extends through and is completely bonded to a hollow aluminum [G= 22.4 GPa] tube. Aluminum tube (1) has an outside diameter of 79 mm, an inside diameter of 57 mm, and a length of 0.84 m. Both the brass shaft and the aluminum tube are securely attached to the wall support at A. Assume L₁-L₂=0.84 m, L3= 0.51 m, TB = 19 kN-m, and Tc= 8 kN-m. When the two torques shown are applied to the composite shaft, determine: (a) the maximum shear stress magnitude 7₁ in aluminum tube (1). (b) the maximum shear stress magnitude 7₂ in brass shaft segment (2). (c) the maximum shear stress magnitude 73 in brass shaft segment (3). (d) the rotation angle of joint B. (e) the rotation angle Pc of joint C. (1) B TB Tc X
Mechanics of Materials (MindTap Course List)
9th Edition
ISBN:9781337093347
Author:Barry J. Goodno, James M. Gere
Publisher:Barry J. Goodno, James M. Gere
Chapter2: Axially Loaded Members
Section: Chapter Questions
Problem 2.2.17P: A hollow, circular, cast-iron pipe (Ec =12,000 ksi) supports a brass rod (Ec= 14,000 ksi} and weight...
Related questions
Question
![A solid 57-mm-diameter cold-rolled brass [G = 42.3 GPa] shaft that is 1.35 m long extends through and is completely bonded to a
hollow aluminum [G = 22.4 GPa] tube. Aluminum tube (1) has an outside diameter of 79 mm, an inside diameter of 57 mm, and a length
of 0.84 m. Both the brass shaft and the aluminum tube are securely attached to the wall support at A. Assume L₁-L₂ = 0.84 m, L3= 0.51
m, TB = 19 kN-m, and Tc = 8 kN-m. When the two torques shown are applied to the composite shaft, determine:
(a) the maximum shear stress magnitude t₁ in aluminum tube (1).
(b) the maximum shear stress magnitude 72 in brass shaft segment (2).
(c) the maximum shear stress magnitude t3 in brass shaft segment (3).
(d) the rotation angle B of joint B.
(e) the rotation angle c of joint C.
(1)
L3
B
TB
3
Tc](/v2/_next/image?url=https%3A%2F%2Fcontent.bartleby.com%2Fqna-images%2Fquestion%2F59e87c9f-d488-44e1-8f93-8d7d44a92f40%2F4f892453-6026-4cd0-b97c-cd0fa26a63e5%2Fie8ihbu_processed.png&w=3840&q=75)
Transcribed Image Text:A solid 57-mm-diameter cold-rolled brass [G = 42.3 GPa] shaft that is 1.35 m long extends through and is completely bonded to a
hollow aluminum [G = 22.4 GPa] tube. Aluminum tube (1) has an outside diameter of 79 mm, an inside diameter of 57 mm, and a length
of 0.84 m. Both the brass shaft and the aluminum tube are securely attached to the wall support at A. Assume L₁-L₂ = 0.84 m, L3= 0.51
m, TB = 19 kN-m, and Tc = 8 kN-m. When the two torques shown are applied to the composite shaft, determine:
(a) the maximum shear stress magnitude t₁ in aluminum tube (1).
(b) the maximum shear stress magnitude 72 in brass shaft segment (2).
(c) the maximum shear stress magnitude t3 in brass shaft segment (3).
(d) the rotation angle B of joint B.
(e) the rotation angle c of joint C.
(1)
L3
B
TB
3
Tc
Expert Solution

This question has been solved!
Explore an expertly crafted, step-by-step solution for a thorough understanding of key concepts.
Step by step
Solved in 4 steps with 2 images

Follow-up Questions
Read through expert solutions to related follow-up questions below.
Follow-up Question
The rotation angle of the joints is still needed.
Solution
Knowledge Booster
Learn more about
Need a deep-dive on the concept behind this application? Look no further. Learn more about this topic, mechanical-engineering and related others by exploring similar questions and additional content below.Recommended textbooks for you
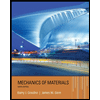
Mechanics of Materials (MindTap Course List)
Mechanical Engineering
ISBN:
9781337093347
Author:
Barry J. Goodno, James M. Gere
Publisher:
Cengage Learning
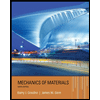
Mechanics of Materials (MindTap Course List)
Mechanical Engineering
ISBN:
9781337093347
Author:
Barry J. Goodno, James M. Gere
Publisher:
Cengage Learning