Q1. Describe the following modes of failure associated with gear teeth, indicating their causes and how they might be prevented in practice: (i) tooth breakage (bending failure); and (ii) surface damage of teeth (pitting).
Q1. Describe the following modes of failure associated with gear teeth, indicating their causes and how they might be prevented in practice: (i) tooth breakage (bending failure); and (ii) surface damage of teeth (pitting).
Elements Of Electromagnetics
7th Edition
ISBN:9780190698614
Author:Sadiku, Matthew N. O.
Publisher:Sadiku, Matthew N. O.
ChapterMA: Math Assessment
Section: Chapter Questions
Problem 1.1MA
Related questions
Question
Please summarise the answers for this question for i and ii
as it looks too long

Transcribed Image Text:Q1. Describe the following modes of failure associated with gear
teeth, indicating their causes and how they might be prevented in
practice:
(i) tooth breakage (bending failure);
and
(ii) surface damage of teeth (pitting).
i. Bending failure occurs as a result of bending stresses in the tooth which are
greatest at the root. Because of the cyclic loading this is a fatigue problem which
manifests itself by cracks propagating across the tooth and the facewidth of the
gear itself. This results in partial or total removal of a tooth.
ii.
The situation maybe made worse by the use of unsubstantial rims or the pressure
of stress concentrations arising from pits may move the critical stress away from
the fillet.
Materials with a high fatigue resistance need to be used-surface hardened steels
are best in this sense,
Therefore, offer little improvement in load distribution.
Residual stresses maybe beneficial - compressive stresses due to Carburising or
shot peeing.
In general (bending strength) a UTS with Carburising steel showing a marked
improvement over other materials.
The repeated application of Hertzian stresses to gear surfaces results in small
fatigue cracks at or near the surface. These extend until lumps fall out leaving
craters. These usually occur on the dedendum surfaces of teeth.
This is also a fatigue problem, but the associated knee point is much
higher ~108 or 10⁹ cycles.
The craters reduce the load bearing surface, break the lubricant film, and
constitute a stress concentration from which total tooth breakage could initiate.
There is evidence that pitting is initiated by stresses associated with asperity
contacts. Pitting can be avoided by ensuring that the oil film thickness is
substantially greater than the total surface roughness.
Expert Solution

This question has been solved!
Explore an expertly crafted, step-by-step solution for a thorough understanding of key concepts.
Step by step
Solved in 5 steps with 9 images

Knowledge Booster
Learn more about
Need a deep-dive on the concept behind this application? Look no further. Learn more about this topic, mechanical-engineering and related others by exploring similar questions and additional content below.Recommended textbooks for you
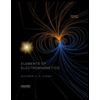
Elements Of Electromagnetics
Mechanical Engineering
ISBN:
9780190698614
Author:
Sadiku, Matthew N. O.
Publisher:
Oxford University Press
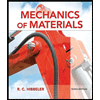
Mechanics of Materials (10th Edition)
Mechanical Engineering
ISBN:
9780134319650
Author:
Russell C. Hibbeler
Publisher:
PEARSON
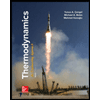
Thermodynamics: An Engineering Approach
Mechanical Engineering
ISBN:
9781259822674
Author:
Yunus A. Cengel Dr., Michael A. Boles
Publisher:
McGraw-Hill Education
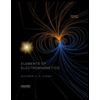
Elements Of Electromagnetics
Mechanical Engineering
ISBN:
9780190698614
Author:
Sadiku, Matthew N. O.
Publisher:
Oxford University Press
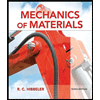
Mechanics of Materials (10th Edition)
Mechanical Engineering
ISBN:
9780134319650
Author:
Russell C. Hibbeler
Publisher:
PEARSON
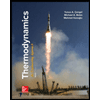
Thermodynamics: An Engineering Approach
Mechanical Engineering
ISBN:
9781259822674
Author:
Yunus A. Cengel Dr., Michael A. Boles
Publisher:
McGraw-Hill Education
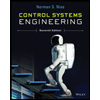
Control Systems Engineering
Mechanical Engineering
ISBN:
9781118170519
Author:
Norman S. Nise
Publisher:
WILEY
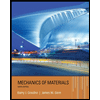
Mechanics of Materials (MindTap Course List)
Mechanical Engineering
ISBN:
9781337093347
Author:
Barry J. Goodno, James M. Gere
Publisher:
Cengage Learning
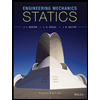
Engineering Mechanics: Statics
Mechanical Engineering
ISBN:
9781118807330
Author:
James L. Meriam, L. G. Kraige, J. N. Bolton
Publisher:
WILEY