Law Wizard Inc. (LWI) is a manufacturer of a range of walk-behind gasoline lawnmowers, which it markets to garden centers and home improvement centers. LWI employs a batch production process whose inventory management, production planning, and accounting procedures consist of a combination of manual activities supported by stand-alone (non-networked) PC technology. The company is experiencing production delays and cost overruns. Its CEO has hired your firm to review its procedures and make recommendations for improving its operations. The batch production process is initiated by receipt of individual customer orders, which are grouped together in batches for manufacturing. The production planning and control clerk enters the orders into the digital production schedule from his department PC and prints two hard-copy work orders. He sends one of these to cost accounting and the other to the production department. The production department supervisor enters the work order into a PC application. The system automatically creates an open work order record and prints the hard-copy move tickets and materials requisitions. The supervisor distributes the move tickets and two copies of the purchase requisitions to each work center involved in the production process. Work center employees exchange the material requisitions for assembly parts and other materials needed to complete the batch. If additional parts or materials are needed beyond the standard quantity, the supervisor issues additional material requisitions. As the production is completed in each work center, employees record their labor time for each batch on hard-copy job cards, which they send to cost accounting along with the move ticket. Finally, upon completion of the batch, the supervisor closes the open work order file. The storekeeping clerk files one copy of the material requisition in the department and updates the raw materials inventory file from the computer in his office. The manager then sends the second copy of the material requisition to cost accounting. At the end of the day, the manager prepares a hard-copy journal voucher and sends it to the general ledger department. The cost accounting clerk receives the work order and sets up a WIP account for the batch. Throughout the production period, the clerk also receives move tickets, job tickets, and materials requisitions, which she uses to post to WIP. At the end of each day, the cost accounting clerk prepares a hard-copy journal voucher, which she sends to general ledger department. The journal voucher reflects the total value of WIP and transfers to finished good inventory. The general ledger clerk receives the journal vouchers, posts to the appropriate GL accounts, and files the journal vouchers in the department. Required Create a system flowchart of the existing system. What risks exist in the system as it is currently designed? Describe the changes needed to reduce the risks.
Law Wizard Inc. (LWI) is a manufacturer of a range of walk-behind gasoline lawnmowers, which it markets to garden centers and home improvement centers.
LWI employs a batch production process whose inventory management, production planning, and accounting procedures consist of a combination of manual activities supported by stand-alone (non-networked) PC technology. The company is experiencing production delays and cost overruns. Its CEO has hired your firm to review its procedures and make recommendations for improving its operations.
The batch production process is initiated by receipt of individual customer orders, which are grouped together in batches for manufacturing. The production planning and control clerk enters the orders into the digital production schedule from his department PC and prints two hard-copy work orders. He sends one of these to cost accounting and the other to the production department.
The production department supervisor enters the work order into a PC application. The system automatically creates an open work order record and prints the hard-copy move tickets and materials requisitions.
The supervisor distributes the move tickets and two copies of the purchase requisitions to each work center involved in the production process. Work center employees exchange the material requisitions for assembly parts and other materials needed to complete the batch. If additional parts or materials are needed beyond the standard quantity, the supervisor issues additional material requisitions. As the production is completed in each work center, employees record their labor time for each batch on hard-copy job cards, which they send to cost accounting along with the move ticket. Finally, upon completion of the batch, the supervisor closes the open work order file.
The storekeeping clerk files one copy of the material requisition in the department and updates the raw materials inventory file from the computer in his office. The manager then sends the second copy of the material requisition to cost accounting. At the end of the day, the manager prepares a hard-copy journal voucher and sends it to the general ledger department.
The cost accounting clerk receives the work order and sets up a WIP account for the batch. Throughout the production period, the clerk also receives move tickets, job tickets, and materials requisitions, which she uses to post to WIP. At the end of each day, the cost accounting clerk prepares a hard-copy journal voucher, which she sends to general ledger department. The journal voucher reflects the total value of WIP and transfers to finished good inventory.
The general ledger clerk receives the journal vouchers, posts to the appropriate GL accounts, and files the journal vouchers in the department.
Required
-
Create a system flowchart of the existing system.
-
What risks exist in the system as it is currently designed?
-
Describe the changes needed to reduce the risks.

Trending now
This is a popular solution!
Step by step
Solved in 4 steps with 1 images

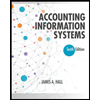
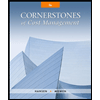
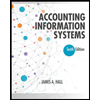
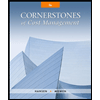