Day 1/Chapter 1 Case Study: Guided Practice WILLIAMS MACHINE TOOL COMPANY For 85 years, the Williams Machine Tool Company had provided high-quality products to its clients, becoming the third largest U.S.-based machine tool company by 1990. The company was highly profitable and had an extremely low employee turnover rate. Pay and benefits were excellent. Between 1980 and 1990, the company's profits soared to record levels. The company's success was due to one product line of standard manufacturing machine tools. Williams spent most of its time and effort looking for ways to improve its bread-and-butter product line rather than to develop new products. The product line was so successful that companies were willing to modify their production lines around these machine tools rather than asking Williams for major modifications to the machine tools. By 1990, Williams Company was extremely complacent, expecting this phenomenal success with one product line to continue for 20 to 25 more years. The recession of the early 1990s forced management to realign their thinking. Cutbacks in production had decreased the demand for the standard machine tools. More and more customers were asking for either major modifications to the standard machine tools or a completely new product design. The marketplace was changing and senior management recognized that a new strategic focus was necessary. However, lower-level management and the work force, especially engineering. were strongly resisting a change. The employees, many of them with over 20 years of employment at Williams Company, refused to recognize the need for this change in the belief that the glory days of yore would return at the end of the recession. By 1995, the recession had been over for at least two years yet Williams Company had no new product lines. Revenue was down, sales for the standard product (with and without modifications) were decreasing, and the employees were still resisting change. Layoffs were imminent. In 1996, the company was sold to Crock Engineering. Crock had an experienced machine tool division of its own and understood the machine tool business. Williams Company was allowed to operate as a separate entity from 1995 to 1996. By 1996, red ink had appeared on the Williams Company balance sheet. Crock replaced all of the Williams senior managers with its own personnel. Crock then announced to all employees that Williams would become a specialty machine tool manufacturer and that the "good old days" would never return Customer demand for specialty products had increased threefold in just the last twelve months alone. Crock made it clear that employees who would not support this new direction would be replaced. The new senior management at Williams Company recognized that 85 years of traditional management had come to an end for a company now committed to specialty products. The company culture was about to change, spearheaded by project management, concurrent engineering, and total quality management. Senior management's commitment to product management was apparent by the time and money spent in educating the employees. Unfortunately, the seasoned 20-year-plus veterans still would not support the new culture. Recognizing the problems, management provided continuous and
Day 1/Chapter 1 Case Study: Guided Practice WILLIAMS MACHINE TOOL COMPANY For 85 years, the Williams Machine Tool Company had provided high-quality products to its clients, becoming the third largest U.S.-based machine tool company by 1990. The company was highly profitable and had an extremely low employee turnover rate. Pay and benefits were excellent. Between 1980 and 1990, the company's profits soared to record levels. The company's success was due to one product line of standard manufacturing machine tools. Williams spent most of its time and effort looking for ways to improve its bread-and-butter product line rather than to develop new products. The product line was so successful that companies were willing to modify their production lines around these machine tools rather than asking Williams for major modifications to the machine tools. By 1990, Williams Company was extremely complacent, expecting this phenomenal success with one product line to continue for 20 to 25 more years. The recession of the early 1990s forced management to realign their thinking. Cutbacks in production had decreased the demand for the standard machine tools. More and more customers were asking for either major modifications to the standard machine tools or a completely new product design. The marketplace was changing and senior management recognized that a new strategic focus was necessary. However, lower-level management and the work force, especially engineering. were strongly resisting a change. The employees, many of them with over 20 years of employment at Williams Company, refused to recognize the need for this change in the belief that the glory days of yore would return at the end of the recession. By 1995, the recession had been over for at least two years yet Williams Company had no new product lines. Revenue was down, sales for the standard product (with and without modifications) were decreasing, and the employees were still resisting change. Layoffs were imminent. In 1996, the company was sold to Crock Engineering. Crock had an experienced machine tool division of its own and understood the machine tool business. Williams Company was allowed to operate as a separate entity from 1995 to 1996. By 1996, red ink had appeared on the Williams Company balance sheet. Crock replaced all of the Williams senior managers with its own personnel. Crock then announced to all employees that Williams would become a specialty machine tool manufacturer and that the "good old days" would never return Customer demand for specialty products had increased threefold in just the last twelve months alone. Crock made it clear that employees who would not support this new direction would be replaced. The new senior management at Williams Company recognized that 85 years of traditional management had come to an end for a company now committed to specialty products. The company culture was about to change, spearheaded by project management, concurrent engineering, and total quality management. Senior management's commitment to product management was apparent by the time and money spent in educating the employees. Unfortunately, the seasoned 20-year-plus veterans still would not support the new culture. Recognizing the problems, management provided continuous and
Practical Management Science
6th Edition
ISBN:9781337406659
Author:WINSTON, Wayne L.
Publisher:WINSTON, Wayne L.
Chapter2: Introduction To Spreadsheet Modeling
Section: Chapter Questions
Problem 20P: Julie James is opening a lemonade stand. She believes the fixed cost per week of running the stand...
Related questions
Question

Transcribed Image Text:Day 1/Chapter 1 Case Study: Guided Practice
WILLIAMS MACHINE TOOL COMPANY
For 85 years, the Williams Machine Tool Company had provided high-quality products to its
clients, becoming the third largest U.S.-based machine tool company by 1990. The company was
highly profitable and had an extremely low employee turnover rate. Pay and benefits were
excellent.
Between 1980 and 1990, the company's profits soared to record levels. The company's success
was due to one product line of standard manufacturing machine tools. Williams spent most of its
time and effort looking for ways to improve its bread-and-butter product line rather than to
develop new products. The product line was so successful that companies were willing to modify
their production lines around these machine tools rather than asking Williams for major
modifications to the machine tools.
By 1990, Williams Company was extremely complacent, expecting this phenomenal success
with one product line to continue for 20 to 25 more years. The recession of the early 1990s
forced management to realign their thinking. Cutbacks in production had decreased the demand
for the standard machine tools. More and more customers were asking for either major
modifications to the standard machine tools or a completely new product design.
The marketplace was changing and senior management recognized that a new strategic focus
was necessary. However, lower-level management and the work force, especially engineering.
were strongly resisting a change. The employees, many of them with over 20 years of
employment at Williams Company, refused to recognize the need for this change in the belief
that the glory days of yore would return at the end of the recession.
By 1995, the recession had been over for at least two years yet Williams Company had no new
product lines. Revenue was down, sales for the standard product (with and without
modifications) were decreasing, and the employees were still resisting change. Layoffs were
imminent.
In 1996, the company was sold to Crock Engineering. Crock had an experienced machine tool
division of its own and understood the machine tool business. Williams Company was allowed to
operate as a separate entity from 1995 to 1996. By 1996, red ink had appeared on the Williams
Company balance sheet. Crock replaced all of the Williams senior managers with its own
personnel. Crock then announced to all employees that Williams would become a specialty
machine tool manufacturer and that the "good old days" would never
for specialty products had increased threefold in just the last twelve months alone. Crock made it
clear that employees who would not support this new direction would be replaced.
Customer demand
The new senior management at Williams Company recognized that 85 years of traditional
management had come to an end for a company now committed to specialty products. The
company culture was about to change, spearheaded by project management, concurrent
engineering, and total quality management.
Senior management's commitment to product management was apparent by the time and money
spent in educating the employees. Unfortunately, the seasoned 20-year-plus veterans still would
not support the new culture. Recognizing the problems, management provided continuous and

Transcribed Image Text:visible support for project management in addition to hiing a project management consultant to
work with the people. The consultant worked with Williams from 1996 to 2001.
From 1996 to 2001, the Williams Division of Crock Engineering experienced losses in 24
consecutive quarters. The quarter ending March 31, 2002, was the first profitable quarter in over
six years. Much of the credit was given to the performance and maturity of the project
management system. In May 2002, the Williams Division was sold. More than 80% of the
employees lost their jobs when the company was relocated over 1,500 miles away.
QUESTIONS
1. Why was it so difficult to change the culture of the company?
2 What could have been done differently to accelerate the change?
Expert Solution

This question has been solved!
Explore an expertly crafted, step-by-step solution for a thorough understanding of key concepts.
This is a popular solution!
Trending now
This is a popular solution!
Step by step
Solved in 2 steps

Recommended textbooks for you
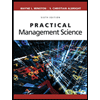
Practical Management Science
Operations Management
ISBN:
9781337406659
Author:
WINSTON, Wayne L.
Publisher:
Cengage,
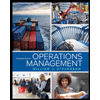
Operations Management
Operations Management
ISBN:
9781259667473
Author:
William J Stevenson
Publisher:
McGraw-Hill Education
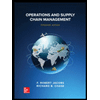
Operations and Supply Chain Management (Mcgraw-hi…
Operations Management
ISBN:
9781259666100
Author:
F. Robert Jacobs, Richard B Chase
Publisher:
McGraw-Hill Education
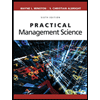
Practical Management Science
Operations Management
ISBN:
9781337406659
Author:
WINSTON, Wayne L.
Publisher:
Cengage,
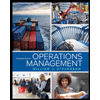
Operations Management
Operations Management
ISBN:
9781259667473
Author:
William J Stevenson
Publisher:
McGraw-Hill Education
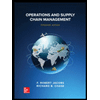
Operations and Supply Chain Management (Mcgraw-hi…
Operations Management
ISBN:
9781259666100
Author:
F. Robert Jacobs, Richard B Chase
Publisher:
McGraw-Hill Education
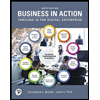
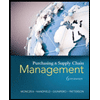
Purchasing and Supply Chain Management
Operations Management
ISBN:
9781285869681
Author:
Robert M. Monczka, Robert B. Handfield, Larry C. Giunipero, James L. Patterson
Publisher:
Cengage Learning
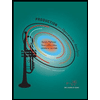
Production and Operations Analysis, Seventh Editi…
Operations Management
ISBN:
9781478623069
Author:
Steven Nahmias, Tava Lennon Olsen
Publisher:
Waveland Press, Inc.