A welded tension member is consisting of two channels placed 400mm back to back with flanges turned out. Select a channel for factored tensile of 4RKN using A36 steel and AISC specifications. The member is to be 15m long.
A welded tension member is consisting of two channels placed 400mm back to back with flanges turned out. Select a channel for factored tensile of 4RKN using A36 steel and AISC specifications. The member is to be 15m long.
Chapter2: Loads On Structures
Section: Chapter Questions
Problem 1P
Related questions
Question
Instructions:-
Write down each step clearly in calculation suggestion what you are doing.( you need to tell why you selected particular value of
ø (phi) and U). What and why you are calculating certain step
Consider R= 433.5
PROBLEM
A welded tension member is consisting of two channels placed 400mm back to back with flanges turned out. Select a channel for factored tensile of 4RKN using A36 steel and AISC specifications.
The member is to be 15m long.
PLASE USE THE EXAMPLE AS GUIDE OF ALL STEPS AND FORMULAS TO BE USE

Transcribed Image Text:52
STEEL STRUCTURES
SIDDIQI Z. A.
DESIGN OF TENSION MEMBERS $3
CHAPTER 2:
Solution:
Approximate r, and r,: (using Design Aids)
P, - 450 kN
T,= 840 kN
(1 +0.015 L) P.
r,= 0.36 h = 0.36(152) - 55 mm
r,-0.60 b - 0.60(300 – 2x51) - 118.8 mm
- (1.54) (450)
- 693 kN
T, > (1 +0.015 L) P.
Exact r, & r, (preferable and a must for final trial):
152
Referring to Figure 2.17,
r, = 56.4 mm as for a single section
I, =2 x 36.0 x10 + 2 x 1990 (150 - S1 + 12.7)
- 5038 x 10' mm'
Design first as a tension member and then check for P. (Case 3).
For welded connections,
300
5038 x 10
- 112.5 mm
I, x1000
Areg
840x1000
2x 1990
Figure 2.17. Built-Up Section Made
By Two Channels.
= 3733 mm
0.9F,
0.9x250
3733
Areg for one channel =
= 1867 mm
Pain 56.4 mm
%3D
bain - 50 mn for welded connections
6x 1000
Li Tmin.
106.4 < 200
(OK)
564
Options available:
1. C 150 x 15.6
2. МС 310 х 15.8
Design of Lacing: This part can be completed after discussion on the design of compression
members.
e.g
Trial section: 2C, 150 x 15.6 (Figure 2.16)
A -1990 mm?
d =152mm ; by=5Imm
I = 633 x 10ʻ man
I, -36.0 x 10' mm
- 12.7 mn
, - 56.4 mm ; r,-13.4 mm
Check For Compressive Strength:
** x 200,000
(106.4)*
F.
174.36 kN
Figure 2.16. Location of Centroid
for a Channel Section.
(KL./r)
> 0.44 F,
- 110 kN
(Inelastic buckling)
Check for bte
4F -
F, = 0.9x p.658 * 250
Both d and by > buin
(OK)
123.47 MPa
Capacity Check:
123.47 х 2х 1990/1000
AT,
49141 kN
P.
(OK)
0.9 F, Aal
=0.9 x 250 x (2 x 1990) / 1000
AT. - 0.75 F,UA.
895.5 kN > T. (OK)
Loading cycles are assumed less than 20,000
= 0.75 x 400 x 0,85 x (2x1990y1000 - 1014.9 kN > T,
(OK)
Assume U-0.85 from design aids and later check by using the detailed formula.
Design Connections
Expert Solution

This question has been solved!
Explore an expertly crafted, step-by-step solution for a thorough understanding of key concepts.
This is a popular solution!
Trending now
This is a popular solution!
Step by step
Solved in 3 steps

Knowledge Booster
Learn more about
Need a deep-dive on the concept behind this application? Look no further. Learn more about this topic, civil-engineering and related others by exploring similar questions and additional content below.Recommended textbooks for you
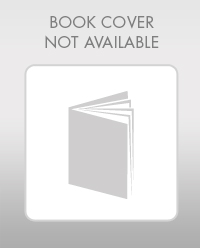
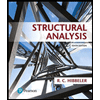
Structural Analysis (10th Edition)
Civil Engineering
ISBN:
9780134610672
Author:
Russell C. Hibbeler
Publisher:
PEARSON
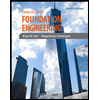
Principles of Foundation Engineering (MindTap Cou…
Civil Engineering
ISBN:
9781337705028
Author:
Braja M. Das, Nagaratnam Sivakugan
Publisher:
Cengage Learning
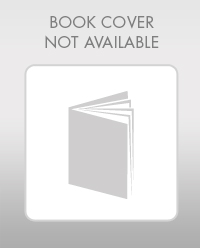
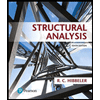
Structural Analysis (10th Edition)
Civil Engineering
ISBN:
9780134610672
Author:
Russell C. Hibbeler
Publisher:
PEARSON
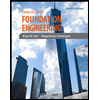
Principles of Foundation Engineering (MindTap Cou…
Civil Engineering
ISBN:
9781337705028
Author:
Braja M. Das, Nagaratnam Sivakugan
Publisher:
Cengage Learning
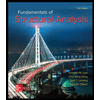
Fundamentals of Structural Analysis
Civil Engineering
ISBN:
9780073398006
Author:
Kenneth M. Leet Emeritus, Chia-Ming Uang, Joel Lanning
Publisher:
McGraw-Hill Education
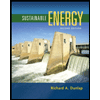
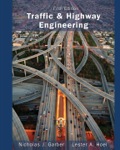
Traffic and Highway Engineering
Civil Engineering
ISBN:
9781305156241
Author:
Garber, Nicholas J.
Publisher:
Cengage Learning