Paramount Limited is reviewing the purchasing policy for one of its raw materials due to a reduction in production requirements. The material used evenly throughout the year is used for the company's products, the production of which is currently 285,000 units annually. Each finished unit of the product contains 0.4 kg of this material. 5% of the material is expected to be lost in the production processes. Purchases are usually made through Letters of Credits and can be made in multiples of 1,000 kg, with a minimum purchase order quantity of 1,000 kg. The cost of this raw material depends upon the purchase order quantity as follows: Order quantity (kg) Cost per kilogram ($) 1,000 2,000 3,000 4,000 6,000 12,000 10.00 9.80 9.65 9.50 9.35 9.20 The costs of placing and handling each order are $1,200, of which $300 is an apportionment of this cost which is not expected to be affected in the short term by the number of orders placed. The annual storage cost of stock is $20 per unit, of which only $16 is expected to be affected in the short term by the amount of stock held. The company expects the machine setup cost for each production run to be $450, and the estimated cost of pilferage is $5 per unit per annum. The bank will charge $250 for the bill processing fee for each transaction, and the company also estimates $3 per unit to prevent deterioration per annum. In addition, the lead time for the raw material is one month, and a minimum of 10,000 kg of safety stock is required.
Paramount Limited is reviewing the purchasing policy for one of its raw materials due to a reduction in production requirements. The material used evenly throughout the year is used for the company's products, the production of which is currently 285,000 units annually. Each finished unit of the product contains 0.4 kg of this material. 5% of the material is expected to be lost in the production processes. Purchases are usually made through Letters of Credits and can be made in multiples of 1,000 kg, with a minimum purchase order quantity of 1,000 kg. The cost of this raw material depends upon the purchase order quantity as follows: Order quantity (kg) Cost per kilogram ($) 1,000 2,000 3,000 4,000 6,000 12,000 10.00 9.80 9.65 9.50 9.35 9.20 The costs of placing and handling each order are $1,200, of which $300 is an apportionment of this cost which is not expected to be affected in the short term by the number of orders placed. The annual storage cost of stock is $20 per unit, of which only $16 is expected to be affected in the short term by the amount of stock held. The company expects the machine setup cost for each production run to be $450, and the estimated cost of pilferage is $5 per unit per annum. The bank will charge $250 for the bill processing fee for each transaction, and the company also estimates $3 per unit to prevent deterioration per annum. In addition, the lead time for the raw material is one month, and a minimum of 10,000 kg of safety stock is required.
Cornerstones of Cost Management (Cornerstones Series)
4th Edition
ISBN:9781305970663
Author:Don R. Hansen, Maryanne M. Mowen
Publisher:Don R. Hansen, Maryanne M. Mowen
Chapter20: Inventory Management: Economic Order Quantity, Jit, And The Theory Of Constraints
Section: Chapter Questions
Problem 7E: Ottis, Inc., uses 640,000 plastic housing units each year in its production of paper shredders. The...
Related questions
Question

Transcribed Image Text:Required:
(a)
(b)
(c)
Determine the annual usage of material, ordering cost per order, and holding cost per
unit for Paramount Limited.
Determine the EOQ without considering the bulk purchase policy.
Calculate the annual cost of pursuing an alternative purchase order policy; thus, advise
Paramount Limited on the purchase order quantity for the material to minimize cost.

Transcribed Image Text:Paramount Limited is reviewing the purchasing policy for one of its raw materials due to a
reduction in production requirements. The material used evenly throughout the year is used
for the company's products, the production of which is currently 285,000 units annually. Each
finished unit of the product contains 0.4 kg of this material. 5% of the material is expected to
be lost in the production processes. Purchases are usually made through Letters of Credits and
can be made in multiples of 1,000 kg, with a minimum purchase order quantity of 1,000 kg.
The cost of this raw material depends upon the purchase order quantity as follows:
Order quantity (kg) Cost per kilogram ($)
1,000
2,000
3,000
4,000
6,000
12,000
10.00
9.80
9.65
9.50
9.35
9.20
The costs of placing and handling each order are $1,200, of which $300 is an apportionment of
this cost which is not expected to be affected in the short term by the number of orders placed.
The annual storage cost of stock is $20 per unit, of which only $16 is expected to be affected
in the short term by the amount of stock held. The company expects the machine setup cost
for each production run to be $450, and the estimated cost of pilferage is $5 per unit per annum.
The bank will charge $250 for the bill processing fee for each transaction, and the company
also estimates $3 per unit to prevent deterioration per annum. In addition, the lead time for the
raw material is one month, and a minimum of 10,000 kg of safety stock is required.
Expert Solution

This question has been solved!
Explore an expertly crafted, step-by-step solution for a thorough understanding of key concepts.
Step by step
Solved in 4 steps

Knowledge Booster
Learn more about
Need a deep-dive on the concept behind this application? Look no further. Learn more about this topic, accounting and related others by exploring similar questions and additional content below.Recommended textbooks for you
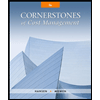
Cornerstones of Cost Management (Cornerstones Ser…
Accounting
ISBN:
9781305970663
Author:
Don R. Hansen, Maryanne M. Mowen
Publisher:
Cengage Learning
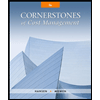
Cornerstones of Cost Management (Cornerstones Ser…
Accounting
ISBN:
9781305970663
Author:
Don R. Hansen, Maryanne M. Mowen
Publisher:
Cengage Learning