Webers is an omni-channel retailer with 250 stores throughout the United States and six distribution/fulfillment centers. Webers specializes in men's and women's clothing across numerous designers and styles. Previously, Webers had relatively no competition for its line of clothing and, as such, was focused more on its productivity rather than on service to its internet customers. Under the current order management process, a consumer would place an order on-line with Webers and receive a notification that the order was received. The order management system (OMS) would then check the availability of inventory for the order. If inventory was not available, the consumer would receive a notice for a backorder. If inventory was available, the OMS would send the order to the warehouse management system (WMS) to be scheduled for picking. Orders were picked in the order in which they were received. Once picked, the WMS would send the order to the transportation management system (TMS) to be scheduled for shipment. Once shipped, the consumer would be sent a notice of ship date. Under this process, the consumer could not pick delivery times when order- ing. Although this has a negative impact on Webers customer service, it allowed Webers to increase productivity in its fulfillment operations. Under increasing pressure from competitors, Webers decided to now allow the consumer to choose delivery times, e.g., next-day, two-day, etc. This was going to have a major impact on how the three systems (OMS, WMS, TMS) operated and exchanged information to facilitate the order management process. While the consumer is ordering, inventory avail- ability is checked in real-time. When the consumer chooses a delivery option, the OMS must communicate with the TMS to determine when the order needs to be tendered to the carrier at the fulfillment center to meet that delivery window. The TMS then communicates with the WMS to determine when the order needs to be picked. CASE QUESTIONS 1. Create process maps for the "before" and "after" order management processes. Use Figure 8.15 as a guide. Start from when the consumer places the order and end when the shipment is made.
Webers is an omni-channel retailer with 250 stores throughout the United States and six distribution/fulfillment centers. Webers specializes in men's and women's clothing across numerous designers and styles. Previously, Webers had relatively no competition for its line of clothing and, as such, was focused more on its productivity rather than on service to its internet customers. Under the current order management process, a consumer would place an order on-line with Webers and receive a notification that the order was received. The order management system (OMS) would then check the availability of inventory for the order. If inventory was not available, the consumer would receive a notice for a backorder. If inventory was available, the OMS would send the order to the warehouse management system (WMS) to be scheduled for picking. Orders were picked in the order in which they were received. Once picked, the WMS would send the order to the transportation management system (TMS) to be scheduled for shipment. Once shipped, the consumer would be sent a notice of ship date. Under this process, the consumer could not pick delivery times when order- ing. Although this has a negative impact on Webers customer service, it allowed Webers to increase productivity in its fulfillment operations. Under increasing pressure from competitors, Webers decided to now allow the consumer to choose delivery times, e.g., next-day, two-day, etc. This was going to have a major impact on how the three systems (OMS, WMS, TMS) operated and exchanged information to facilitate the order management process. While the consumer is ordering, inventory avail- ability is checked in real-time. When the consumer chooses a delivery option, the OMS must communicate with the TMS to determine when the order needs to be tendered to the carrier at the fulfillment center to meet that delivery window. The TMS then communicates with the WMS to determine when the order needs to be picked. CASE QUESTIONS 1. Create process maps for the "before" and "after" order management processes. Use Figure 8.15 as a guide. Start from when the consumer places the order and end when the shipment is made.
Practical Management Science
6th Edition
ISBN:9781337406659
Author:WINSTON, Wayne L.
Publisher:WINSTON, Wayne L.
Chapter2: Introduction To Spreadsheet Modeling
Section: Chapter Questions
Problem 20P: Julie James is opening a lemonade stand. She believes the fixed cost per week of running the stand...
Related questions
Question

Transcribed Image Text:Figure 8.15
Customer Wait Time (CWT)
Build/Outsource
No
(1)
(2)
(3)
(6)
(7)
ID or forecast
ID
Current
Yes ID
Local Yes
Repair/
Diagnose
Capacity
Capacity
Inv.
Inventory
Maintenance
Required
Adequate?
Req's
Available?
Reserve
Inventory
Perform
Maintenance
Update
Make
Vehicle
Vehicle
or Repair
Readiness
Available
Labor
Space
No
Reschedule
No
Prepare/
Place Order
Receive
Enter, &
Validate
Order
Receive
Inventory
Select
Plan
and
Determine
Consolidate and
Order
Route
Build Shipments
Loads
Carriers
and
Rate
Receive Pick
Product Product
Load
Vehicle
and
Generate Product
Deliver
Ship
Dly Date
Shipments
Shipping
to
Customer
Site
Docs
D1.2
D1.3
D1.4
D1.5
D1.6
D1.7
D1.8
DI19
D1.10
D1.11
From Make
or Source
Invoice &
Receive
Payment

Transcribed Image Text:CASE 8.2
Webers, Inc.
Webers is an omni-channel retailer with 250 stores throughout the United States and six
distribution/fulfillment centers. Webers specializes in men's and women's clothing across
numerous designers and styles. Previously, Webers had relatively no competition for its line
of clothing and, as such, was focused more on its productivity rather than on service to its
internet customers.
Under the current order management process, a consumer would place an order on-line
with Webers and receive a notification that the order was received. The order management
system (OMS) would then check the availability of inventory for the order. If inventory
was not available, the consumer would receive a notice for a backorder. If inventory was
available, the OMS would send the order to the warehouse management system (WMS)
to be scheduled for picking. Orders were picked in the order in which they were received.
Once picked, the WMS would send the order to the transportation management system
(TMS) to be scheduled for shipment. Once shipped, the consumer would be sent a notice
of ship date. Under this process, the consumer could not pick delivery times when order-
ing. Although this has a negative impact on Webers customer service, it allowed Webers to
increase productivity in its fulfillment operations.
Under increasing pressure from competitors, Webers decided to now allow the consumer
to choose delivery times, e.g., next-day, two-day, etc. This was going to have a major impact
on how the three systems (OMS, WMS, TMS) operated and exchanged information to
facilitate the order management process. While the consumer is ordering, inventory avail-
ability is checked in real-time. When the consumer chooses a delivery option, the OMS
must communicate with the TMS to determine when the order needs to be tendered to the
carrier at the fulfillment center to meet that delivery window. The TMS then communicates
with the WMS to determine when the order needs to be picked.
CASE QUESTIONS
1. Create process maps for the "before" and "after" order management processes. Use
Figure 8.15 as a guide. Start from when the consumer places the order and end when
the shipment is made.
Expert Solution

This question has been solved!
Explore an expertly crafted, step-by-step solution for a thorough understanding of key concepts.
This is a popular solution!
Trending now
This is a popular solution!
Step by step
Solved in 4 steps with 2 images

Recommended textbooks for you
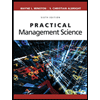
Practical Management Science
Operations Management
ISBN:
9781337406659
Author:
WINSTON, Wayne L.
Publisher:
Cengage,
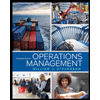
Operations Management
Operations Management
ISBN:
9781259667473
Author:
William J Stevenson
Publisher:
McGraw-Hill Education
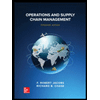
Operations and Supply Chain Management (Mcgraw-hi…
Operations Management
ISBN:
9781259666100
Author:
F. Robert Jacobs, Richard B Chase
Publisher:
McGraw-Hill Education
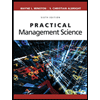
Practical Management Science
Operations Management
ISBN:
9781337406659
Author:
WINSTON, Wayne L.
Publisher:
Cengage,
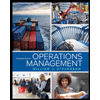
Operations Management
Operations Management
ISBN:
9781259667473
Author:
William J Stevenson
Publisher:
McGraw-Hill Education
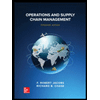
Operations and Supply Chain Management (Mcgraw-hi…
Operations Management
ISBN:
9781259666100
Author:
F. Robert Jacobs, Richard B Chase
Publisher:
McGraw-Hill Education
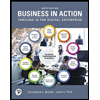
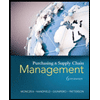
Purchasing and Supply Chain Management
Operations Management
ISBN:
9781285869681
Author:
Robert M. Monczka, Robert B. Handfield, Larry C. Giunipero, James L. Patterson
Publisher:
Cengage Learning
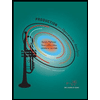
Production and Operations Analysis, Seventh Editi…
Operations Management
ISBN:
9781478623069
Author:
Steven Nahmias, Tava Lennon Olsen
Publisher:
Waveland Press, Inc.